東芝機械は5月17から19日まで静岡県の沼津本社工場と御殿場工場で「東芝機械グループソリューションフェア2018」を開催する。最新の超微細加工機やマシニングセンタ(MC)、成形機など同社の最新加工技術を展示するほか、セ…
―成形をゆく―
不二精工(大阪市西淀川区)
ゼロ・ディフェクト(ZD)と言う成形加工において最高で最大の品質目標に挑戦する成形メーカーに遭遇した。10年前に訪問したことのある会社は、すっかり成形工場を変えていた。「不良品を作らない」「不良品を作ろうと思っても作れない」とする車載用電子部品の成形加工ラインは、ロボットが導入され、一段と知能化を高めていた。考え始めたのは、前回の訪問した頃、弱電の電子部品から次第に車載用に比重を増し、新しい成形加工法が求められていた頃。具体的に言えば、7、8年前に人の手を一切触れさせないで成形品を生産するフープラインを開発した。ただし、当時の生産ラインは、人手を無くすことが主目的で、人の手でやれば「組み間違いを発生させる」「変形させる」「一定時間内に成形することで品質を安定させる」など今のZD発想は全くなかった。不二精工(濱野雅夫社長)の新インサート成形ラインは、驚いた。
それはZDを可能にする「新インサート成形ライン」と名付けられていた。昨年の2014年に2台、15年に2台の計4台の6軸ロボットを導入し、量産成形の試運転をしていた。
システムは、真ん中にロータリテーブル付きの立形射出成形機1台を配置し、その前後工程に世界最速(往復動作0・31秒)の6軸ロボット各2台と部品ストッカーを装備した。システムは、幅2・5m×奥行き6・5m。最大の特長は、成形機を安定して働かせる知能化ロボット。
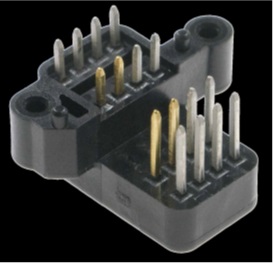
工程は、6軸ロボットでワークを掴み、成形機に挿入。成形後検査し、トレーに積み、トレーを何段か重ねてラックに収納するまで。その間、ワークには人の手が一切触れることがない。ロボットによるロボットの成形加工とでもいう新しい成形システムになっている。仮にロボットがミスをしても「異常発生!」と成形品はその場で弾き出され、最終工程は良品しか辿りつけないラインになっている。
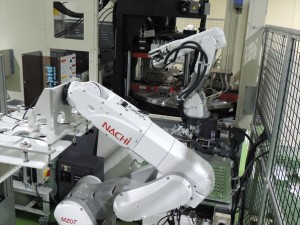
仕組みを考えた和田幸治総務課長は「ロボットはトレーを交換し、電子部品を4個一緒に掴み、反対側の手でもう4個一緒に掴んで金型に入れ、金型に成形品を入れるのをカメラで確認する。成形を終えて部品が出てきた後、奥の試験器装置に運び、1秒間に1000Vの耐電圧を掛ける」と、不良品を作れない新インサート成形の第一歩を評価する。金型の穴にピン1本を入れるクリアランスは100分の3と言うからかなりの高度作業が伴う。
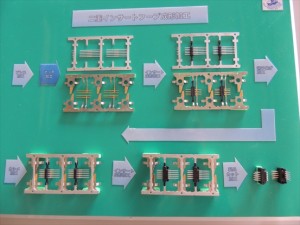
「まだまだ未完成。チョコ停をするためロボットの微細な動きを丸1日観察している時もある」(和田課長)と謙遜するが、かなり現場に馴染んできたようだ。また、「他のインサートフープラインは、成形機とプレスの設備を上手く使いこなし、なおかつ成形金型だから、プラスチックしか成形してはダメだとするのでなく、成形金型の中でカシメ、成形することも実現した」。残念なのは秘守義務を伴う成形品のため、ここではお見せできない。代わりにロボットラインのワークの類似品はこれ(写真①)。
写真1と2は、日本ロボット工業会が推進する「ロボット補助金」を活用することで可能になった。「ゼロ・ディフェクトと海外のメーカーに打ち勝つコスト削減」が評価された。仮に海外に技術が流失しても、さらにその上を行く技術の開発や日本に仕事を残す、引き戻す、なおかつ潤ったものは従業員に還元するなどの考えを具現化した。
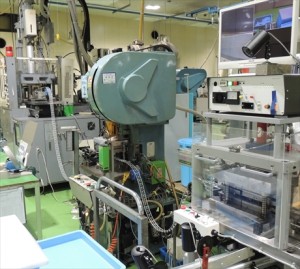
フープ成形が布石
新インサート成形ラインは、現在の同社の主力成形であるインサートフープ成形が開発の布石になっている。
それは、設備間を製品そのままの材料状態で送っていく帯状のこと。プレス→射出成形→プレス→射出成形を1本のラインで繋ぎ、異種材料を一体成形する。途中で電子部品1本1本の足に1秒間に1000Vの耐電圧を掛け、性能検査も兼ねる作業を行う。
そのインサートフープラインは、全長25m。最初のワークが誕生するまで約45分掛かるが、出始めたら4秒に1個ずつ部品は作られる。
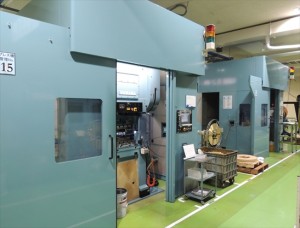
この自動化成形ラインに車載用電子部品が飛びついた。最も数多く出る成形品は月産10万個の非接触ブレーキセンサもあれば最も少ないのは同3000個の同高級ブランド車種部品もある。品種で言えば車載が30品種ぐらい。納入ユーザーは、車載ユニットメーカーはじめ国内主要メーカーなどが名を連ねる。今では、同社製の成形部品は、自動車、携帯電話、一般家電、ヘルスケアなどにとって無くてはならない存在となっている。
車載用電子部品は0・2㎜~0・1㎜のレベルの寸法精度に入っていないと組み立てられない。人の手がロボットに置き換わる最前線の技術が開花しようとしていた。
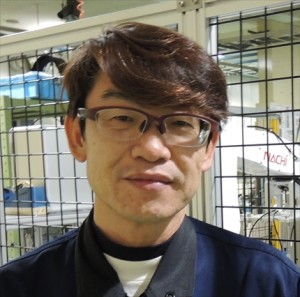
会社名:不二精工
住 所:大阪市西淀川区姫里3-5-4
設 立:1959年7月31日
資本金:1千万円
従業員数:33人
代表者:濱野雅夫氏
事業内容:精密金属プレス加工、精密樹脂成形加工、精密プレス金型設計・製作
主な納入先:パナソニック、パナソニック・デバイス、パナソニック・デバイス日東、村田製作所、京セラ、オムロン、デンソー、ソニーEMCS、スター精密、ローム、太陽ハトメほか。
金型新聞 平成27年(2015年)12月10日号
関連記事
EV化などによる金型需要の変化やAMをはじめとする新たな製造技術の登場など金型産業を取り巻く環境はこれまで以上に大きく変化している。金型メーカーには今後も事業を継続、成長させていくため未来を見据えた取り組みが求められてい…
次世代のリーダー育成 日本金型工業会(山中雅仁会長・ヤマナカゴーキン社長)は10月18日、上野精養軒(東京都台東区)で「第3回金型アカデミー・シニア金型マスター・金型マスター認定式」を開催した。金型製造に10年以上携わっ…
レーザー溶接・金型補修機器メーカーのテラスレーザー(静岡市駿河区、054-270-7798)はこのほど、光産業創成大学院大学(浜松市西区)主催の光技術を使った事業計画を競うビジネスコンテスト「フォトニクスチャレンジ202…
小型・軽量化、作業性向上 カネテック(長野県上田市、0268-24-1111)はこのほど、新型のマグネットLED電気スタンド「ME-3KJ」を発売した。光の拡散を抑えるデザインや電球を採用。作業者の視界に光が入りにくい仕…