6000t級のダイカストマシン導入 リョービはこのほど、ダイカスト専業メーカーとしては日本で初めて、6000tクラスのダイカストマシンの導入し、「ギガキャスト」に参入すると発表した。2025年3月から試作サービスを開始す…
MOLDINO エンドミルケースを金型から製作
切削工具メーカーが金型からエンドミルケースを製作するー。そんなユニークなプロジェクトに取り組んだのが、金型加工向け切削工具を手掛けるMOLDINO(モルディノ)(東京都墨田区、03・6890・5101)。ケースの設計から金型の設計、製作、組立までを内製し、成形メーカーで量産した。すでに製作したケースは、同社のCBNエンドミルシリーズを収納し、市場に流通している。
金型加工のニーズを知るために製作
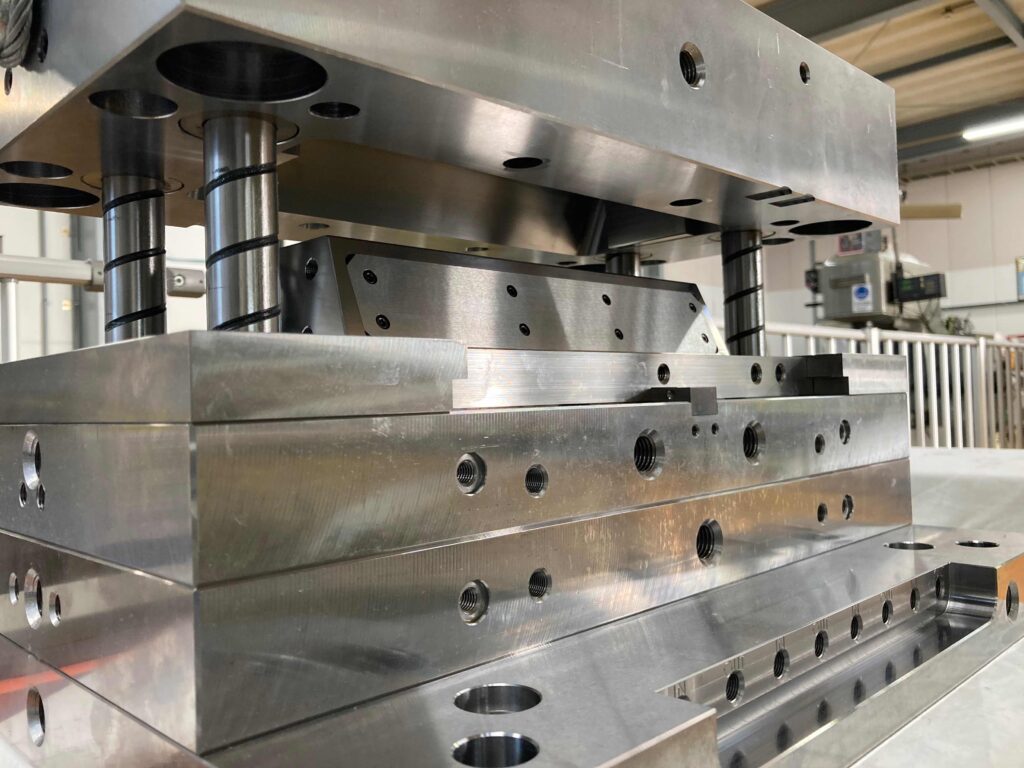
「金型加工における問題点や、そもそも金型メーカーは何を求めているのか。そういうところをしっかり知るために、まずは自分たちで金型を作って、学び、経験することが大事だと考えました。新しい製品や加工方法の開発はもちろん、営業担当にもポイントを理解してもらい、提案力を強化することも目指し、取り組みをスタートさせました」(ソリューション営業部長・木野晴喜氏)。
実は同社の金型づくりは今回が初めてではない。2018年に樹脂製コップの金型を製作。翌年の2019年に東京、名古屋で開かれた金型加工技術の専門展「インターモールド」で、金型とその金型を使って成形したコップを自社ブースに展示した。この取り組みは、2017年に現在の社名につながる「MOLDINO」ブランドを立ち上げたのがきっかけ。
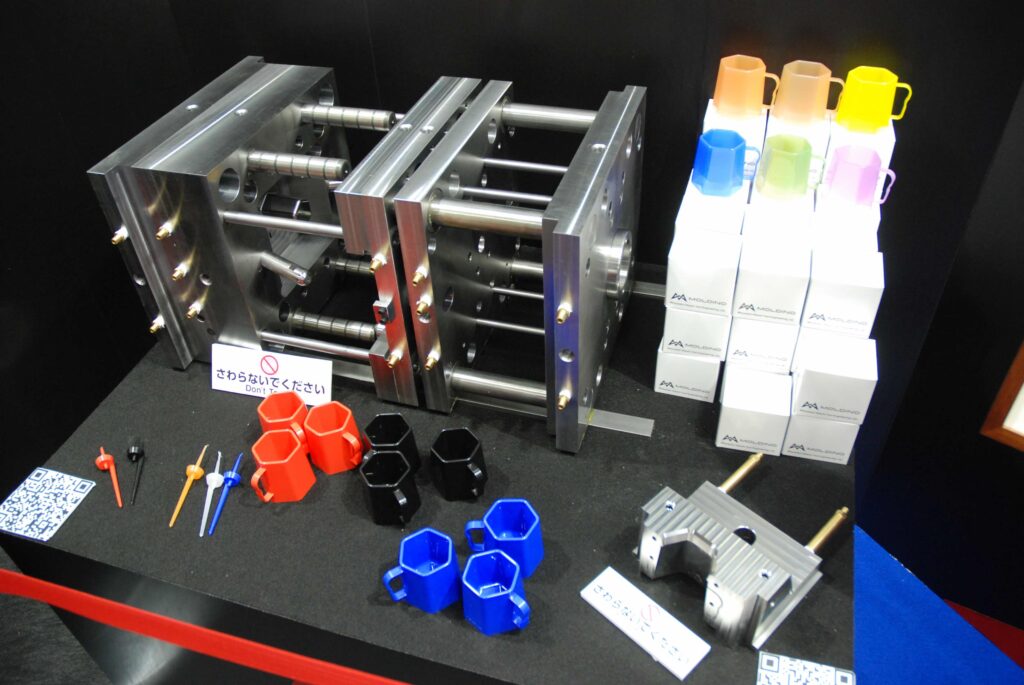
「金型加工向けを中心とした工具を提供するメーカーを目指す上で、まずは金型加工というのがどういうものか改めて知る必要がありました」(木野氏)。一方で、「前回は金型加工の課題を知ろうというのが目的で、新製品や加工法の提案までは行きませんでした。今回は新製品の開発と加工提案につなげることを目指しました」(木野氏)。
ケースの設計から社内で手掛けた
今回のプロジェクトでは、エンドミルを収納するケースを製作すると決め、ケースの設計から社内で行ったという。どんなケースにするか。いろんなアイデアを検討する中には、工具が丸だから、円柱状にしたらどうかという案も。「この案は既存の生産システムでの対応が難しいということで採用には至りませんでしたが、まずはユーザーの使い勝手を考え、さまざまな工夫をこらして設計しました」(テクニカルエンジニア・池部哲夫氏)。
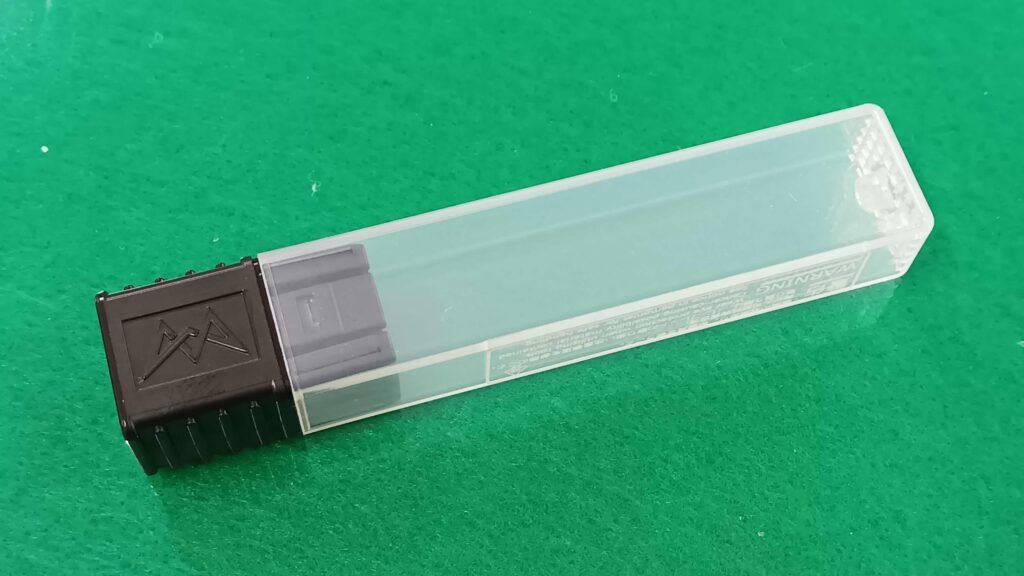
そもそもエンドミルケースは、「本体」と「フタ」で構成されている。「本体」は既存のCBNエンドミルシリーズで採用している黒に、「フタ」も従来通りの透明とした。
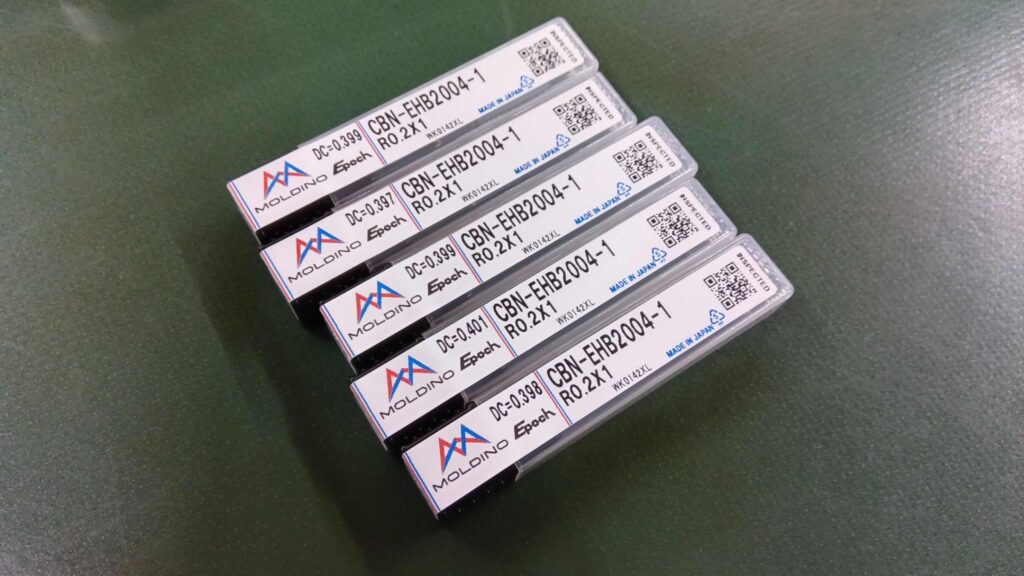
「本体」はグリップ感を持たせるために、側面に凹凸形状を加え、シボ加工を施した。また、「本体」にくぼみ、「フタ」に高さ0.5mmほどの突起を設け、くぼみと突起が噛み合うことで、簡単に外れにくい構造に。同社のロゴマークも配した。
また、「本体」と「フタ」の間には、0.5mmのすき間を設けた。「ユーザーの多くが、スケールを使ってケースに貼ってあるラベルを切って、開封しています。すき間を設けることで、スケールを入りやすくしました」(池部氏)。その他、「本体」は底面を鏡面に仕上げ、ラベルとの密着性を上げることで、ラベルがはがれにくいように工夫した。
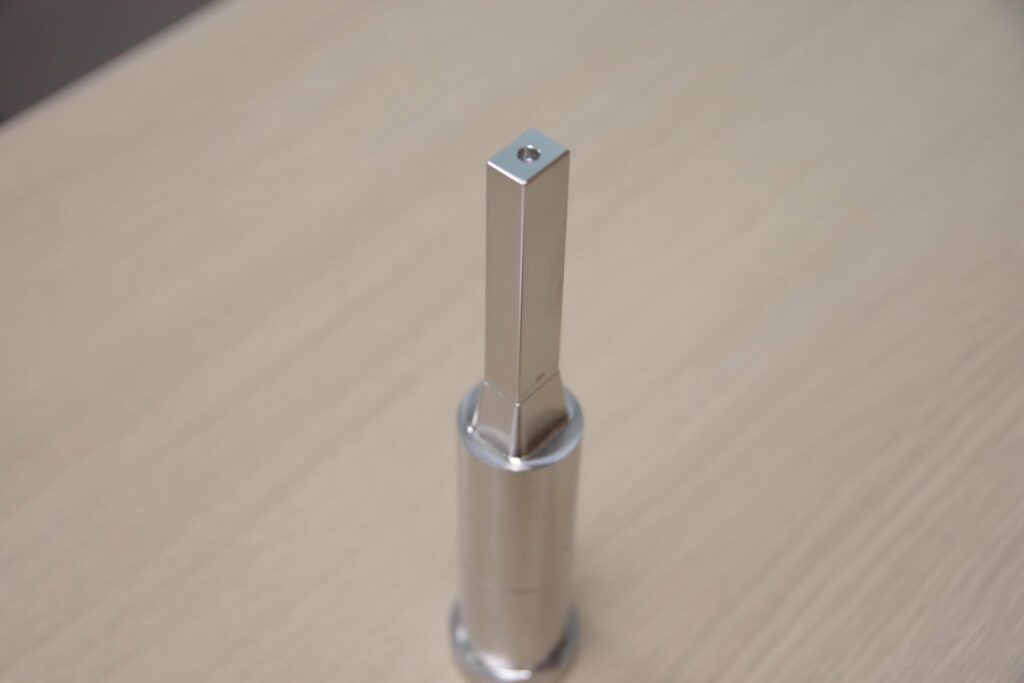
金型は2型、オール切削加工で
金型は、「本体」と「フタ」の2型を製作。さまざまなメーカーのマシニングセンタ11台が設備される同社野洲工場(滋賀県野洲市)で約2年かけて完成させた。「プロジェクトは2020年からスタートしたのですが、途中で新型コロナウイルスの感染拡大の影響による中断もあり、当初の計画よりも長引いてしまいました」(木野氏)。
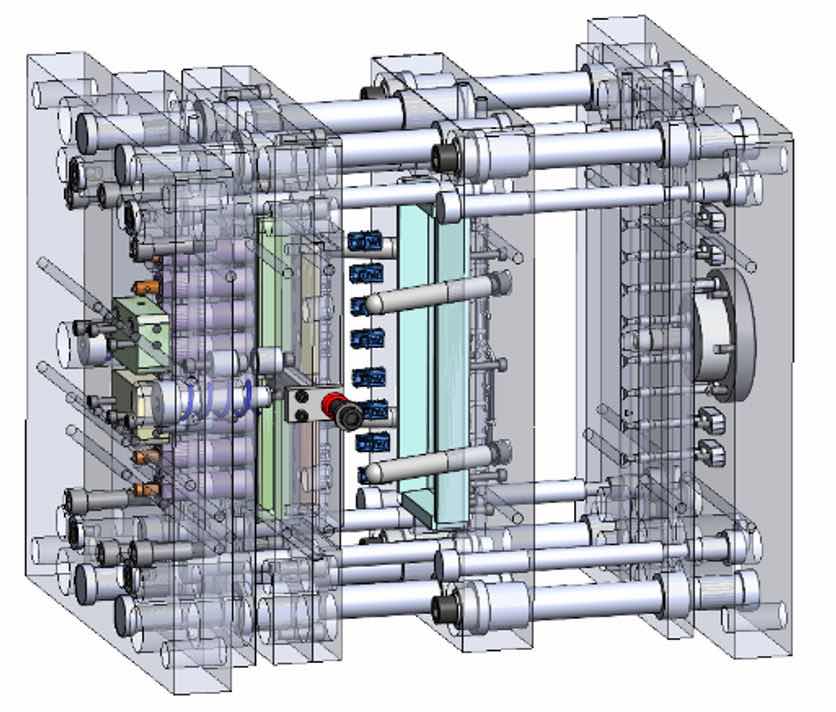
特に苦労したのが、金型設計だという。「アドバイザーにご支援をいただきながら設計したのですが、コロナ禍だったため、ほとんどリモートでの作業となりました。ウエブ会議システムを使い、私がCADを操作し、アドバイザーから口頭で指示を受けながら作り込んでいきました。どこを、どっちに、どのくらい動かすのか、途中で混乱することもあり、お互い相当苦労しました。1つの部品を設計するのに丸一日かかったこともありました」(池部氏)。最終的には2型設計するのに2カ月ほどかかったという。
金型製作で特にこだわったのは、大きく3つ。①オール切削加工(放電レス)②磨きレス③成形バリを出さない加工―。これらを実現するために、さまざまな工具を駆使して、金型の製作にあたった。「今回の金型を加工するのに、だいたい50アイテム、100本以上の当社製工具を使用しました」(池部氏)。
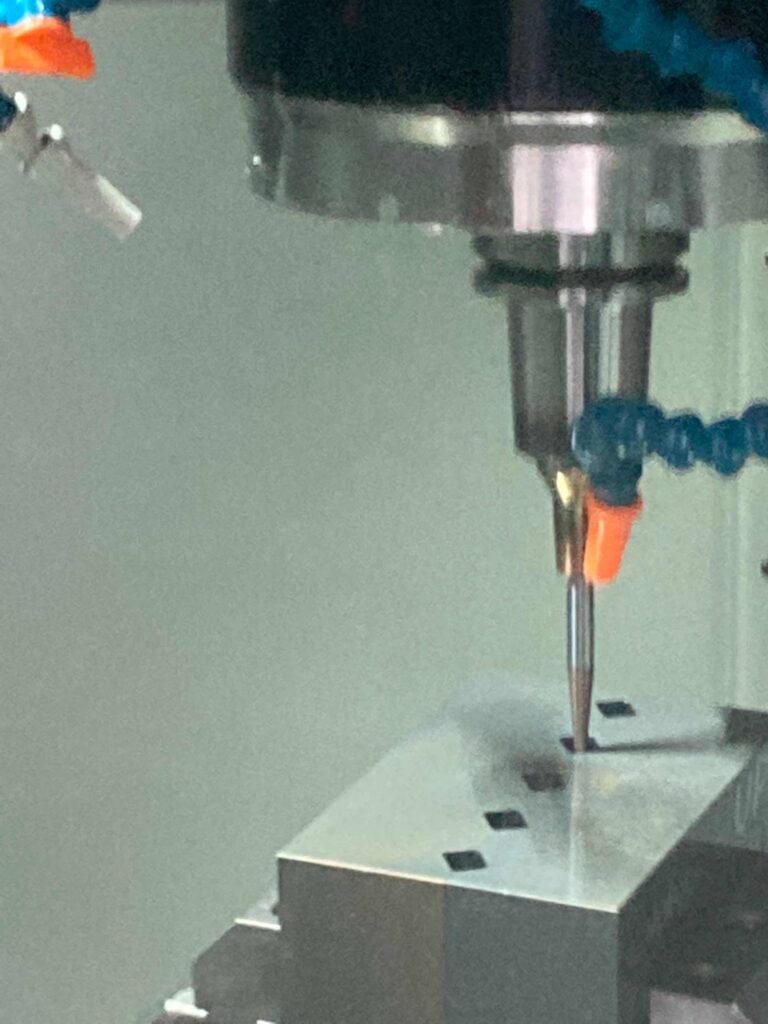
突き加工で磨きレスを実現
金型加工では、同社が持つさまざまな工具、工法を用いた。その中でも特に革新的だったのが、「フタ」の金型での加工だ。この「フタ」の金型は、パーティングラインを目立たせないようにするため、角部を中心に割る構造を採用した。ただ、各スライドで加工にずれが生じると、パーティングラインが目立ってしまうため、いかにずらさないで加工するかが重要になるという。
そこで、同社はスライドを閉じた状態で加工ができる特殊工具を製作。4枚刃ラジアスエンドミル「EPDRF」をベースに、首部の段差をなくした特殊な工具を使い、5軸加工機による突き加工で旋回しながら加工することで実現した。「この工法を用いたことで、スライドを閉じたまま加工できただけでなく、鏡面加工による磨きレスにもつながりました。おそらく、Z方向はXY方向に比べ、剛性が高いため、安定して加工できたのかもしれません」(池部氏)
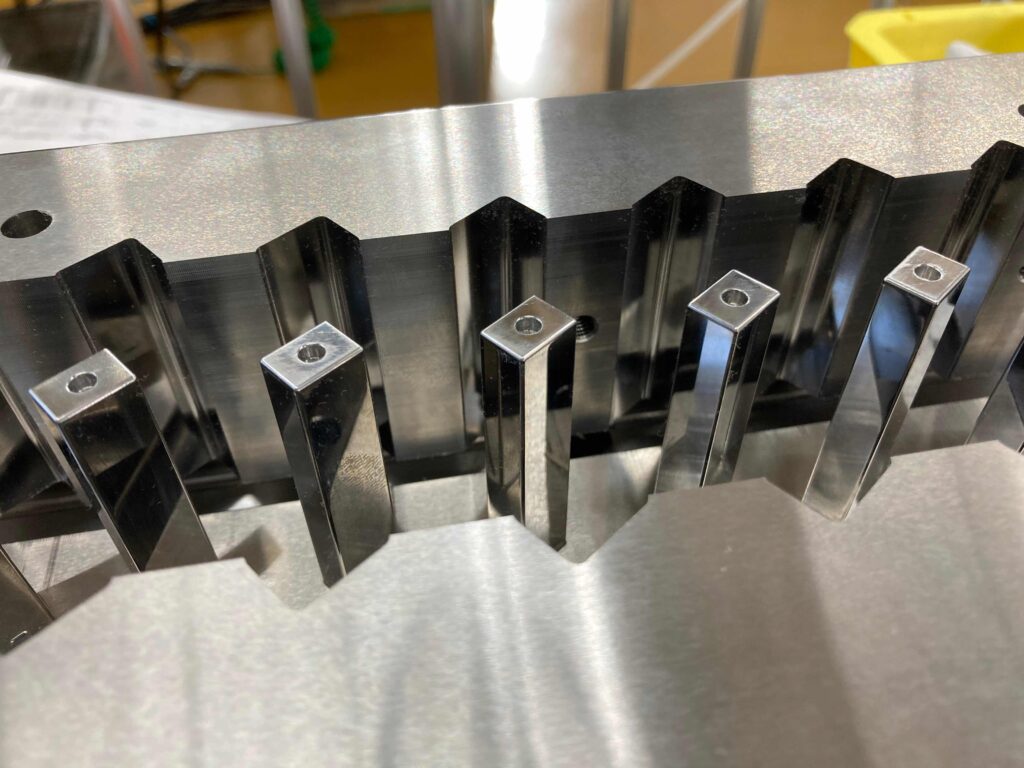
この突き加工は、キャビティだけでなく、コアの加工でも採用した。インサート式工具で加工し、鏡面加工を実現。加工時間は2時間かかったが、仕上げの磨き工程では、砥石やペーパーを使わず、ダイヤモンドペーストを用いて20分ほどで仕上げることができたという。「加工に2時間かかっても、人の手をほとんどかけなくて済むので、メリットは大きいと考えました」(池部氏)。
新製品の開発にもつながった
また、「フタ」の金型加工で使用した特殊工具は、新製品の開発にもつながった。今年2月、深掘り加工用ボールエンドミル「EPDBPE-ATH」に首部の段差をなくした「フリーネックタイプ」を追加した。干渉を気にせず加工できるため、ダイカスト金型などの深掘り加工に適している。また、突出し量を調整できるため、工具集約にもつながるという。
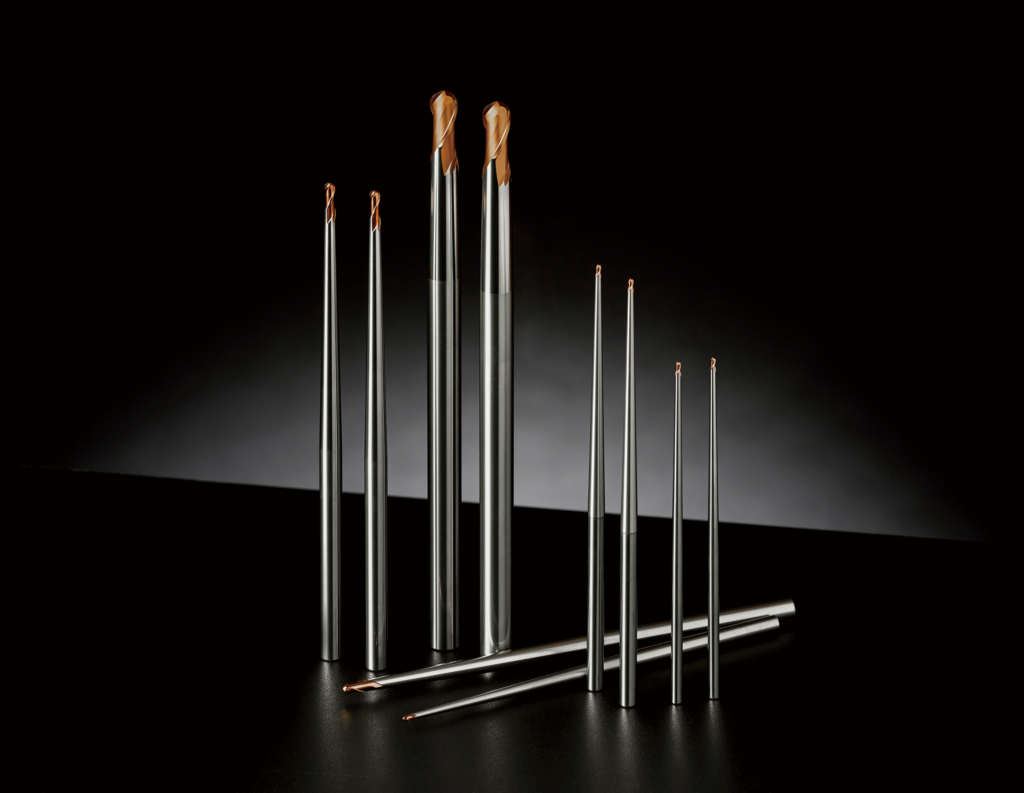
「これから需要拡大が期待される『ギガキャスト』などの深掘り加工に対して、安定した加工を実現することができます。加えて、干渉を気にしなくて良いのが特長。すでにいくつかの企業に試してもらったが、非常に評判が良いです。当社も今回の金型づくりを通じてその良さを実感しています」(木野氏)。
高精度加工の重要性を再認識
一方、こうした一連の取り組みを進める中、多くの学びもあったという。その一つが、高精度加工の重要性。「完成した金型を初めて射出成形機に載せて成形した際、大きなバリが出してしまいました」(池部氏)。原因はある部品が3μm削り足りなかったことにあった。通常の金型メーカーであれば、削り足りなかった3μmを熟練作業者の手で磨いて調整するところだが、同社にはそうした熟練作業者がいない。結局、機械で数μmの再加工を行い、何とかバリを抑えることができたものの、正確に3μmだけ追い加工するのは段取り的にも非常に難しく、「削りすぎたら、またバリが出てしまうし、祈るように加工しました」(池部氏)。
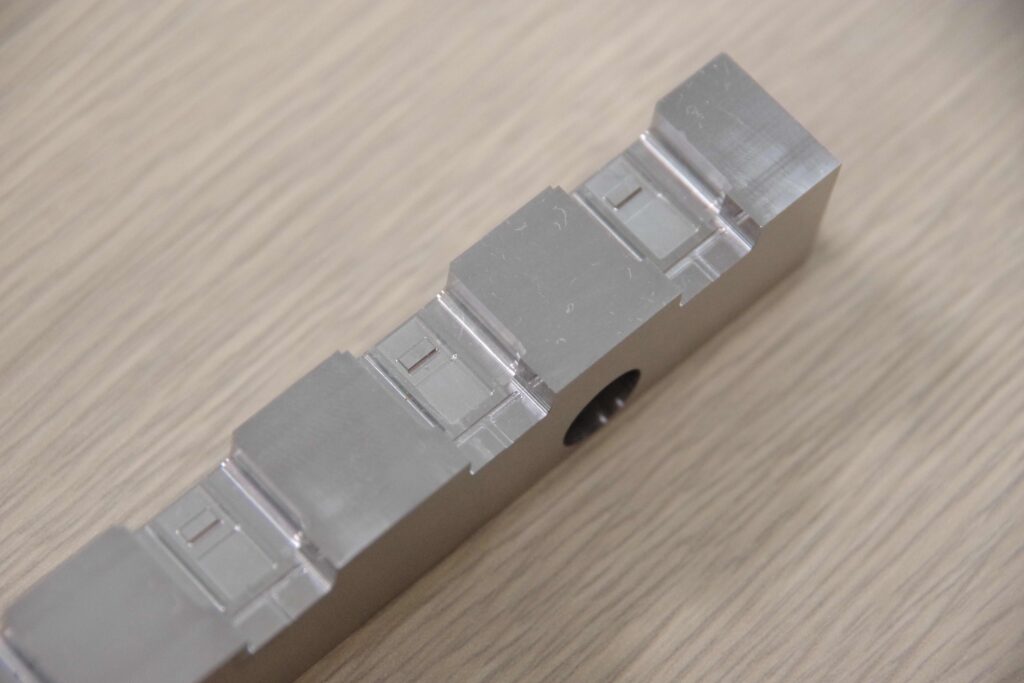
そこで感じたのは、「合わせ」の大変さだという。「合わないと、手で仕上げるか、もう一度機械に載せて加工し直さないといけません。ただ、それだと工数や手間がかかってしまいます。きちんと機械で高精度な加工ができていれば、こうした手間をなくすことができるのだと、身をもって感じました」(池部氏)。
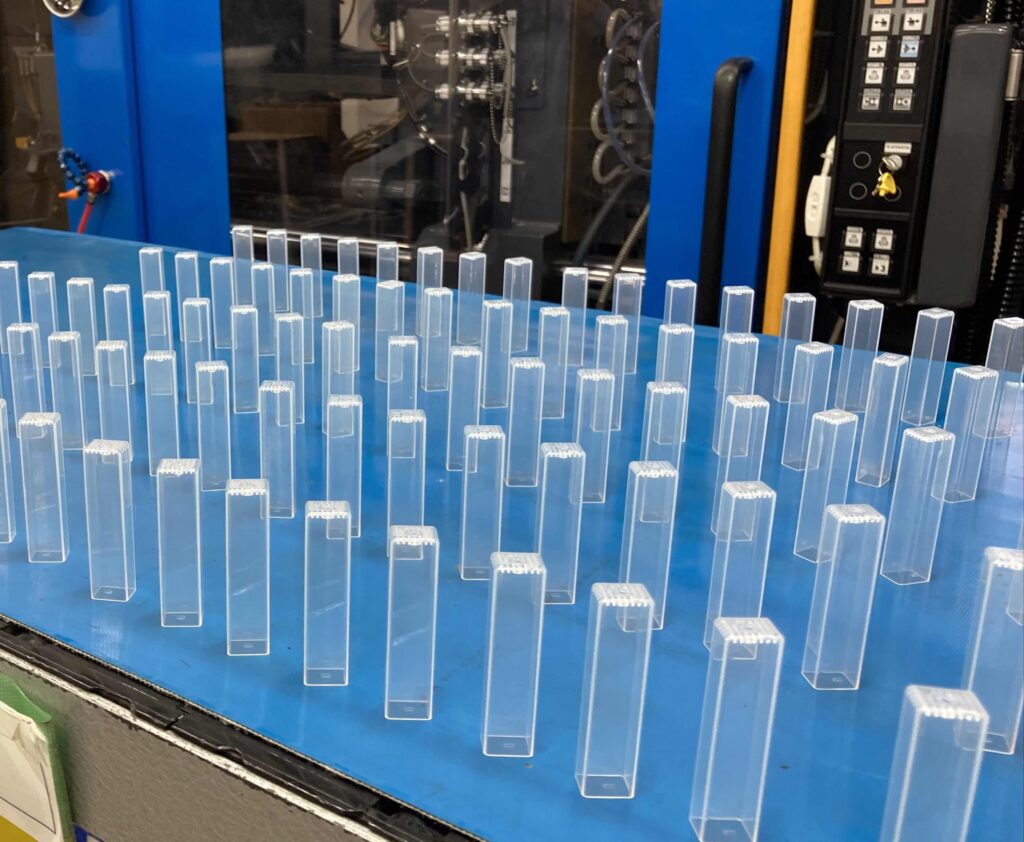
同社では以前から、荒加工から高精度を追求し、磨き・調整まで含めたトータル工程の最適化を狙う「Hi-Pre²(ハイプレツー)」を提唱し、提案を行っている。「我々がやるべきことは、もっと磨きの時間を短縮することではないか。そう考えて、今、磨き工数を減らすことができるアプリケーションの開発に注力しています。磨き工数が多くなると、工数が増えるだけでなく、形状の崩れにもつながります。こうした問題を起こさないような工具開発、工法提案ができればと考えています」(木野氏)。
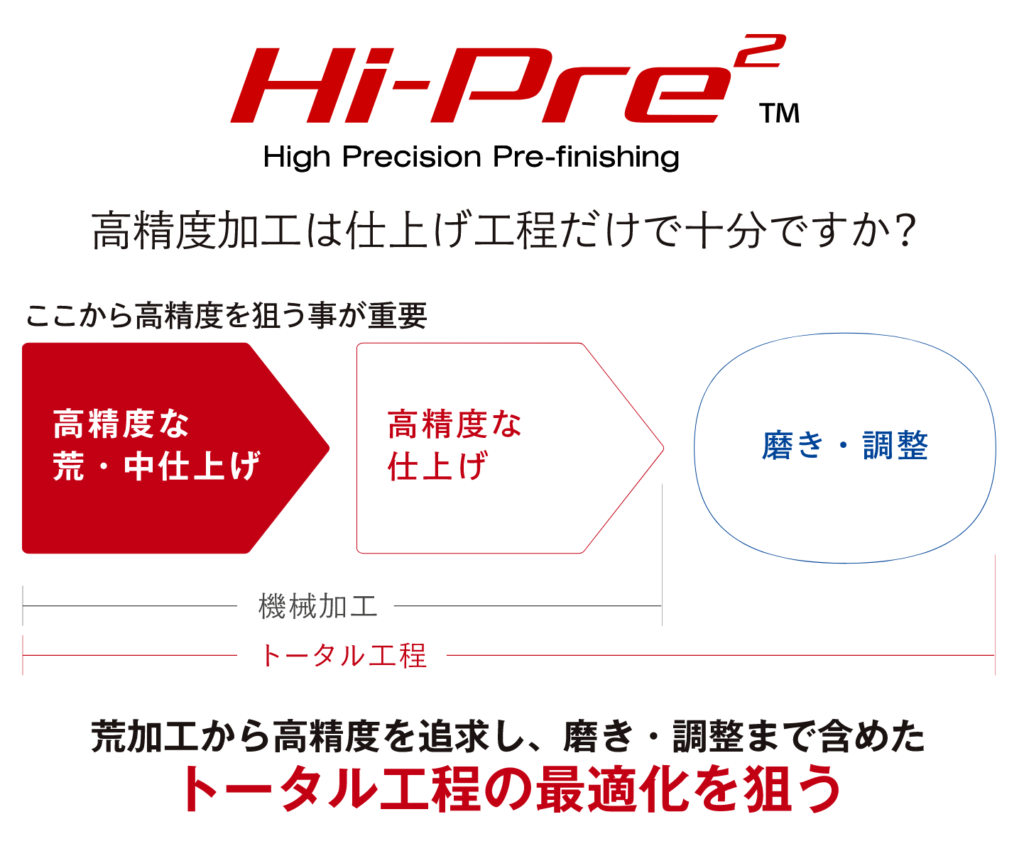
社内教育、工具・工法提案に生かす
今回のプロジェクトで培った経験は、社内教育に生かしているという。営業担当者全員を対象に「金型勉強会」を実施し、今回の金型づくりで得た工具や加工に関する知見、知識を共有。提案力の底上げにつなげている。また、社内だけでなく、今後は社外でも積極的に発信していく考え。「どんどん外に情報を出していき、お客さんとの交流につなげていきたいです」(池部氏)。
また、活用した工具や工法などはユーザーへの提案にも活用していく考え。「同じような課題を抱える金型加工現場はたくさんあると思う。今回の取り組みだけで終わらせず、積極的に展開していきたいと考えています」(木野氏)。
「金型」を意味する「MOLD」と、「革新」を意味する「INNOVATION」を組み合わせて作られた「MOLDINO」。2020年に社名を変更してから今年(2024年)で4年が経つ。金型加工に特化した切削工具メーカーとして、さらなる加工イノベーションを実現するべく、同社の挑戦は続く。
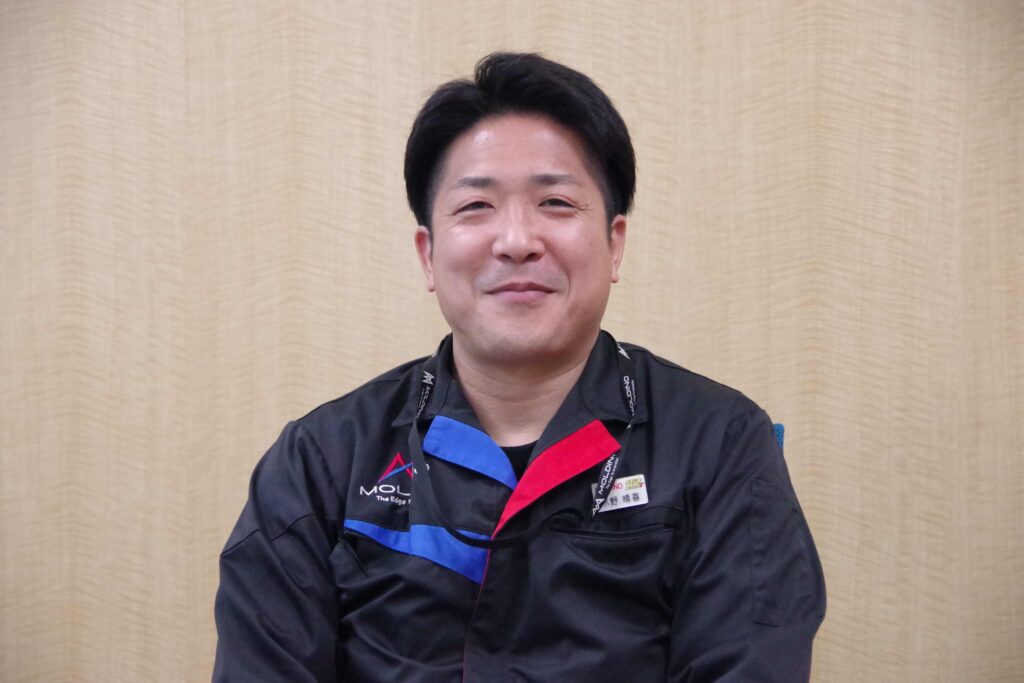
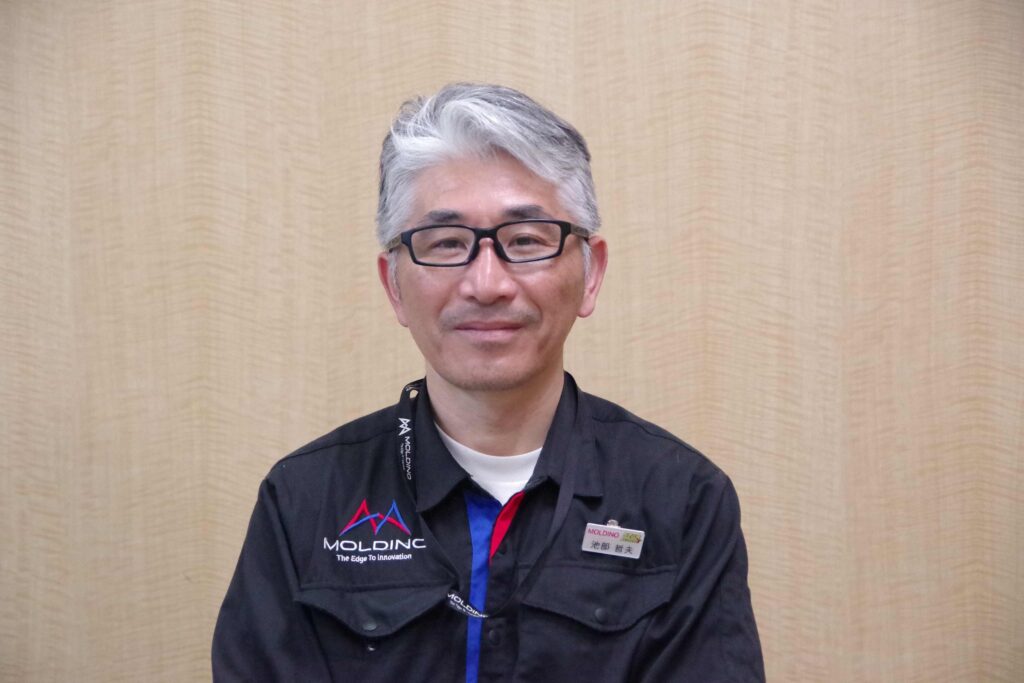
金型新聞WEB限定
関連記事
中古機械を販売する小林機械は今年からリース会社と提携し、中古機械のサブスクリプション(定額課金)サービスの提供を開始した。一般的なリース契約(7年)よりも短い2年で使用可能。短期的な受注や、試験的な導入などのニーズに対応…
輸入強化や印市場開拓 松野金型製作所(佐賀県基山町、0942・81・7000)はこのほど、インドの成形企業と業務提携した。金型や金型技術を提供する一方、インドで成形した部品の輸入や、インドで成形を検討する日系ユーザーの支…
高熱伝導グラファイト複合素材の開発や製造を手掛けるサーモグラフィティクスは、金型向けのサービスを強化している。高熱伝導グラファイト(1700W /m・k)を金型の中に独自の複合化技術で埋め込み熱伝導率を高めることで高速昇…
設計・解析ノウハウ中国で蓄積 ギガキャストで先行する中国でギガ向け金型を製作し、そのノウハウをベースに国内でのギガ関連の需要開拓を狙うのが共立精機だ。構想段階からの設計相談や解析などの技術サポートを提供する一方、国内では…