金型業界含め国内製造業は慢性的な人手不足を抱え、加工や測定工程で自動化を図ることが大きな課題となっている。そのため、これまで複数の機械で加工していた加工工程を1台の機械に集約し、段取り工程の削減や短縮、さらに、工程間の搬…
【特集】匠の技を手に入れろ
金型はこれまで、金型職人の頭の中で製品形状や金型設計を描き、経験やノウハウで調整し、製造してきた。そして金型の「匠」の技は「背中」を見て学ぶもので、習熟への時間はとても長かった。しかし近年では、工作機械やCAD/CAMといったソフトウェアなど技術革新が進み、金型は従来の製造法から少しずつ変化している。また、匠の技を「学びのプロセス」無しに手に入れられる技術も登場している。それでは今後、匠の技がどのように変化するのか。多くの金型メーカーが技術者不足や次代への技術伝承を課題とする中、改めて「匠の技」の今と今後を追ってみる。
目次
PART1:兵庫県立大学国際商経学部・藤川健 准教授インタビュー
PART2:田口型範・田口順社長インタビュー
PART3:この技術で匠に近づける!! 5つの技術の先進事例
PART4:初級者を5年で匠に マツダの取組み紹介
PART5:記者の目
PART1
兵庫県立大学国際商経学部・藤川健 准教授に聞く、金型の「匠」とは①
「金型づくりの舵取る力」
金型の製造はこれまで金型職人と言われる技能者が製造してきた歴史があり、職人の頭の中で製品形状や金型設計を描き、経験やノウハウで調整し、製造してきた。だが、近年は工作機械やCAD/CAMといったソフトウェアなど技術革新が進み、金型は従来の製造法から少しずつ変化している。では、改めて「匠の技」とは何か。将来、匠の技がどのように変化すると予測されるのかを、兵庫県立大学の藤川健准教授に聞いた。
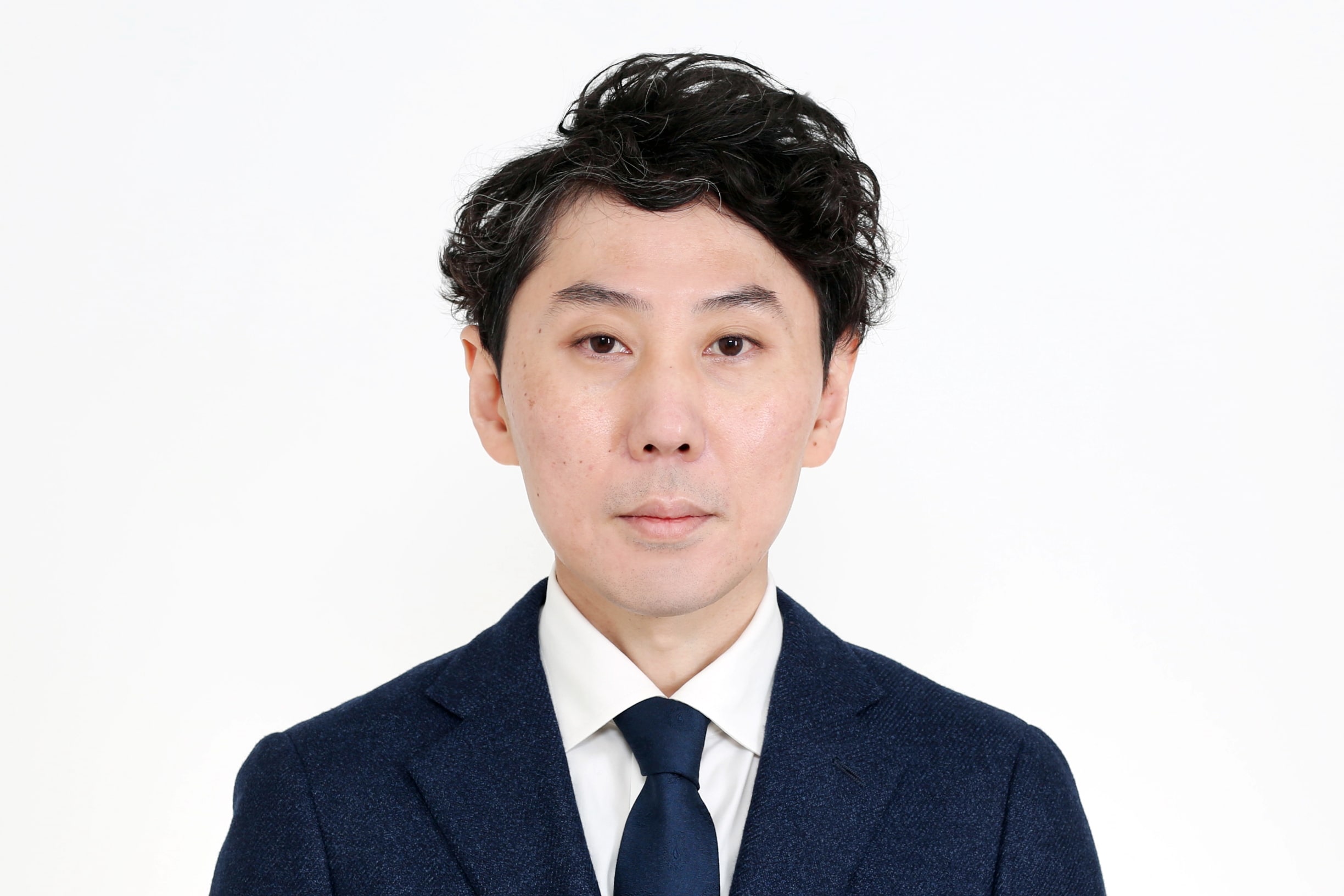
ふじかわ・たけし
2007年同志社大学大学院商学研究科博士後期課程単位取得退学後、同志社大学商学部講師、愛媛大学法文学部講師・准教授を経て、兵庫県立大学国際商経学部准教授として現在に至る。博士(商学)。主な著書は『アジア大の分業構造と中小企業』(14年)、『東アジア優位産業』(20年)。
金型の産業構造が「匠」を生んだ
金型の「匠の技」とは何か。
金型製造に必要な能力として「技能」と「技術」がある。技能とは、人に付随した熟達や勘、ノウハウと呼ばれる言語化しにくい暗黙知が含まれる能力で、技術とは言語化しやすく、データやプログラミングなど形式知を含む能力と定義できる。金型分野の「匠の技」は前者の技能の中にあり、近年は構造部設計や組立図作成など金型設計と、組立や調整といった仕上工程に技能者を配置するケースが多い。設計や磨きなど経験が必要な工程で熟達した技能が求められているからだと思う。
なぜ日本の金型メーカーに技能者が多いのか。
それは日本の金型産業の構造が影響している。これまで金型製造企業の競争力はQCD(品質・価格・納期)を高めることであり、いかに耐久性の高い金型を早く、低コストで製作できるかという改善能力が重要だった。そのため、特定の型種・サイズに絞った上で、全ての技能を極め、競争力強化を図ってきたと推測している。逆に中国などの金型企業は幅広い型種・サイズを受注した上で、徹底的な分業制をとっており、日本の金型メーカーのような技能向上は難しいかと思う。
技能に変化は。
変化する要因には技術革新と顧客ニーズがある。リーマンショック以降、ユーザーニーズがさらに、低価格・短納期になり、金型メーカーに求められるものが対応能力へと変化してきた。顧客の求めるQCDに応えるため、簡易な金型構造への変化、海外からの型材・部品の調達など様々な取り組みを行っており、近年は対応力の高さも匠といえる。
将来の匠の技とは。
機械やAIの進化で以前の匠の技をデータベース化する動きが活発だ。例えば、熟練者が行っていた見積もりもシステム化されており、標準化や技能レスが増えてきた。その中で人にしかできない要素に「判断能力」があるのではないか。例えば、最適な金型製作方法や部品選定などで、個々の企業に適した人の判断を伴う部分が将来の匠の技に変わる可能性がある。
PART2
田口型範・田口順社長に聞く、金型の匠とは②
デジタル技術が進化
鋳造用金型・木型などを手掛ける田口型範(埼玉県川口市)の田口順社長は、50年以上に渡って金型づくりに従事し、長年匠の技を目の当たりにしながら自身でも技を磨いてきた。その一方で、いち早くCAD/CAMや5軸マシニングセンタを導入するなど、技術革新にも積極的に取り組んできた。デジタル技術などによって、金型づくりの技術が加速度的に進化する中、田口社長が考える「これからの匠の技」について聞いた。
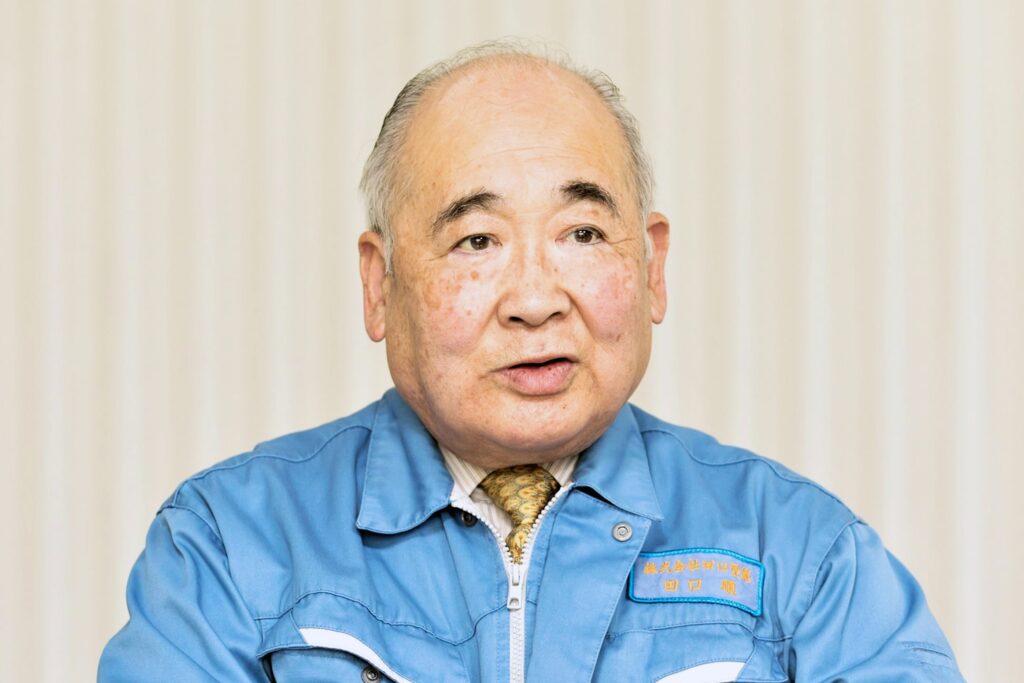
たぐち・じゅん
1949年生まれ、埼玉県出身。73年早稲田大学卒業後、田口型範入社。89年社長就任。2019年にはこれまでの功績が認められ、「旭日単光章」を受賞した。
匠以上の加工も可能に
私が大学を卒業して田口型範に入社した1970年代は、ならいフライス盤が金型加工の主力でした。この機械は木や樹脂製の模型(モデル)にならって同じ形に加工するという仕組みのため、「モデル精度=金型精度」と言われ、いかに高精度なモデルを作ることができるかが匠の技とされていました。
当時の匠は、のみ、かんな、ハイトゲージなどの道具を駆使して、+-0・1㎜の精度で高精度なモデルを作り上げていました。また、モデルに使用する材料の選定やモデルをどう分割するかなども匠の重要な技でした。
それが80年代に入ると、CAD/CAMが登場し、金型加工でもNC(数値制御)加工機が使われるようになりました。すると、モデルは実物からデータ化されるようになり、これまでの高精度なモデルを作るという匠の技は以前ほど重要ではなくなっていきました。
また、私が金型設計を始めた頃は定規などを使って手書きで設計しており、平行に線を引くことも匠の技の一つでした。それがドラフターによって簡単に平行線が引けるようになり、それだけでも感動した記憶があります。その後、2次元CADによってコンピュータ上での設計が可能になり、さらに3次元CADが登場し、より簡単に設計できるようになりました。
それからも加工機や工具、ソフトウェアの性能は向上し続け、現在ではデジタル技術の進化もあり、これまで以上に高精度な加工が可能になっています。どんなに匠の技が優れていると言っても、ミクロン台の精度は出せません。そうした面では機械には敵わないと考えています。
感覚、感性はこれからも
特に機械加工では匠の技を必要とする領域が少なくなっていると感じます。せめて言えるとするなら5軸加工。ここはまだ匠の技が発揮できる分野ではないでしょうか。効率良く加工するためのセッティングやCAMなどは多くの経験やノウハウを必要とするため、技術の力だけでは難しいと思います。
金型づくりは技術革新が進み続けると思います。遠隔操作で金型が作れたり、AIやロボットが金型を作ったり、SF映画のような世界が現実になるかもしれません。とはいえ、最終的に三次元のものを作るという匠の感覚や感性はこれからも必要ですし、機械やソフトウェアで補えない部分があるのも確かです。
これからの匠が気を付けるべきは、デジタルを信用しすぎないこと。数値や映像でみられるからといって現物を確かめずに加工して不良を出すなど、デジタル化の落とし穴はたくさんあります。腕の良い職人はいつでも謙虚です。技術が進歩し、時代が変わっても、こうしたものづくりの本質は変わりません。
PART3
この技術で匠に近づける
熟練者の手や体の動き、判断を真似て、それを20年かけて身につける—。いわゆる金型の「匠」の技は「背中」を見て学ぶもので、習熟への時間はとても長い。しかし、その匠の技を「学びのプロセス」無しに手に入れられる技術が登場している。多くの金型メーカーが技術者不足や次代への技術伝承を課題とする中、この技術は進化し注目されている。どのような技術があるのか、5つの技術の先進事例を追った。
プログラムの効率化
テンプレート化やパス最適化 〜プログラム作成を軽減〜
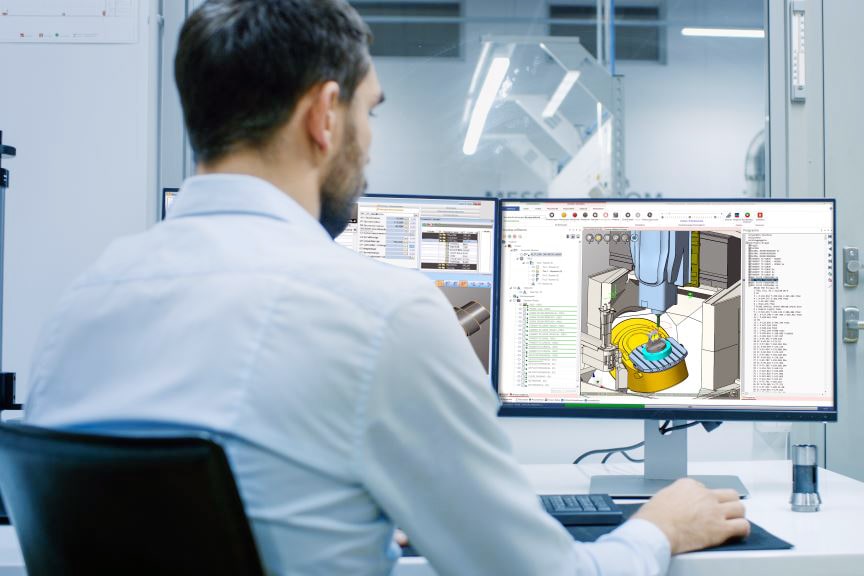
自動化や機械の稼働率向上に欠かせないのが、プログラムの安定的な供給だ。特に金型づくりでも自動化が加速している中、いかに効率よく正確なプログラムを作成できるかがより重要になっている。しかし、CAM工程をボトルネックにあげる金型メーカーは多い。
その理由の一つが、そもそもCAMの担当者自体が不足していることに加え、育成に時間がかかること。高度なCAM技能者にはソフトウェアのスキルはもとより、加工の知識も必要なので育成に時間がかかる。
もう一つは、人手不足のために、高度なCAM技能者が本来ならしなくても良い簡単なプログラム作成までしなければならない状況が多いことだ。あるプラスチック型メーカーの工場長は「能力の高いCAM技能者が必要なプログラム作成は全体の3割もない」と指摘する。
こうした課題を解決するため、誰でも簡単にプログラムを作成できたり、一部を自動で作成できたりするなど、CAMの技能者の負担を減らすことができる技術やツールが出始めている。
その技術の一つが「テンプレート化」だ。これまでそれぞれの金型メーカーが蓄積した材料や工具、加工形状などのノウハウに加え、機械メーカーらが蓄積したノウハウをソフトウェアとしてテンプレート化する。そのテンプレートから、自動で加工設定が割り振られることで、CAM操作を大幅に減らすことができる技術が登場している。複雑な形状では難しいが、シンプルな加工や、ノウハウや過去のデータが充実したテンプレートでは、自動でプログラム作成ができるようになっている。
また、自動で「パスを最適化」するソフトも登場しており、技能者の負荷を減らすことができる。技能者でなくても、自動で最適なパスを出せるので、加工の品質や加工速度の安定化にもつながる。
こうした技術を活用しても、現状では完全な自動化は難しかったり、データの築盛など個社での取り組みが必要だったりする。しかし、プログラム作成の手間を減らす新技術の開発は進んでいる。
補正技術
工具やワークの異常検出 〜機上で計測、補正へ〜
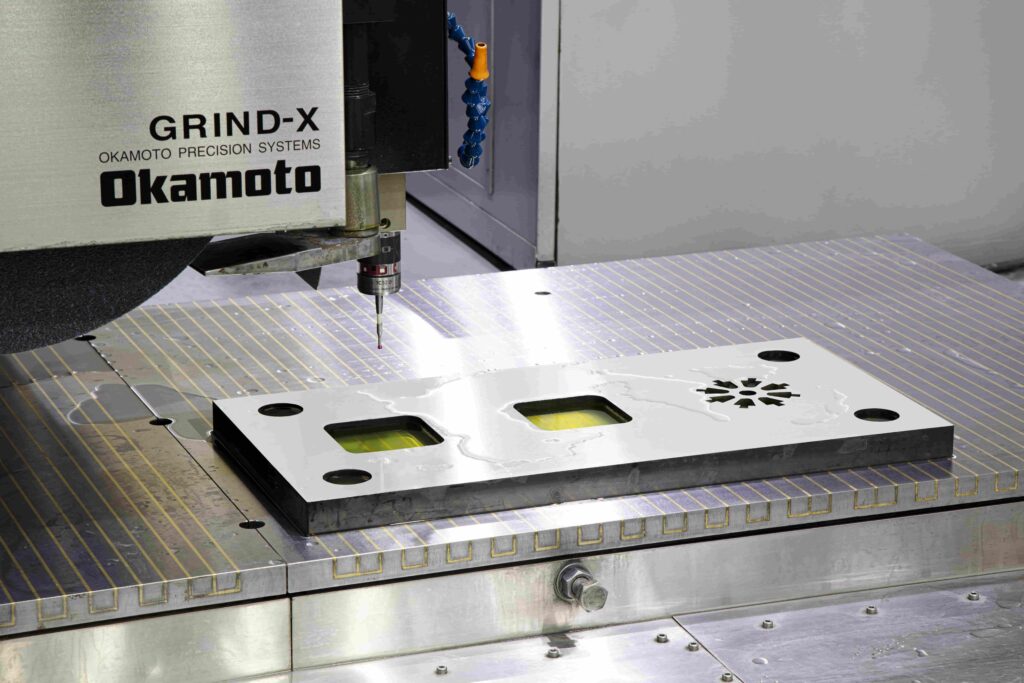
高精度加工を実現するには工具の芯出し、加工条件の設定、追い込み加工、すり合わせ後の調整などを行う熟練作業者が必要不可欠だが、近年、タッチプローブや工具測長器を使い、機上でワークや切削工具を計測し、元データとの比較や補正する技術が進化してきた。さらに、工作機械メーカー各社は、加工と機上計測を組み合わせた自動化提案を強めている。
オークマの「Hyper‐Surface」は加工プログラム補正機能を持ち、CAMから出力された加工データの指令位置の微小なバラつきや隣接する加工パス間のズレなど加工面不良につながる加工プログラムの乱れを自動で補正し、加工データの修正なしで加工面品位の向上を図る。
安田工業は加工回転数での工具の振れを計測し、刃先の振れが最も少なくなる工具の掴み方を機械が自動で探し出す「アンバランス計測」機能を提案。ミーリング加工では回転数が高くなると、切削工具のわずかなアンバランス(振れ)も振動源となり、加工品質の悪化の原因となり、機械が振れ量の最も小さくなる位相を自動で選択し、オペレータの負担も軽減。
三菱電機は独自開発したAI技術「Maisart」を同社製放電加工機に搭載し、加工状態をリアルタイムで検出。熟練作業者が行っていた加工条件の調整を自動化する。さらに、同技術を搭載したワイヤ放電加工機「MPシリーズ」は板厚が変化する段差部やノズルの離れ量に応じた加工条件の調整を行わず、高精度な加工を実現する。
熟練技能者の減少により、金型メーカーも人的な作業や調整を機械化、自動化することは競争力強化につながる。それを進めるために今後もメーカー各社の技術開発から目が離せない。
この技術に注目!
加工プログラムを自動補正・オークマ 門形マシニングセンタ「MCR-S」
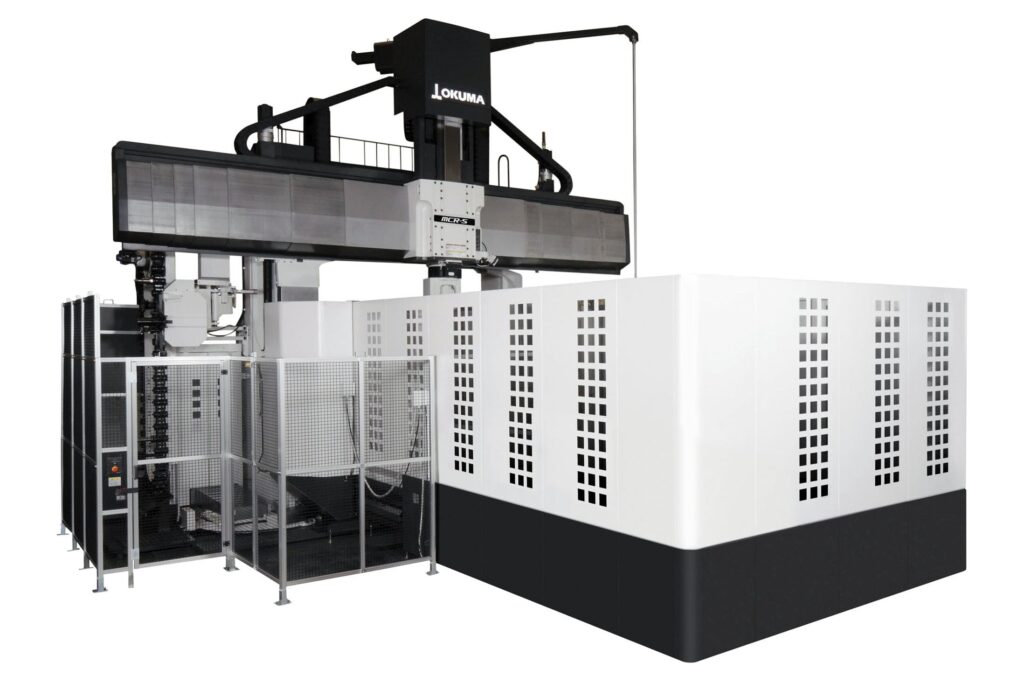
「MCR‐S」は、金型の荒加工から仕上げ加工までを1台でこなし、大幅な工程短縮を実現。
加工プログラム補正機能「Hyper‐Surface」搭載で、加工面不良につながる加工プログラムの乱れを自動補正し、加工面のスジ目がない高面品位加工を行う。磨きレスにも繋げることができる。加えて、タッチプローブと精度マスタを用いた3Dキャリブレーションの定期的な機械精度の点検、校正により、三次元計測機と同等の機上計測結果を一般工場環境下で実現する。
AIで加工条件を自動調整・三菱電機 Maisart(マイサート)
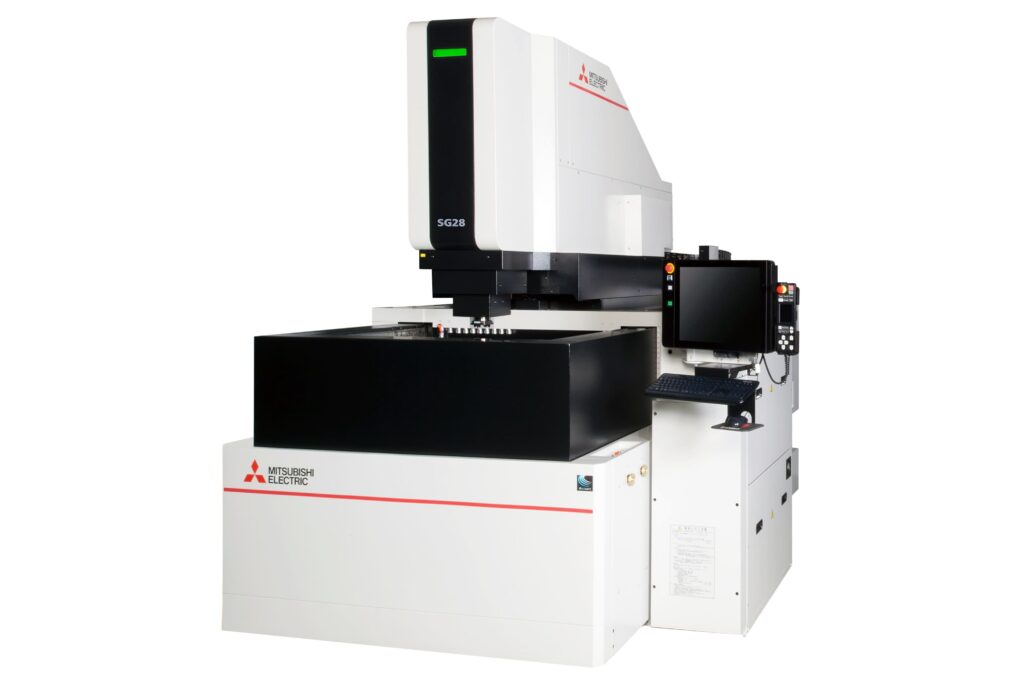
「Maisart」は三菱電機が独自開発したAI技術。同社製放電加工機に搭載することで、加工状態をリアルタイムで検出し、加工安定化のためにこれまで熟練作業者が行っていた加工条件の調整を自動化することができる。
ワイヤ放電加工機「MPシリーズ」では板厚が変化する段差部やノズル離れ量に応じた加工条件の調整を行わなくても安定した高精度加工が可能。形彫放電加工機「SVPシリーズ」「SGシリーズ」では小~中大物ワークでの安定加工を実現する。
工具の振れ最小の掴み方探す・安田工業 アンバランス計測
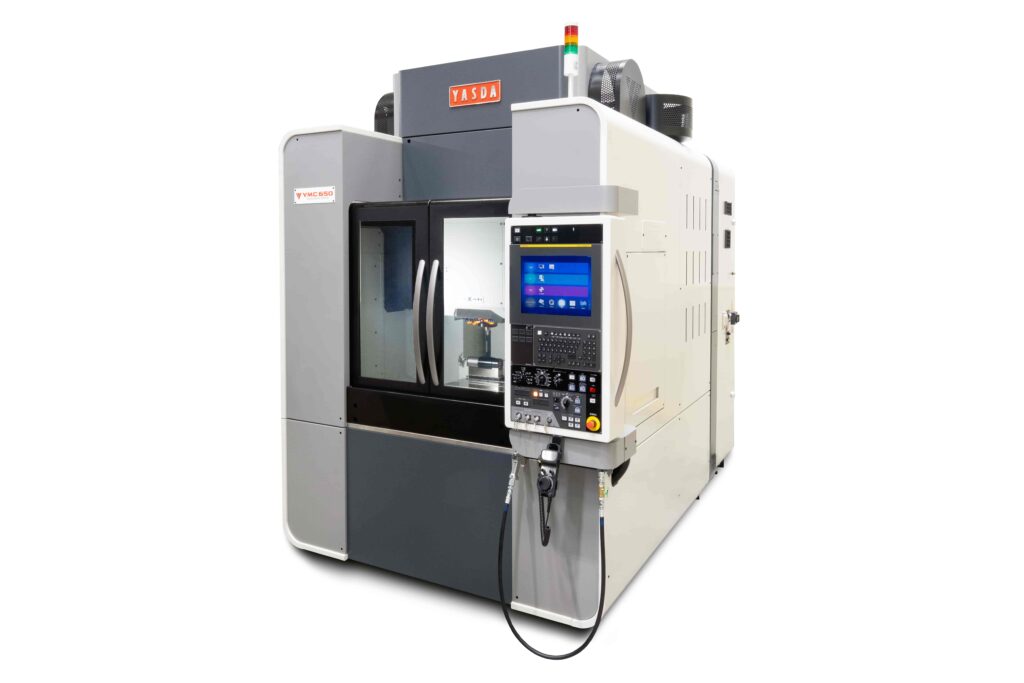
ミーリング加工において回転数が高くなると、切削工具のわずかなアンバランス(振れ)も振動源となり加工品質を悪化させる。「アンバランス計測」は、その刃先の振れが最も少なくなる工具の掴み方を、機械が自動で探し出す機能だ。
加工回転数での工具の振れを計測し、主軸を掴み直して振れ量が最も小さくなる位相を自動で選択する。これにより、振れと振動が最も少ない状況における加工が可能となり、オペレータの負担を軽減、加工品質を向上する。
磨きレス
工作機械でナノの面粗さ 〜超硬工具でも実現可能に〜
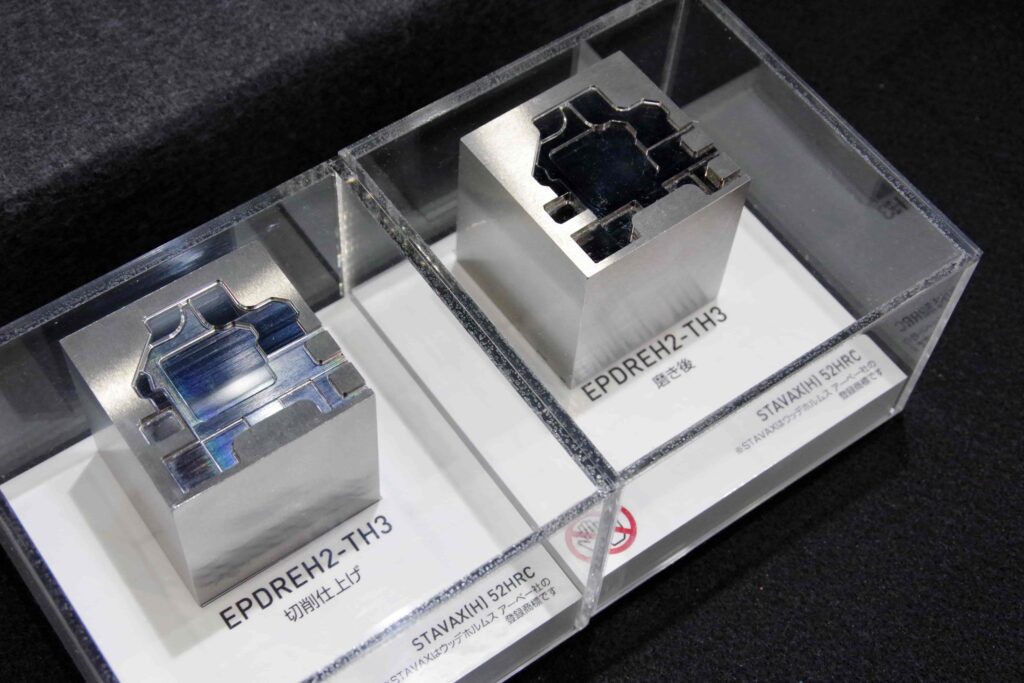
金型加工の最終工程である磨き。金型の品質を左右する重要な工程で、職人がセラミック砥石やダイヤモンドペースなどの道具を使いながら手作業で仕上げていく。そうした技能は長い年月をかけて鍛えられ、一人前になるまでに最低10年はかかるとも言われている。
しかし近年は、少子高齢化を背景とした労働人口の減少により、磨きができる熟練技能者が不足している。また、人手不足によって、磨き工程がボトルネックとなり、生産性の低下を招いているケースも少なくない。
こうした課題を解決するために、ここ最近注目を集めているのが、「磨きレス」だ。機械加工だけで、ナノレベルの面粗さを得ることができ、磨き工程の負担を軽減したり、工程自体を無くしてしまう技術のことを言う。
この「磨きレス」を実現する工作機械や切削工具の進化は日進月歩であり、これまで以上の加工精度や品質が可能になっている。工作機械では、6万回転の主軸を搭載した機種や振れ精度が1μm未満の高精度モデルなどが開発されている。
切削工具では、これまでのPCD(多結晶焼結ダイヤモンド)やCBN(立方晶窒化ホウ素)工具に加え、超硬工具でも「磨きレス」を可能にする工具が出始めている。独自のコーティングを採用し、高硬度鋼の加工でもCBN工具以上の面粗さを実現したり、刃形を改良し加工スジを抑制するなど種類は豊富だ。
その他、より良い面粗さを得ることできる加工プログラムを作成できるソフトウェアなど「磨きレス」を可能にする新技術が登場している。
この技術に注目!
筋の発生を抑制・オーエスジー 超硬防振型エンドミル立ち壁対応型「AE-VMFE」
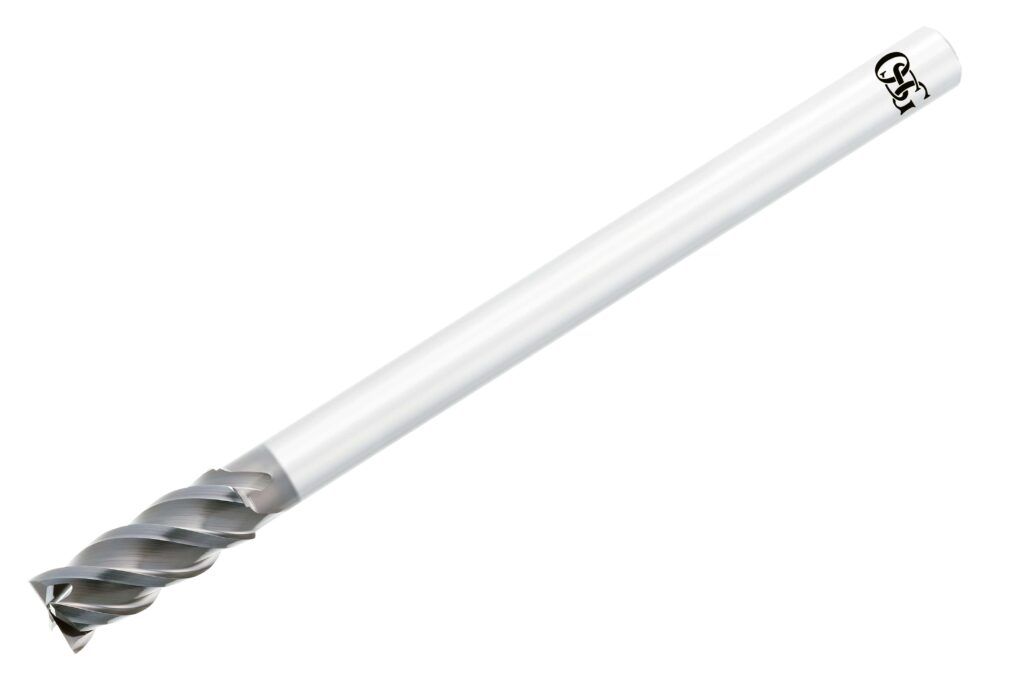
炭素鋼・合金鋼・ステンレス鋼からチタン合金・Ni基合金まで幅広い被削材に対応可能なAブランドの超硬防振型エンドミル「AE-VMシリーズ」に立ち壁対応型「AE-VMFE」を追加した。
2.5D刃長と刃太タイプのロングシャンク形状により、L/D=5以上の立ち壁を側面ステップ切削で高能率・高精度に加工。また、シャンク側端面のR形状により筋発生を抑制。
金型部品などの深い立ち壁加工やポケット加工に対応する。
見える化
機械や金型の状態を数値化 〜加工条件を最適化〜
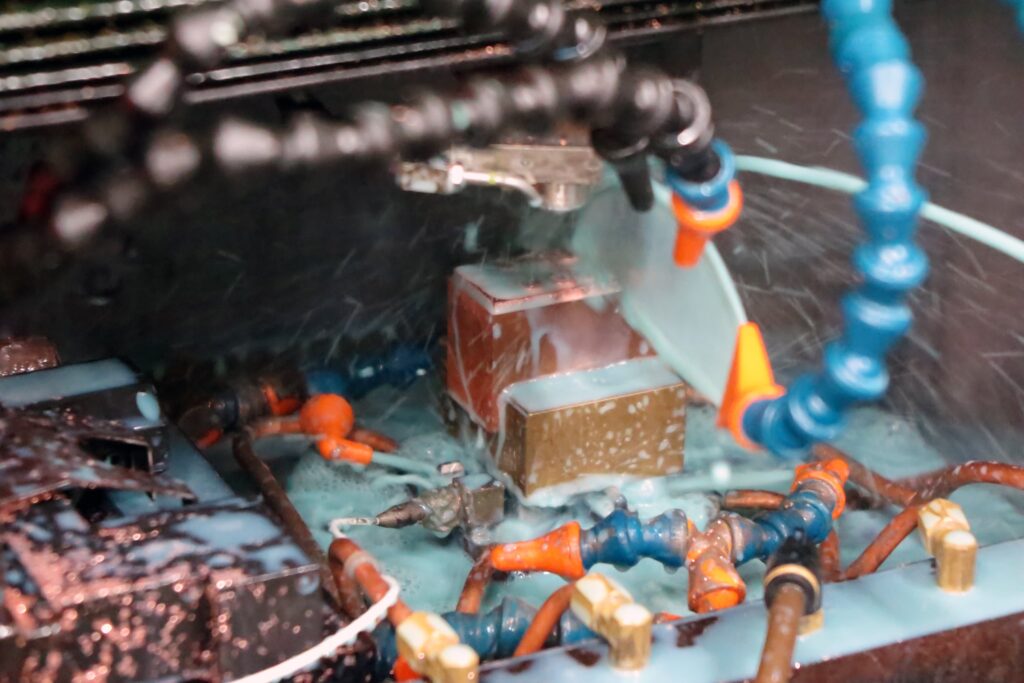
これまで加工機の状態や金型内部の変化を把握するには、熟練技術者の長年蓄積された経験や勘が不可欠だった。
加工機では、送り速度を上げるなど加工条件を厳しくすると、工具の欠損や機械の破損しやすくなり、機械の稼働停止、不良の発生につながる。そのため機械の状態を正確に把握しないと最適な条件を設定するのは難しかった。
また、金型内部の変化は、音や温度、振動、成形品の状態などあらゆるパラメータから予測するため、多くの経験やノウハウが求められる。加えて、成形中はブラックボックスとなり、リアルタイムで把握することは熟練技術でも困難なことだった。
しかし近年、センサ技術やITの進化によって、熟練技術者の技を数値化し、熟練度の低い技術者でも機械や金型の状態を「見える化」できるようになってきた。振動センサや温度センサ、電流センサなど様々なセンサとそれらをつなぐネットワークシステムによって、「見える化」を実現している。
マシニングセンタや放電加工機などといった加工機に各種センサを取り付け、機械の状態データを取り込むことで、自動で制御や加工条件を最適化。機械の性能を最大限引き出すことが可能で、加工時間の短縮や工具寿命を向上させることができる。
金型にも温度センサなどを搭載することで、内部の状態を「見える化」できる。最近では有線だけではなく、無線でデータをパソコンなどに送ることができるシステムも多く登場しており、取り回しやすく、より導入しやすくなっている。
この技術に注目!
金型温度を可視化・匠ソリューションズ 「TWINDS-Tスタンダードキット」
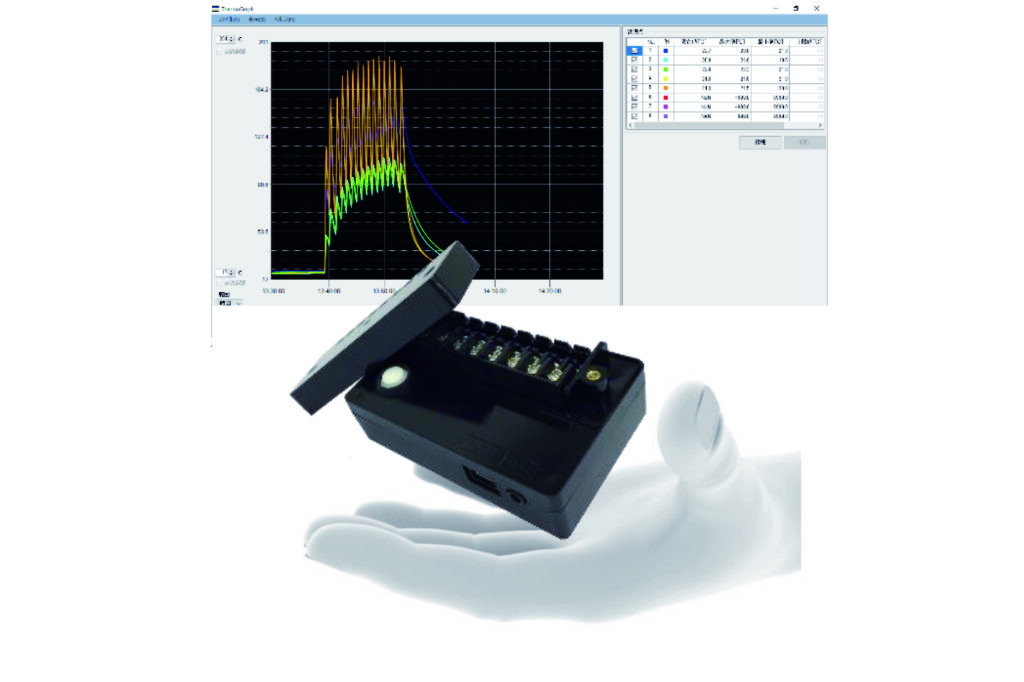
生産現場で鋳造・樹脂成型金型内部温度のリアルタイム表示やアラート表示を行う一方、遠隔地のPCに自動蓄積する。また、小型CPUボードや表示パネルのフルパッケージ提供で簡単にシステムの実現が可能。金型温度を可視化することで、人的エラーの回避や温度の変化点から起因する品質問題、立ち上げロスの早期分析や究明に役立つ。
ワイヤレス通信で作業の邪魔をせず断線を防ぐ他、取り回しも容易。本体も小型・防塵防水化で、鋳造・冷却水など生産中の温度監視にも適する。
セッティング
段取りも研削も自動 〜工具測定データを蓄積〜
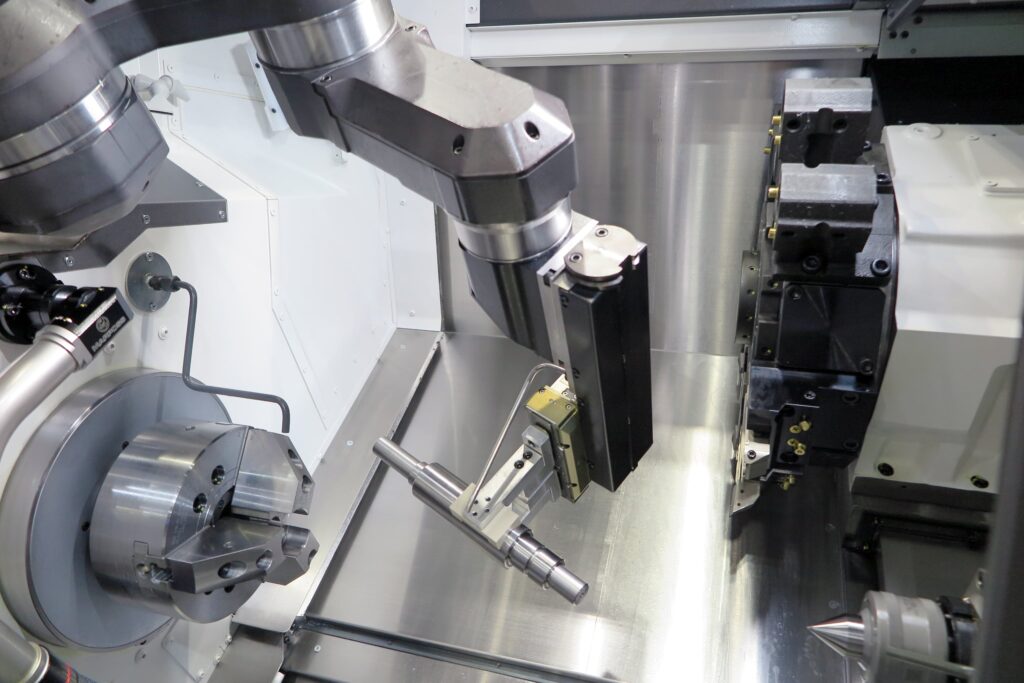
ワークの位置決め、工具の取り付け、加工条件の設定—。金型を加工するためのセッティングも長年の経験やノウハウが必要だ。しかしそうした匠の技術を補完できる新たなシステムや機器が登場している。
加工の基準点を測定する心出し。それを自動でできるシステムがOKKの「3Dマイスター」。マシニングセンタの主軸近くのカメラで機上のワークを撮影。そのデータを3Dモデルに変換し指定した点をタッチセンサで計測し、その点を機械座標で基準点と認識する。この一連のプロセスはタブレットで操作できる。
岡本工作機械製作所の「SELF」はワークや砥石の位置決めに加え、平面研削までを全自動でできるシステム。テーブルに載せたワークと砥石を自動検知し、総取り代を入力すると加工が始まる。加工したワークは自動で測定、誤差補正の加工もする。
補正技術を活用しワークを自動でセッティングできるのはオープン・マインド・テクノロジーズ・ジャパンの5軸加工向けCAM「hyperMILL」。ベストフィットソリューションという機能で、ワークをタッチセンサで計測し、ワークとNCデータとの誤差をCAMで補正する。緻密な位置決めを要する大型ワークのセッティングに有効という。
ホルダにセットした工具の測定データを蓄積できるのはエヌティーツールのツールプリセッタ「イージスアイ」。非接触で高精度に測定したデータをサーバに蓄積し、そのデータを工作機械に転送して活用することができる。
この技術に注目!
金型の心出しを自動化・OKK 3Dマイスター
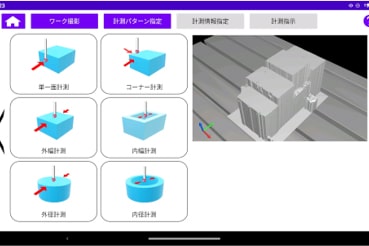
「3Dマイスター」は、タッチセンサシステムと最新のマシンビジョン技術である3Dカメラを連動させ、金型などの心出し作業を自動化できるシステム。
3Dカメラで撮影したワークは、タブレット上に3次元モデルとして表示。それの計測したい個所をタッチするだけで、心出しに必要な計測動作を簡単に行える。
経験やノウハウ、作業の手間を要していた従来のマニュアル操作は必要なくなり、スマホを操作する感覚で心出し作業ができる。
この技術に注目!
アタリ出し作業を自動化・黒田精工 平面研削盤自動アタリ出し機能「Smart-Contact」
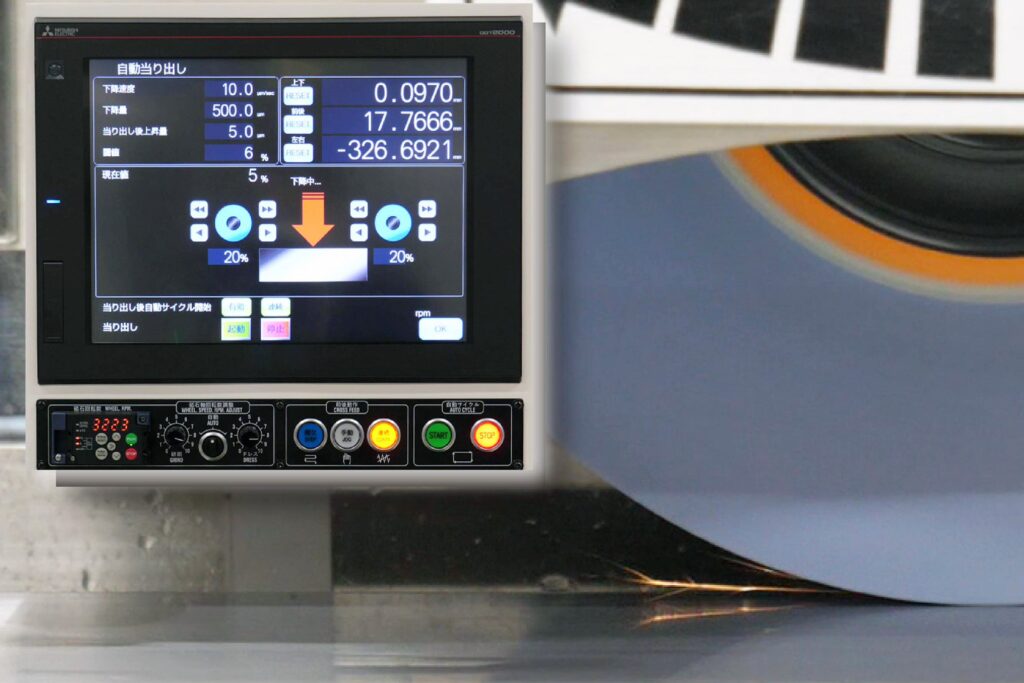
アタリ出し作業を自動化し、熟練度を要する繊細な作業を誰でも安全に行うことができる機能。
砥石とワークの自動接触検知機能に加え、砥石タッチ後の自動加工スタート機能も搭載。自動加工開始までの工数削減と加工品質の安定化を実現する。また、アタリ出し作業時の過負荷や事故防止、作業者のストレス軽減にもつながる。
操作は砥石を大まかにワークに接近させてスタートボタンを押すだけで行える。動作開始後、作業者は他の作業に従事することができる。
PART4
マツダ 初級者を5年で匠に
匠と呼ばれる金型づくりの熟練者と経験の浅い初級者との違いは何だろうか。例えば匠は金型を研削するとき目線や手、身体をどのように動かしているのか—。それをモーションキャプチャーで見える化し技能指導に生かしているのが自動車メーカーのマツダだ。技能のメカニズムをデジタル技術で解明し、習熟に長年を要していた匠の技を次代に継承している。
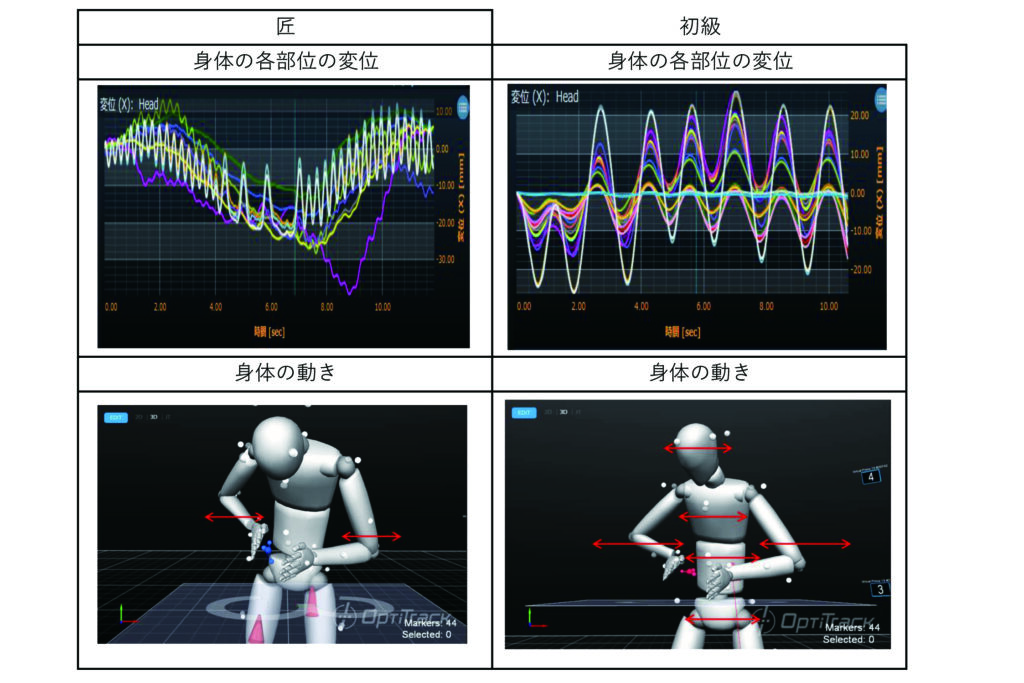
匠の動きを分析し技能伝承
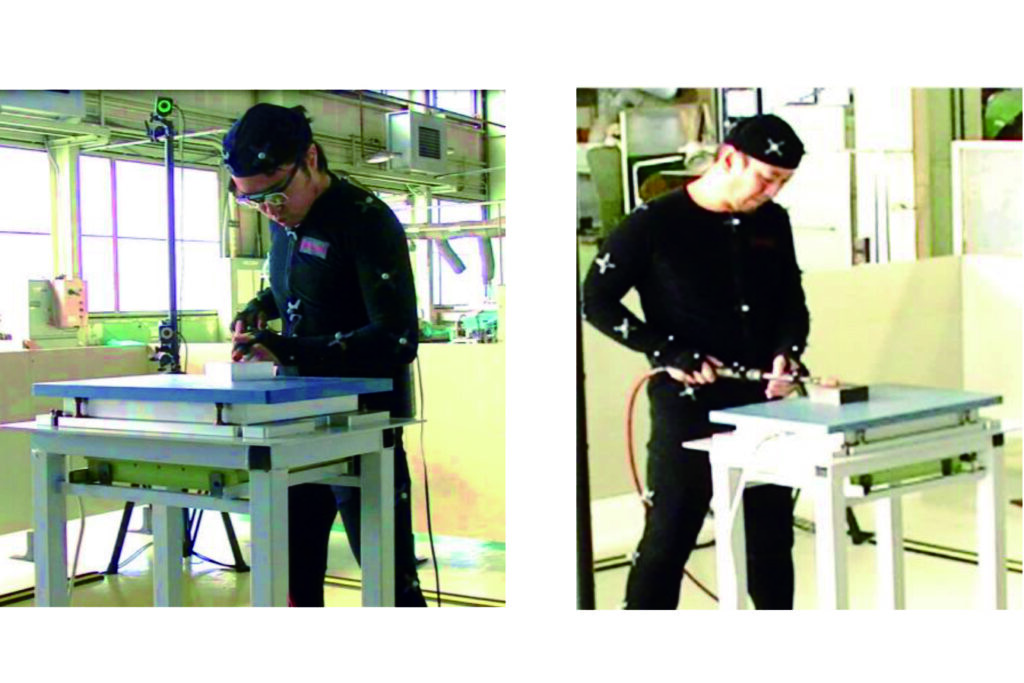
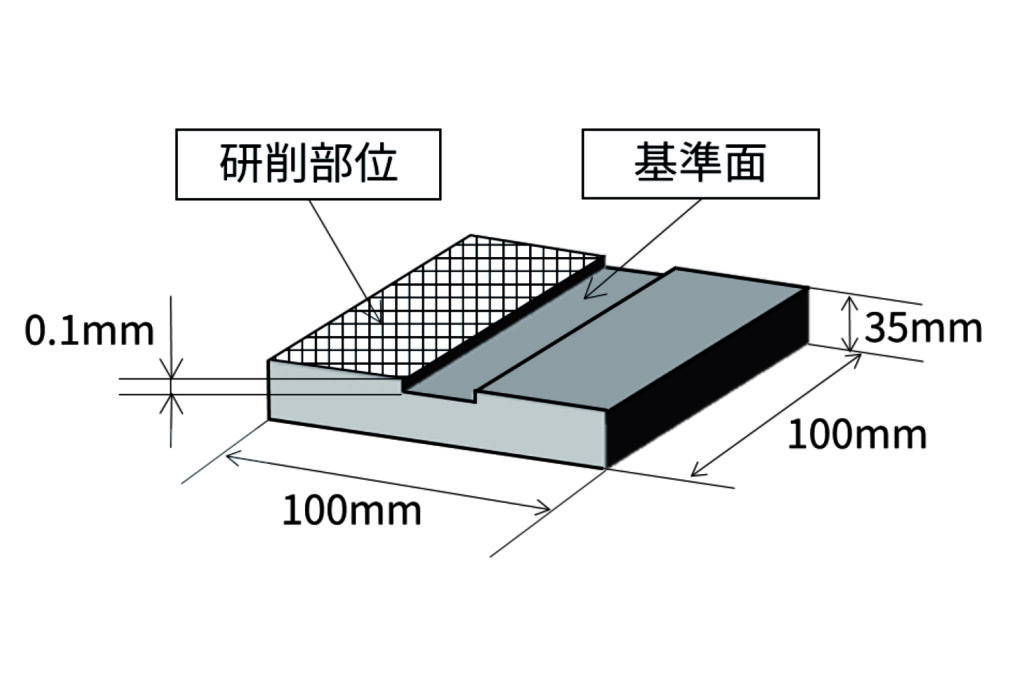
ゴーグルをかけ、帽子を被り、黒いボディスーツを着た技能者が作業台に載せたワークをグラインダーで研削する。ワークには基準面(0.1㎜の段差)があり、同じ高さになるように足を踏み込み、砥石をあて、左右に振る。マツダのプレス金型などを手掛けるツーリング製作部で行うモーションキャプチャーの様子だ。
帽子とボディスーツのあちこちには41個のマーカーがついている。ゴーグルやグラインダーにも複数のマーカーがついており、これらを8台のカメラで撮影し、各マーカーの3次元座標の動きを計測する。左右の足元と作業台の3カ所にはプレートがあり、それにかかる反力も測る。
測るのは、技能者の目線や頭、肩、腕、腰、足など各部位の動き、速度、加速度。そして作業台や床にかけた力。いわば目や身体をどのように動かしグラインダーを操作したか。それぞれ数値とグラフになって表れる。それをもとに筋活動量も解析する。
匠の技のメカニズム解明
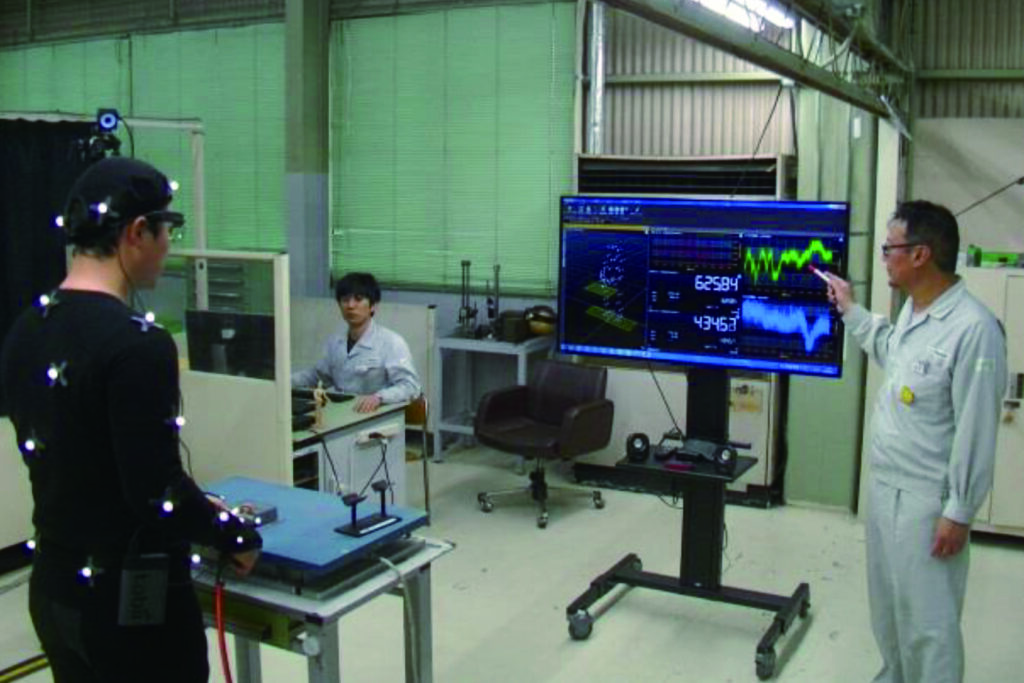
金型の仕上げ技能は、20年以上の長年の経験やノウハウによるミクロン台の精度が求められる。匠に共通する特有の身体やグラインダーの操り方は—。ツーリング製作部では、このモーションキャプチャーを活用し、匠の技能のメカニズムを解明している。
5人の匠がワークを研削する同じ作業を計測。身体の各部位の速度やグラインダーの重心など69の変数から、研削に最も関係の深い6つの変数を抽出し、それをさらに分析。匠の動きには「ツール保持部変位」や「腰加速度」「踏み込み動作」など6つの主成分(技能特長)が密接に関わっていることを算出した。
このメカニズムから導き出せるのは、初級者と匠との違いだ。例えば、初級者は体幹や腕、足のバランスが不安定なのに対し、匠は均一。匠は身体の軸がしっかりしており左右のブレが少ない。グラインダーに効率良く力を伝え、疲れにくい作業で高い品質に仕上げていることがわかるという。
カルテで技能定量評価
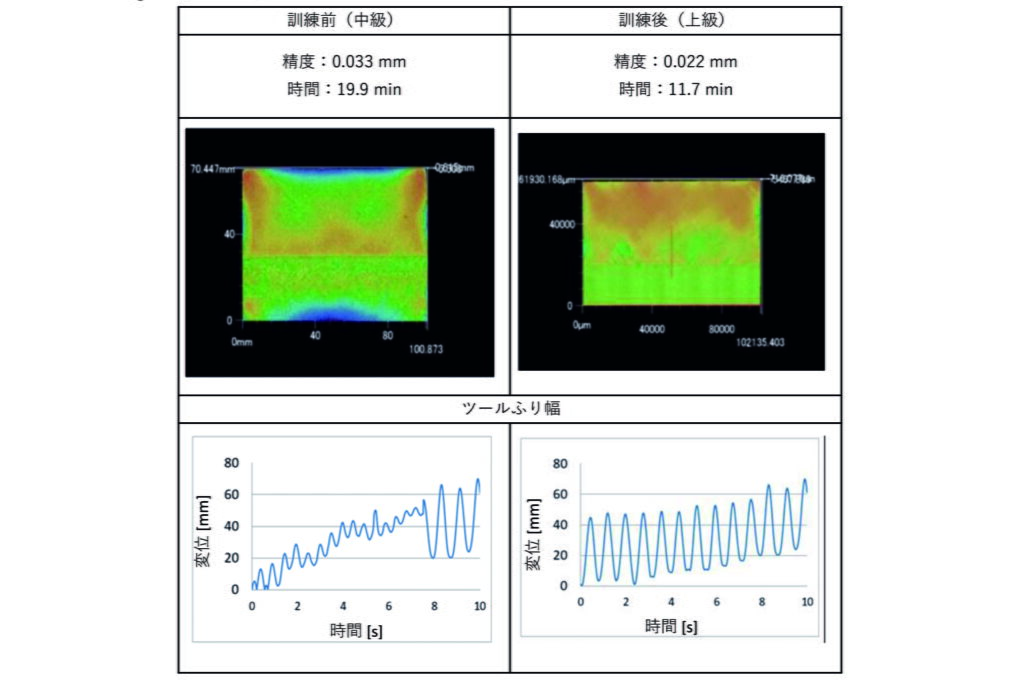
そしてこの計測・分析結果をもとに、「技能カルテ」と呼ぶ技能の診断記録を作成する。グラインダーを動かす振り幅や速度、視線の動作、磨きに重要な6つの主成分を数値で表示。自らの長所や短所、匠とのレベルの差を比較、評価できる。さらには筋活動量から作業中の身体への負荷もわかるという。
この技能カルテは技能者の技能訓練の指導に用いる。技能カルテと作業中の動画を匠と比較し、匠の基準値に近づくように訓練する。訓練では匠の動きを倣える治具やセンサを使い、グラインダーを操作する。これを繰り返し補正することで匠の動きに近づける。
労働者が減少、技能伝承が課題に
ツーリング製作部がモーションキャプチャーによる技能伝承システムの開発に取り組み始めたのは今から5年前。少子高齢化に伴い労働者が減少、高齢化する一方で、長年の経験や勘を必要とする金型は技能伝承に時間がかかり過ぎていた。技能を見える化することで伝承の時間を短くできないだろうか—。そんな直面する課題への挑戦がモーションキャプチャーを活用するきっかけだった。
モーションキャプチャーと技能カルテを用いる訓練は、ツーリング製作部の仕上げに関わる50人の技能者が受講(週2時間×4回)。江草秀幸主幹は「そのうち95%の技能が向上した」という。技能伝承システムによる取り組みは匠の技の伝承期間をこれまでの20年から5年へと短縮することを目標としており、「5年での育成の基盤ができた」(江草主幹)。
磨き・溶接への応用も
今後期待するのが、技能指導の多様化や異分野での応用だ。横山郁夫部長は「コロナ禍の中、遠隔地での指導、海外拠点の外国人技能者への指導にも生かせるし、研削で確立した訓練の仕組みはきっと溶接や磨きにも応用できる。金型づくりのカギを握るのは匠の技能。いかに伝承できるか、チャレンジを続けていく」。
PART5
記者の目
指先でミクロン台の凹凸を感じたり、最適な樹脂の流動構造を導き出したり。それらは今なお匠の技と呼ばれている。だが過去を振り返ると今は無き匠の技は少なくない。
例えば汎用機を五感で操る技や精緻な図面を描く技。その殆どはNC機やCADの登場で熟練度の低い人もできるようになった。金型づくりの進化はある意味、匠の技術の平準化ともいえる。
しかしその全てが置き換わると思わない。その一つが想像力だろう。良品を生み出す金型の仕組みとそれを作るプロセスを脳でイメージする。それが大切なのだとある金型の匠が話していた。
とはいえ技術の進化は金型づくりにおける多くの不可能を可能にしてきた。人の脳によるイメージングも機械やソフトに置き換わる未来が来るのだろうか。
金型新聞 2021年7月10日
関連記事
スプリングバック、材料特性のばらつきに対応 ハイテン材加工に不可欠とされるCAE解析。すでに多くの金型メーカーが活用し、生産性や品質の向上につなげている。近年は自動車部材のハイテン化が進み、これまで以上に強度の高い超ハイ…
「CASE」(コネクテッド、自動運転、シェアリング、電動化)に代表されるように、「百年に一度の変革期」と言われる自動車業界。金型にとってもその影響は大きく、舵取り次第では将来の成長を左右しかねない。特に、金型へのインパ…
自動車のボデー部品や排気系部品など手掛けるフタバ産業は1470MPa超ハイテン材の冷間プレス部品の量産を確立、今年1月に発売した新型プリウスに採用された。先代プリウスはホットスタンプを用いた部品を採用していたが、冷間プレ…
EV化などによる金型需要の変化やAMをはじめとする新たな製造技術の登場など金型産業を取り巻く環境はこれまで以上に大きく変化している。金型メーカーには今後も事業を継続、成長させていくため未来を見据えた取り組みが求められてい…