自動車のプレス金型を手掛ける明星金属工業は、工場のエア効率化や照明のLED化などにより16年間でCO2排出量を18・5%削減した。カーボンニュートラルへの取り組みを推進する上田幸司社長は「CO2削減に取り組むことで無駄な…
【特集】進化する金型のDX
デジタル技術を活用してビジネスモデルや業務プロセスを変革するデジタルトランスフォーメーション(DX)。しかし、人が介在する金型づくりでDXを進めるのは簡単ではない。金型企業はDXをどのように考え、取り組むべきなのか。先進的な取り組みを進める企業やDXを実現する最新技術を紹介し、進化する金型のDXに迫る。
目次
PART1:ツバメックス 全工程がデータで一気通貫
PART2:エムエス製作所 社内制度も工場見学もDX
PART3:アイセル ルーティン化した無駄の洗い出し
PART4:DXのススメ
PART5:記者の目
PART1
ツバメックス インタビュー
金型業界でも「DX」の動きが加速する中、40年ほど前から独自のアプローチで取り組みを進めてきたのが、金属加工の集積地「新潟・燕三条地域」に本社を構えるツバメックスだ。独自開発した3次元設計支援システムを中心に、上流工程の営業から最終工程の仕上げまで一気通貫でデータが繋がる仕組みを構築。金型づくりのリードタイム短縮に取り組むとともに、“金型サプライチェーン”における新たな仕組みづくりにも挑む。
全工程データが一気通貫 新しいサプライチェーンを構築

ツバメックスが「DX」の先駆けとなる取り組みを進めたのは、1982年にCAD/CAMシステム「CATIA」(仏ダッソー・システムズ社)を導入してから。当時はまだITを活用した金型づくりが一般的ではない中、「コストの80%は設計段階で決まると言われている。この設計を効率化するために、いち早く導入を決めた」(開発部の荒井善之氏)。
この「CATIA」をもとに独自開発したのが、現在同社の金型づくりを支えている3次元設計支援システム「TADD(Tsubamex Auto Die Design System)」だ。通常、CADシステムはモデリング機能が主で、NCデータや部品表などの情報はオペレータが引き出さなければならない。
一方、「TADD」はユーザー情報を入力し、金型の3次元モデルを構築すると、三面図や部品表、鋳物データ、加工属性、ビューワデータなどを全て自動で出力することができる。これを実現するために取り組んだのが、「TADD」と金型づくりに必要な情報システムを連携させることだ。
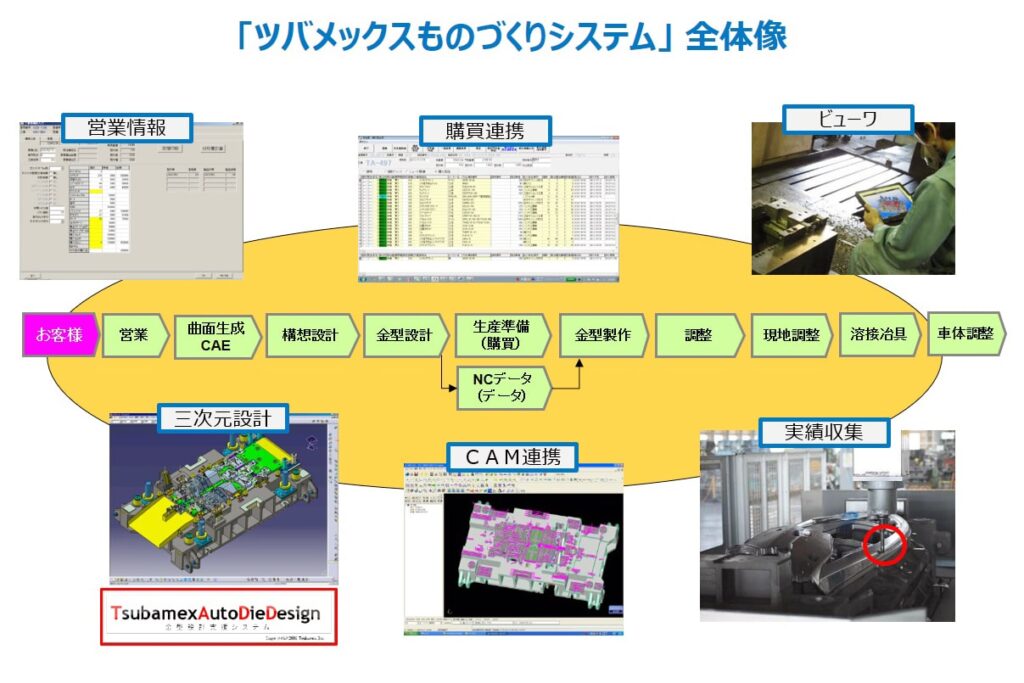
営業情報や原価、ユーザー情報を管理する「金型管理システム」、日程や進捗を支援する「日程管理・スケジューラシステム」、加工設備の実績を自動で収集する「NC稼働システム」、いつでもどこでも情報が閲覧できる「ビューワ・ポータルシステム」などを連携。営業から最終仕上げまで一貫したデータで繋げ、誰もがいつでもどこでも現場で起こっている情報を確認できるようにした。
この仕組みによって、設計業務の作業性が向上。モールド金型では設計リードタイムが従来の3分の1まで短縮した。さらに、後工程に対してミス「ゼロ」のデータ提供も可能にした。現場の作業者が設計担当者に問い合わせる回数もこれまでの4分の1にまで減らすことができたという。
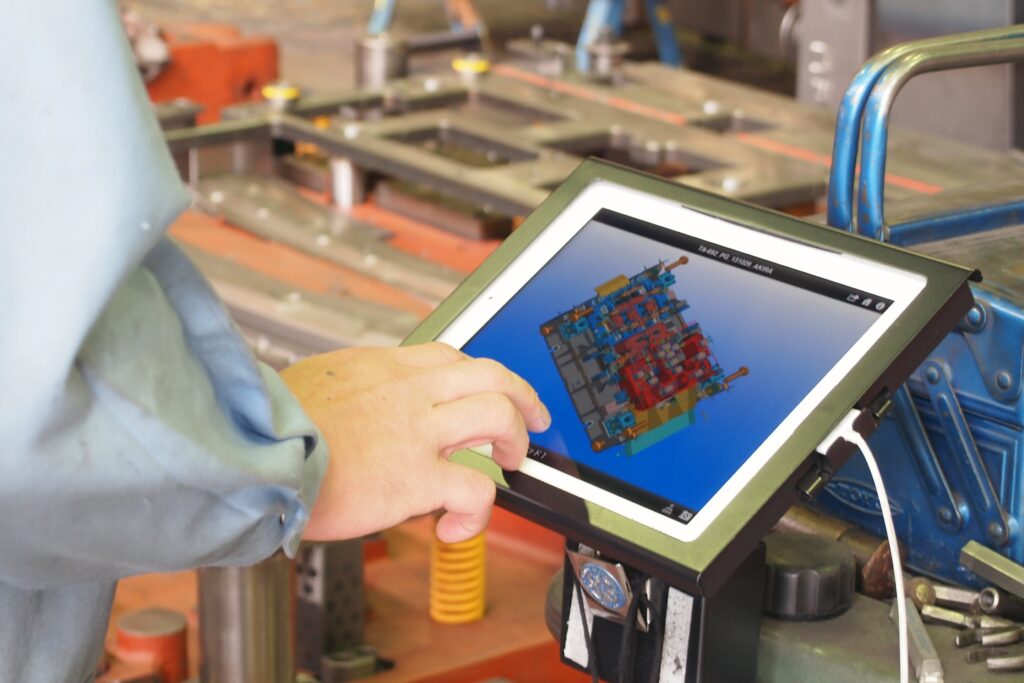
こうしたシステムでよく課題として挙げられるのが「システムをいかに定着させるか」。同社ではシステムを使ってもらえるようにするために、「見たくなるコンテンツづくり」に注力したという。部品表、納期、作業指示、ユーザー仕様など、現場の作業者が必要となる情報を全て集約し、見たくなる、使いたくなるように作り込みを行った。2005年にはIoT機器を導入し、加工設備の実績情報もリアルタイムで確認できるようにした。
加えて、現場の作業者全員にパソコンもしくはiPadを支給し、全員が同じ操作でこれらの情報を閲覧できる環境を整えた。「IT機器に不慣れな作業者でも必要な情報が手に入るとなれば、強制しなくてもしっかりと使ってもらえるようになる」(荒井氏)。
「今後、受注変動の波やQCD(品質・コスト・納期)の要求はさらに厳しさを増すことが予測される。こうした状況を乗り切るには金型企業同士が連携していくことが大事。『DX』はその大きな武器になる」(多田羅晋由社長)。同社は今後、これまでに組み上げてきた「TADD」を始めとした仕組みを生かし、企業間連携に取り組もうとしている。
3次元設計データを共有し、設計変更や作業指示などにかかる時間ロスを無くす他、受発注や工程情報、IoTで取得した実績情報などをクラウド上で共有する仕組みを構築し、複数の金型企業との共同受注体を目指す。すでに2社と連携しており、今後さらに増やしていく考えだ。「当社と一緒に取り組める仲間を増やし、『DX』によって金型業界における新しいサプライチェーンを構築していきたい」(多田羅社長)。
- 本社 : 新潟県新潟市西蒲区高野宮3283-1
- 電話 : 025-375-4945
- 代表者 : 多田羅晋由社長
- 創業 : 1892年
- 従業員 : 187人
- 事業内容 : 自動車、建築資材、家電製品などのプレス金型、モールド金型の製造及び金属部品のプレス加工、プラスチック成型品の製造
PAER2
社内制度も工場見学もDX
製造現場だけがDXの対象ではない。社内業務や営業、社員間コミュニケーション、工場見学などもデジタル技術の活用が広がっている。ルーチン作業や不効率な仕事の仕組みを見直し、新しい方法で格段に生産性を高めている。社内DXに取り組む金型メーカー2社の取り組みを紹介する。
エムエス製作所 DXで情報共有を促進
VR工場見学も好評
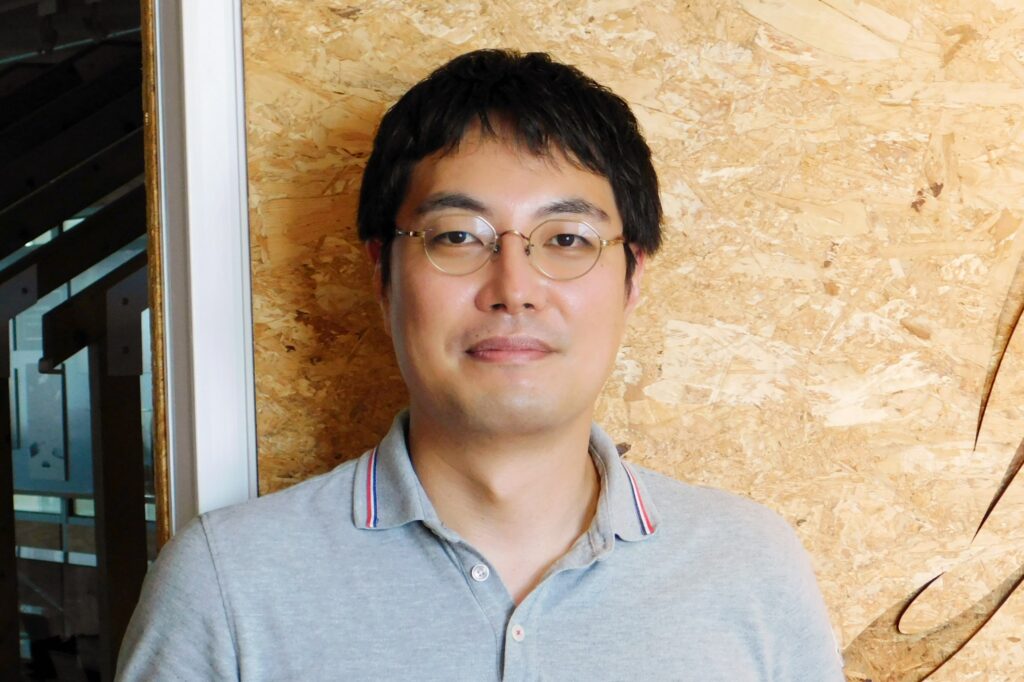
「当社のDXはコミュニケーション改革。金型メーカーの課題は人とのコミュニケーションから生まれるヒューマンエラーや不効率な業務体制にあり、それをデジタル技術の活用で課題解決した」とはゴム金型を手掛けるエムエス製作所(愛知県清須市)の迫田邦裕社長。
同社が導入したのはビジネス型LINEである「LINE WORKS」。全社員がスマートフォンを持ち、チャットや掲示板、カレンダーといった機能を幅広く活用し、トップの情報発信から製造現場の図面やデータなどもデジタルで共有。「1年半の取り組みで間接的なロスが軽減し、課題だったヒューマンエラーや現場のペーパーレス化になった」。また、海外のグループ企業とも情報のやり取りがスムーズになり、「情報の距離感は確実に縮まった」と効果を実感している。
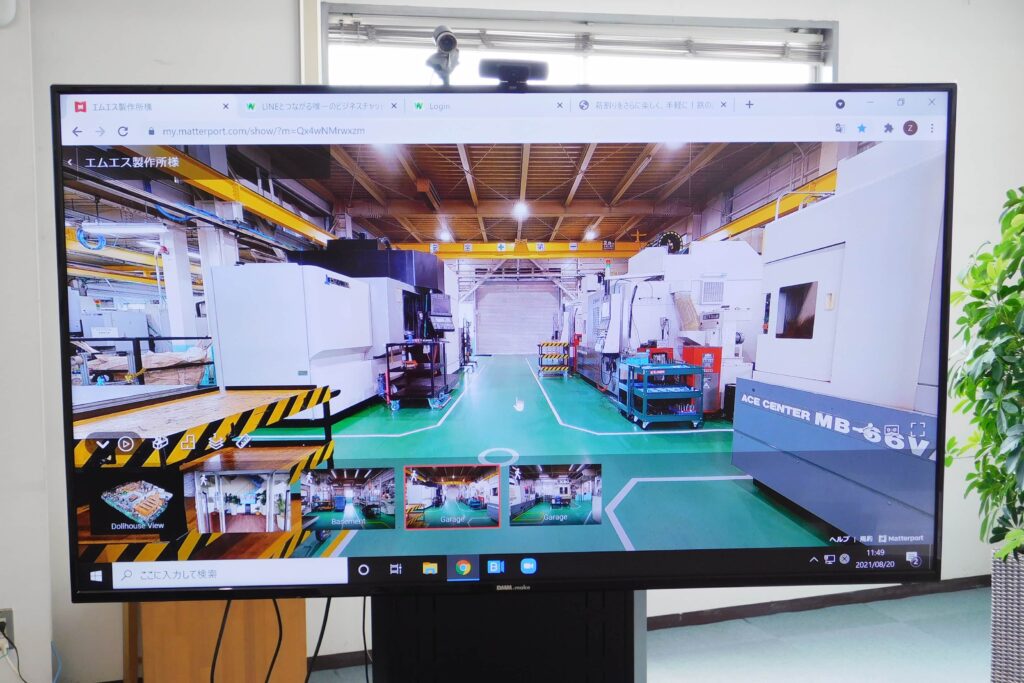
さらに、コロナ禍で工場見学が難しくなったことを受け、顧客向けの情報発信として「VR工場見学」を開始。360度カメラで3次元の仮想空間を作成。立体的な工場全体の俯瞰図(ドールハウス機能)から各フロアにある設備の様子などをリアルに再現し、画面上で回転、拡大、縮小も自由自在に閲覧でき、自身が歩いているような臨場感を体感できる。「当社は5カ国で展開し、海外顧客から日本のマザー工場が見たいというニーズも多く、新たなソリューションを通じて当社を知ってもらう機会を設けることは大きなメリット。新規開拓など営業ツールにも活用できる」と話す。同社はVR工場を新たなソリューション提案と捉え、製造業向けに販売も始めた(基本撮影料は10万円から)。
迫田社長は「自社の強みを見直し、開発力や提案力の強化が必須」と、数年前よりデザイン経営を掲げ、金型メーカーが持つ独自の技術力に、デザイン性など付加した自社製品の開発に取り組む。直近はクラウドファンディングに挑戦。薪割りに使うキャンプ専用クサビ「先鋒」がマクアケで目標額以上の実績を残した。「これは営業のDX。デジタルはあくまでツールで、常に人が主役」とし、デジタルの活用で効率化や新しいことに取り組み、いかに社員のモチベーションを上げるかが金型メーカーのDXといえる。
- 本社 : 愛知県清須市春日立作54‐2
- 電話 : 052・409・5333
- 代表者 : 迫田邦裕社長
- 従業員 : 48人
- 事業内容 : ゴム成形金型、ウェザーストリップ成形金型設計製作など。
PART3
アイセル ルーティン化した無駄の洗い出し
社内制度の見直しも
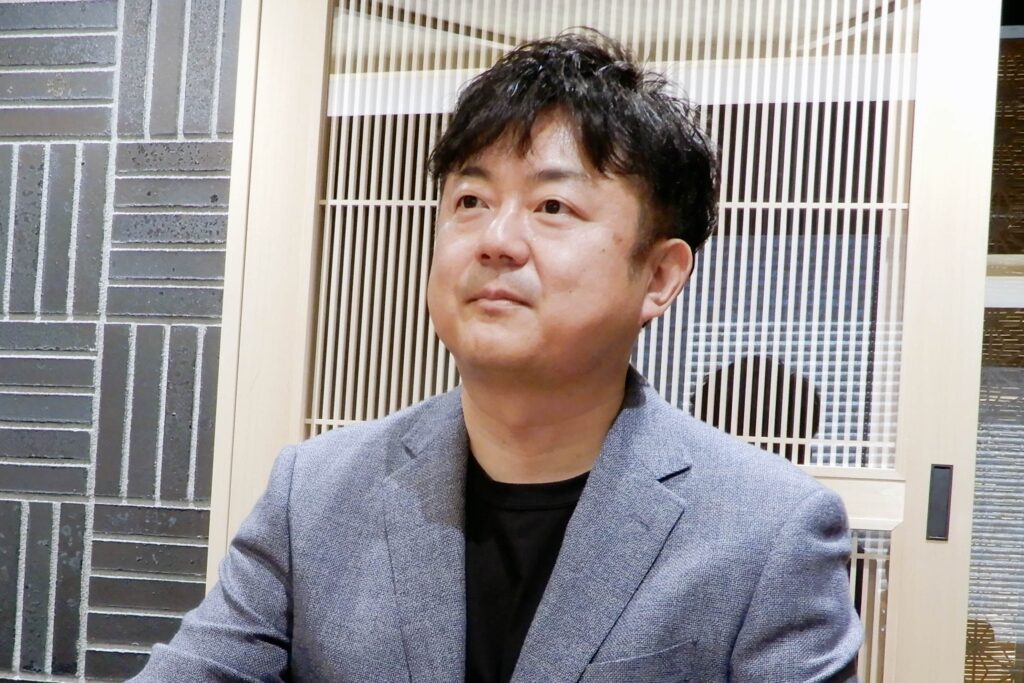
「社内でルーチン化している業務を洗い出し、当たり前だと思っている仕事を解体した」と話すのは、FA用部品や金型のガイドなどの開発・販売を手がけるアイセルの望月貴司社長。同社は、勤怠管理や経理システムなど、社内制度のDXを進めている。
「当たり前」と思われている仕事を解体するため、営業・経理・総務・広報などそれぞれの部署から、仕事に対して先入観の少ない若手を選抜。20〜30代を中心としたグループを作り、課題の洗い出しをさせた。その中で見つかった課題が、勤怠管理、給料計算、精算の3つ。そこで若手グループ内で自動化の方法を考えてもらい、その結果専用システムの導入が決定した。
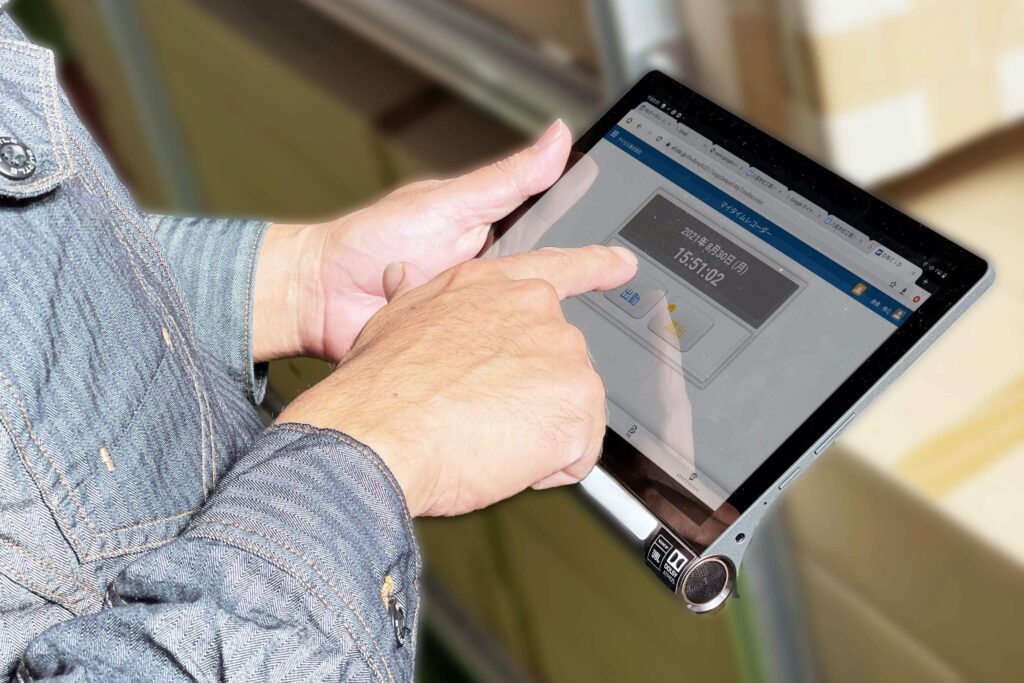
まずは、経理と勤怠管理が同一のシステムを導入。また、従業員全員にタブレットかPCとアカウントを支給し、勤怠管理や、従来は紙で行っていた打刻修正依頼などを全て電子で行える体制を整えた。電子化された勤怠情報や打刻修正の情報からシステムが給与を自動計算するため、これまで経理が一件ずつ行っていた給与計算や修正後の再計算が不要になったほか、従業員も手書きの申請用紙を持って上司に申請する手間が省け、社内全体の効率も向上した。交通費や交際費などの諸経費の精算も同様で、スマホやタブレット、PCから申請が可能。システムが自動で計算するため人の手がかからず、業務の脱属人化も促進できた。
導入に当たり、例えば同社は1分単位で打刻に対応していたが、システムでは15分刻みの打刻しか対応できないなど、システムの機能と社内の制度が合わない場面も多かった。しかし「社内制度にシステムを合わせるのではなく、システムが一般的なものだと考え、会社がシステムに合わせる必要がある」(望月社長)として、社内制度をシステムに合わせることを選択。社内制度そのものの見直しも図った。いずれは給与明細なども全て電子化し、印刷費や郵送費の削減を目指すという。
今後の動きについては、「修理・アフターの領域でも、システム導入を考えている。従業員も顧客も、みんなが楽をするためにも、ルーチンの自動化が必要」(望月社長)。
PART4
DXのススメ
デジタル技術の進化はすさまじい。次世代通信規格「5G」で通信環境が変化したり、IoT機器やAI(人工知能)の実装で見える化が進展したり。ただ、これらを全て追いかけるのは難しい。DXで重要なのは、こうしたデジタルツールを金型加工にいかに生かすかだ。そこで本特集では、金型加工に関連が深そうな「稼働状況の見える化」、「リモートによる診断や加工試験」、「シミュレーション技術」、「カンコツをデジタル化する技術」の4つのデジタルツールの活用方法をまとめた。
稼働状況の見える化
データ収集から分析
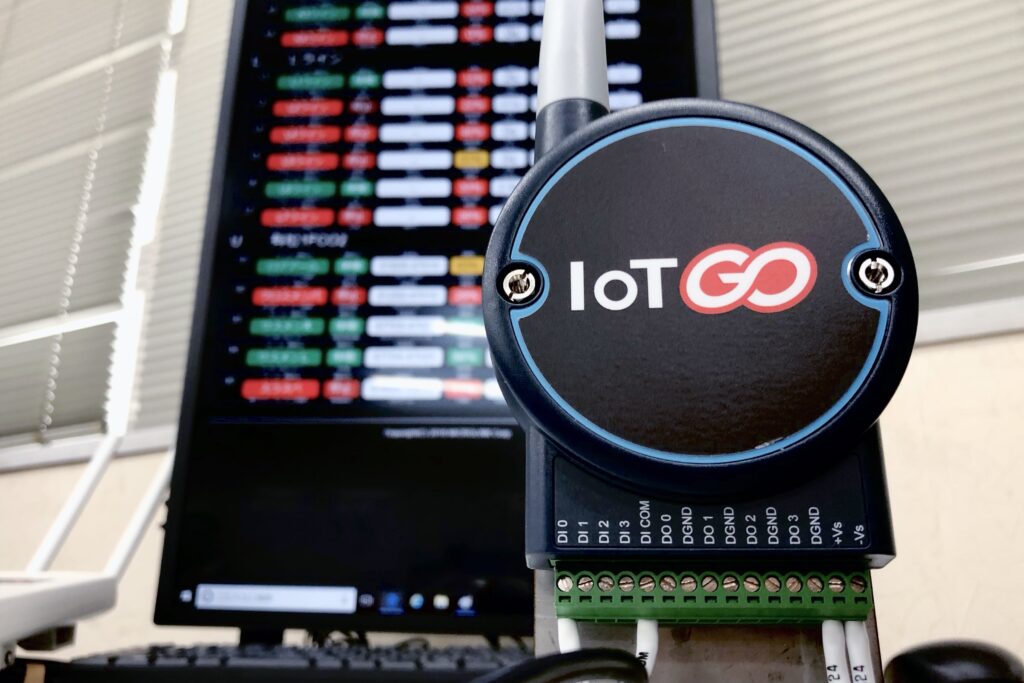
IoTなど先進技術を用いて工作機械といった設備の稼働率を見える化するソリューションは多くの製造業で導入され、機械のダウンタイム改善、稼働率の向上に寄与している。金型メーカー含め製造業では生産量が増加しても少子高齢化による人手不足で、従来のように人員を増やし生産量を高めるのは難しい状況で、いかに同じ人数、現設備の生産性を高められるかが競争力強化に直結する。そのため「定期巡回による設備監視」や「日報からの稼働率集計」など、従来方法による稼働率の見える化ではなく、IoTなどデジタル技術を使いリアルタイムで正確な情報を取得することで、機械停止や異常の原因を明確にし、最適な改善方法を見つけること
がDXの第1歩と言える。
IoTによる機械設備の稼働状況の見える化は様々なメーカーで取り組まれているが、より簡単に構築できることも重要な要素だ。工作機械メーカーではIoT機器を用いてネットワーク化し、機械の稼働状況をモニタリングするソリューションを数多く提案している。
また、CAD/CAMや生産管理システムといったソフトウェア関連のメーカーも工場設備や作業現場の見える化を促進するため、IoT機器との連携やプラットフォームの構築を図っており、新型から旧型の機械設備まで幅広く一元管理し、作業計画と実際の稼働実績を照らし合わせ、比較・分析できる仕組みを構築。
これまで工場内のトラブルはベテラン技術者によるノウハウで早期解決してきた側面があり、今後、技術者の高齢化が進む中で、生産性向上や品質向上を図るには「情報の見える化」でトラブルの事前予知や原因究明につながる仕組みが不可欠。属人的なノウハウをいかに標準化する環境を整えることが未来の競争力につながる。
カンコツをデジタル化
伝承や加工をサポート
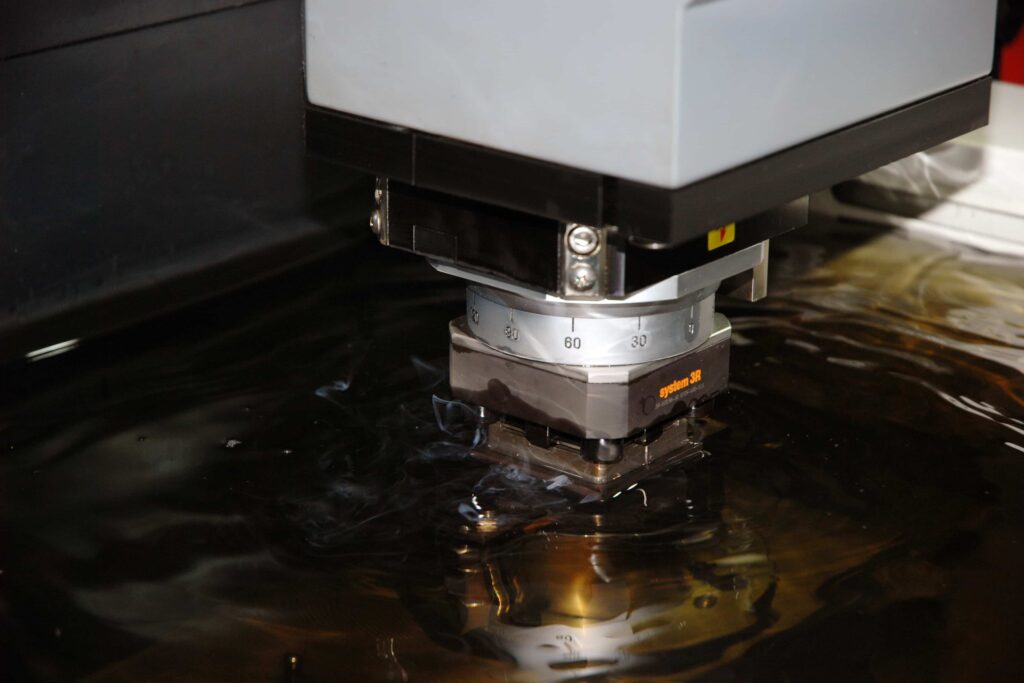
デジタル技術やAI(人工知能)を活用し、技能伝承や機械加工の条件最適化など、カンやコツをデジタル化する動きが広がり始めている。
これまで磨きなど人の動作に関する領域は職人技とされ、伝承や教育が難しいとされてきた。しかし最近では、金型づくりのこの領域でもデジタルの活用が進み始めている。その技術の一つが、人や物体の動きをデジタル的に記録するモーションキャプチャだ。
代表的なのは、磨き作業の見える化。ワークを磨く際に動く、肩や腕、腰などにセンサを取り付け、職人の動きを分析。彼らの動作を細かく分析するとともに、新人技術者との差異を見つけ、技能者育成につなげる企業も出始めている。
切削加工や放電加工の最適な条件設定も技能者の領域。ここではAIを活用するなどして、技能者をサポートする技術も登場している。例えば、放電加工機。形彫り放電では、電極が消耗するため、音や状況を見ながら常に最適な条件設定が必要になる。最近では、AIを活用して、常に最適な条件で放電す
る機能が発表されている。
切削加工でも、パスを最適化する技術が進化している。近年は工作機械の性能が向上しているため、「ある程度のパスであれば形状は出せる」(あるベテラン技術者)が、最も早く効率的なパスとは限らない。
そこで、作成したパスを再計算し、最適な条件を推奨するツールが登場している。技能者に気づきを与えたり、新人をサポートしたりする機能として期待されている。
シミュレーション技術
デジタル空間に現象を再現
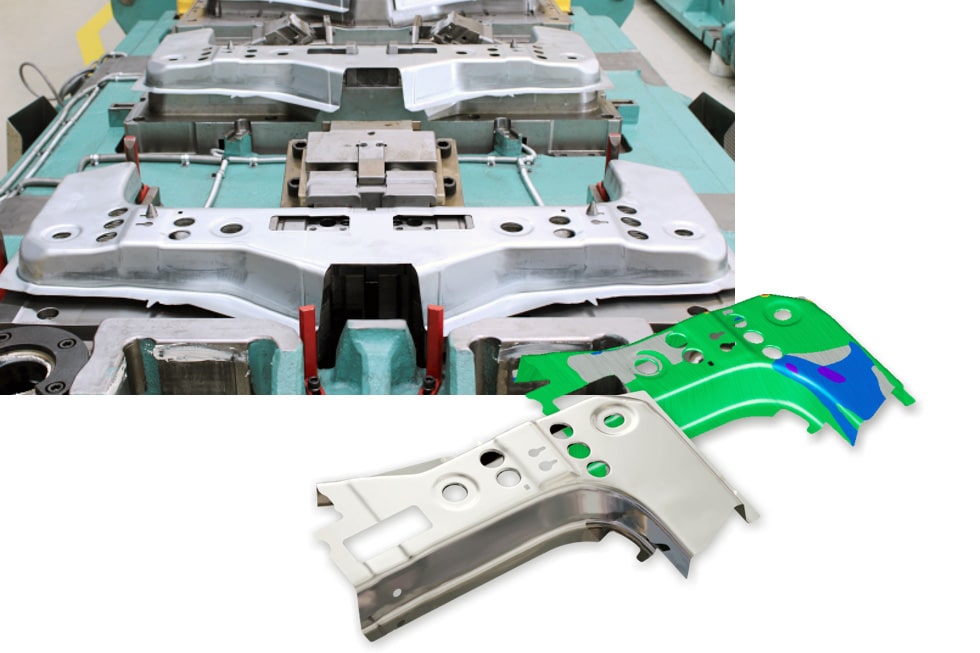
プレス成形品の塑性変形や樹脂の流動性、金型動作などをコンピュータ上で予測するシミュレーション技術。金型づくりの生産性を向上させるツールとして以前から用いられてきた。デジタル空間で実際の現象を再現できるこの技術は、DXにも無くてはならない技術の一つと言える。
近年では、ソフトウェアの情報処理能力の向上や実際のデータを取得する計測技術の進化などによって、シミュレーション精度が向上。より現実に近い結果が得られるようになっている。
シミュレーションソフトでは、材料や条件のバラつきなど量産現場でのパラメータの変動を考慮した手法を導入し、シミュレーション精度を大幅に向上させることができるシステムが登場している。トライ工数の削減、不良率の低減などの効果が期待でき、ある海外メーカーでは、おおよそ2億円のコスト削減効果があったという事例もある。
金型や設備、材料だけでなく、作業者も含めた工場全体をシミュレートして、生産性を向上できるソフトウェアの用途開発も進んでいる。現実空間をデジタル空間に再現する「デジタルツイン」と呼ばれる技術で、工場レイアウトや生産工程のさらなる最適化などに活用することができる。
一方、データを取得する技術では、IoT機器の他、3DスキャナやX線CTなど様々な計測技術の開発が進んでおり、これまで取得できなかったデータも収集できるようになっている。今後、こうしたハードウェアとソフトウェアの進化によって、シミュレーション技術のさらなる革新に期待したい。
加工診断・試験をリモートで
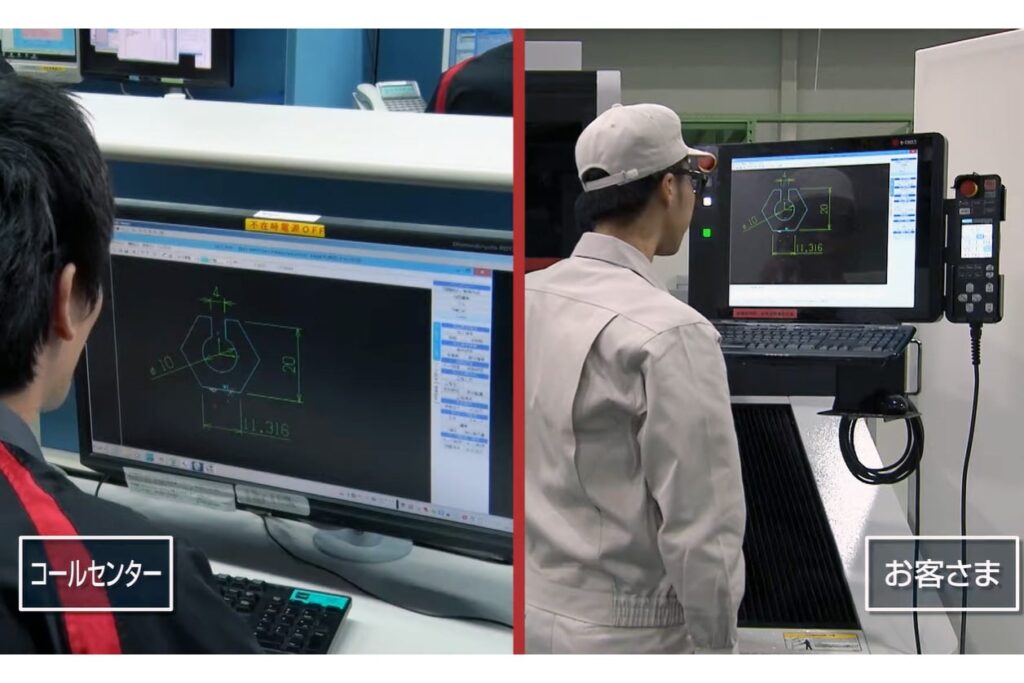
金型のDXは工作機械の稼働監視やシミュレーションなどにとどまらない。生産性を高める最適な加工方法を相談したり、難しいワークの加工試験をしてもらったり。リモートでできるサービスを工作機械や切削工具メーカーが展開している。
経験が浅く、加工の知識やノウハウに乏しい。どんな加工条件、機械に指示すれば失敗せずに加工できるのだろうか—。そんな金型技術者をサポートするのが、三菱電機が展開する「iQ care Remote4U」のリモート診断サービスだ。
技術者はコールセンターに問い合わせ、加工技術オペレータにワークの形状やワイヤの仕様を説明する。さらにワイヤ放電加工機の「リモートサービス」モードに切り替え、両者でCAD図面を共有。オペレータは遠隔でそれを操作、確認し最適な加工条件を導き、アドバイスをする。
一方、遠く離れた場所から切削加工試験ができるのは三菱マテリアル。金型メーカーとテクニカルセンター(埼玉県、岐阜県の2拠点)をテレビ会議システムでつなぎ、課題のワークを最適な加工条件で加工。その様子をカメラで撮影し共有する。
これまで切削試験はテクニカルセンターで行ってきたが、それに比べてリモートは複数の技術者が参加で、訪問する時間やコストを削減できる。またコロナ禍における両者の技術交流の方法として貢献しているという。
PART5
この技術に注目!
オークマ AI活用し予知保全
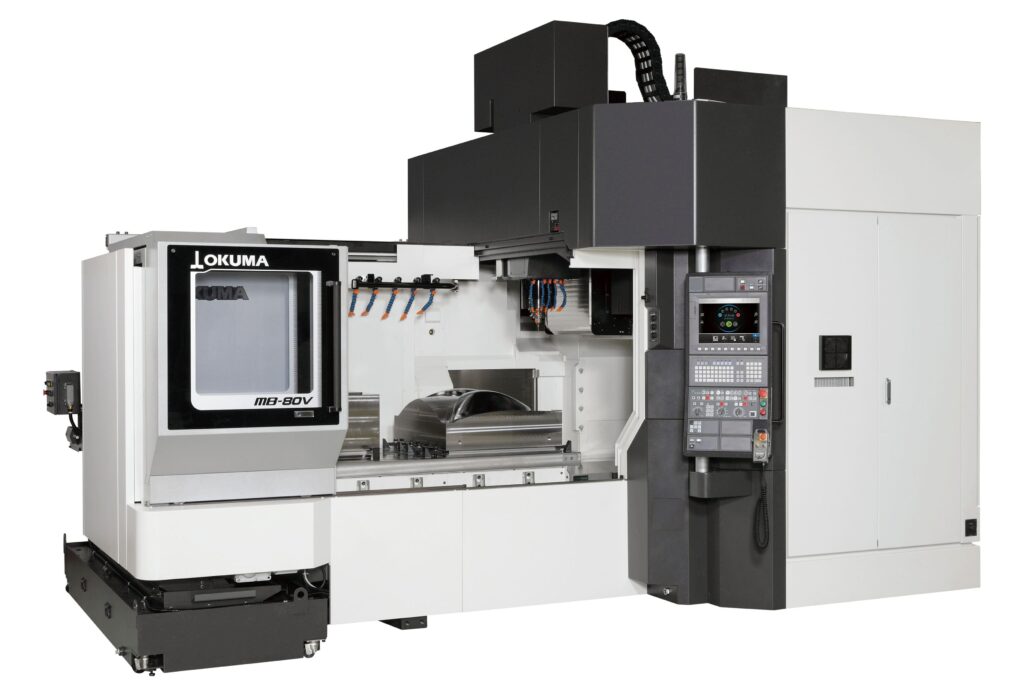
立形マシニングセンタ「MB-80V」
大型化する自動車金型などの大物部品加工に最適な高精度立形マシニングセンタ。荒加工時間を短縮し、高面品位仕上げ加工を1台で完結する。AI技術による予知保全技術でマシンダウンを未然に防止する。
オーエスジー 機械止めずにプリセット
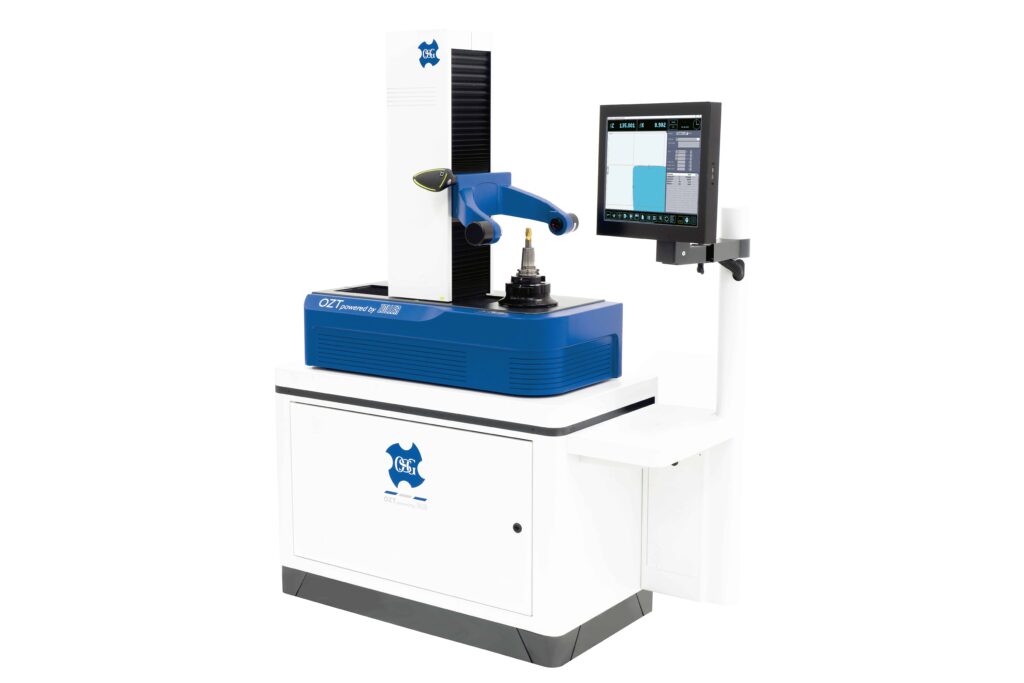
ツールプリセッタ「OZT」(独ZOLLER社製)
機械を止めずツールをプリセットできる。カメラタイプで焦点が合わせやすく、測定値のバラツキも少ない。自動刃先認識システムにより位置合わせ作業も正確にできる。加工前のプリセットや測定により、不良削減、衝突防止、生産性向上に貢献する。
オートフォームジャパン 開発期間短縮を支援
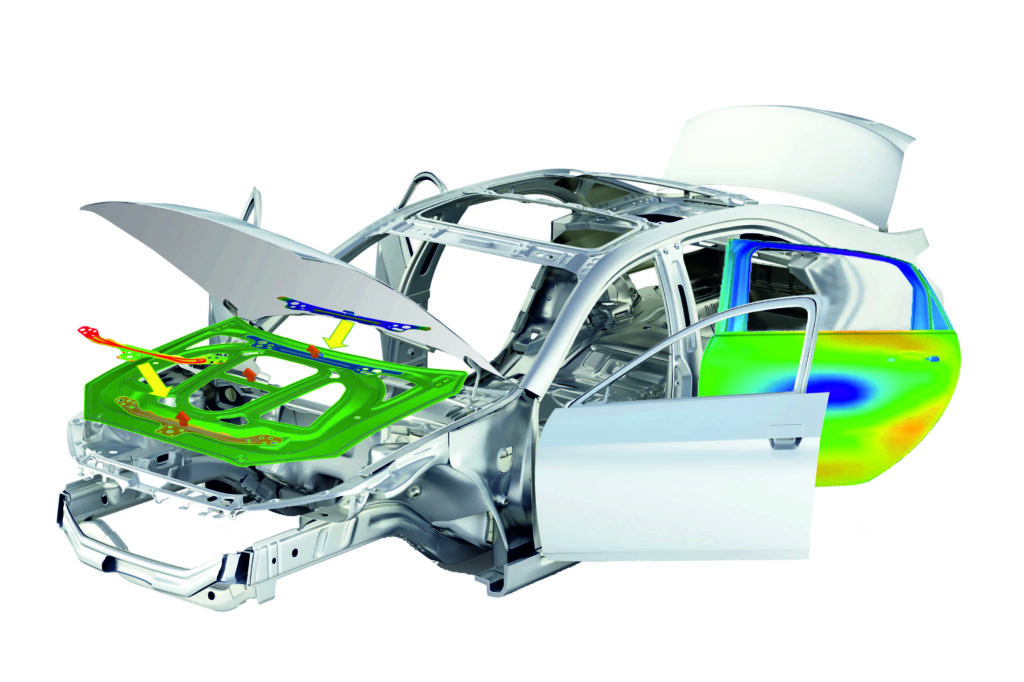
「AutoFormホワイトボディ(BiW)アセンブリソリューション」
プレス部品の早期フィージビリティからプロセス・エンジニアリング、ホワイトボディ生産まで、工程チェーン全体をサポートするソリューションシステム。開発初期から不具合の特定や解消策の検討により数か月単位の開発期間短縮を支援する。
サカモト・ダイテム フル3D対応のモールドベース
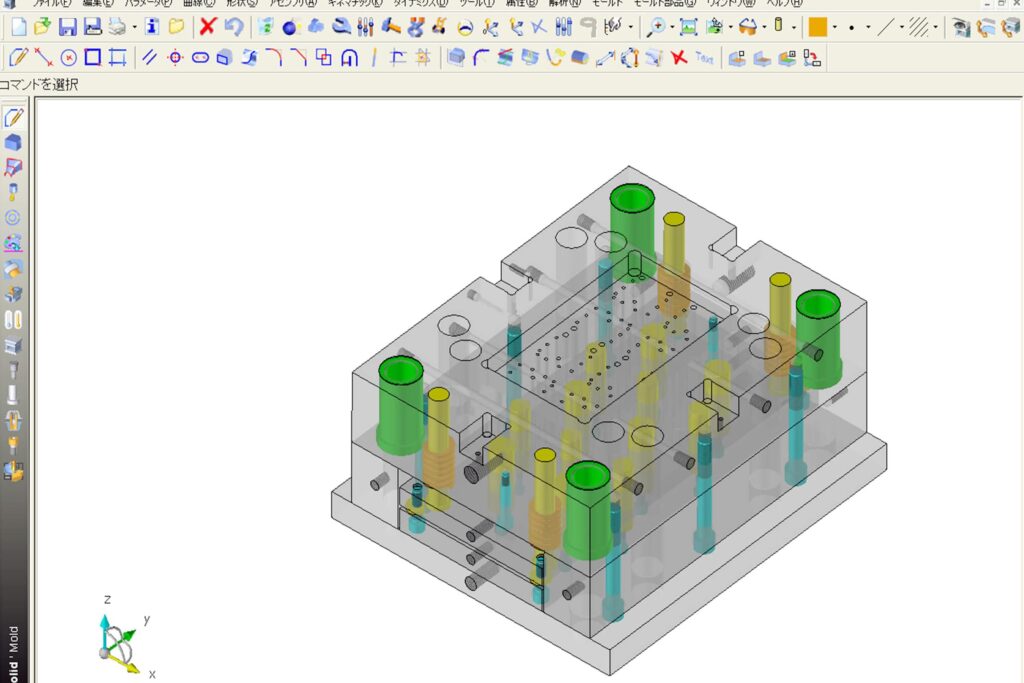
オンライン対応
パラソリッドデータから加工属性を自動で付与できるシステムを開発し、全てのCADでモールドベースの全加工が3次元データのみ(2次元は不要)で対応できる。また、オンライン営業により、取り組みが理解しやすいと好評を得ている。
C&Gシステムズ CAD/CAM連携の工程管理
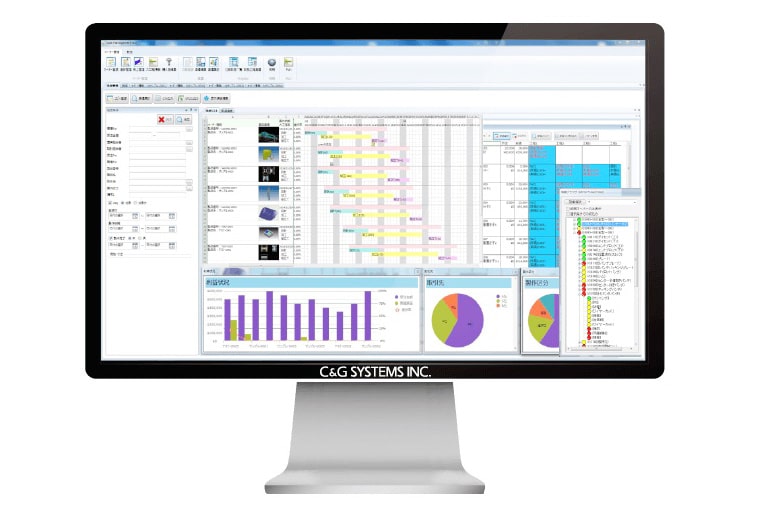
AIQ(アイク)
受発注・計画・進捗・実績・負荷・原価を「見える化」し、生産効率向上につながる。CAD/CAMと連携しているのが特長。IoT機器と連携し、稼働監視ができる。不良防止、補修部品の予測、技能伝承などカスタイマイズも可能。
CGTech NCプログラムを最適化
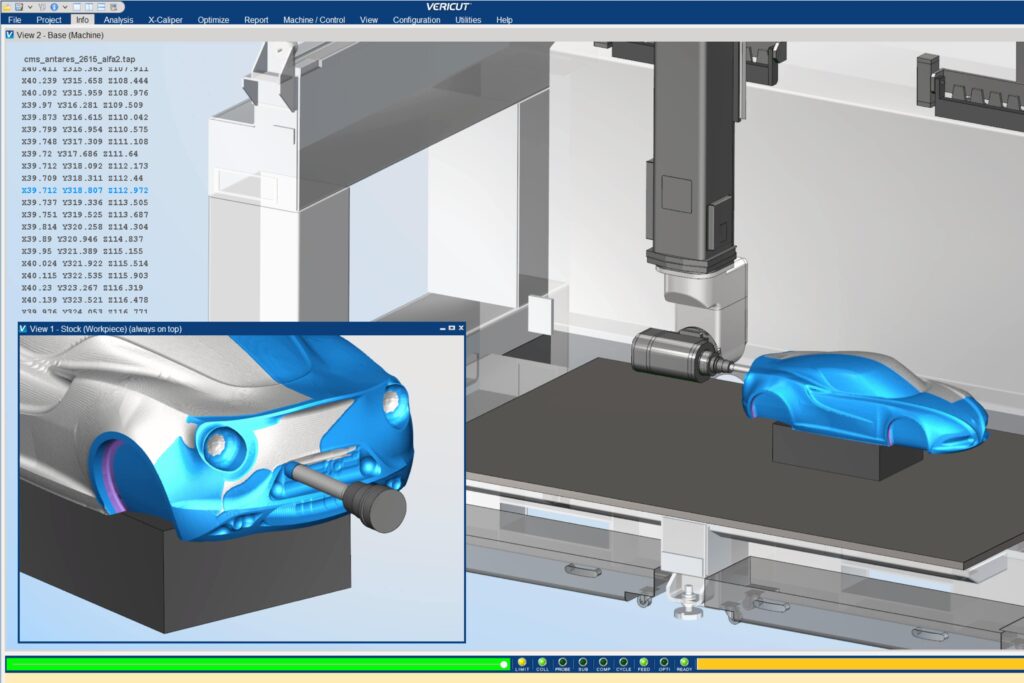
NCマシンシミュレーション「VERICUT」
NCプログラムで行うため、実際の加工に近いシミュレーションが可能。5軸や複合機だけでなく、積層造形にも対応する。また、NCプログラムの条件を分析・最適化するForce機能では、材料、切削工具、機械加工条件に対し効果的なNCプログラムが作成できる。
セイロジャパン 機上測定プログラムを作成
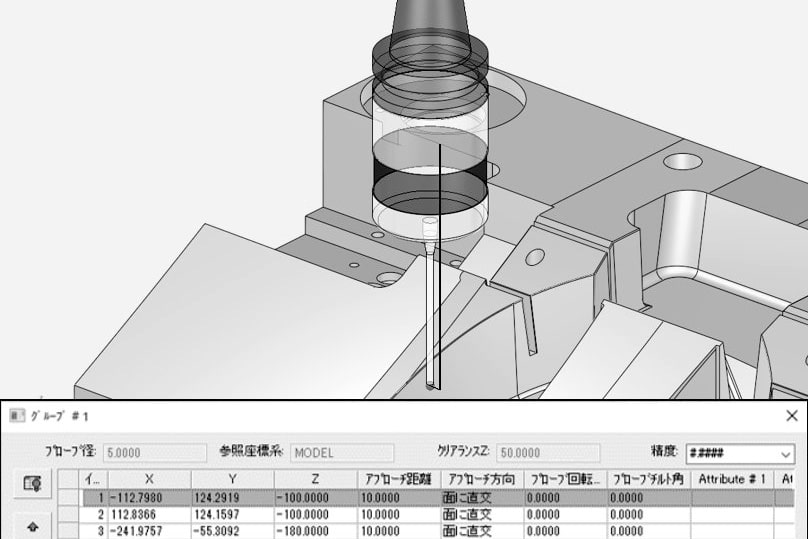
「Cimatron」機上測定ツール
「Cimatron」を使って機上測定に必要な測定NCプログラムを作成可能。測定困難な曲面上や勾配面上の点も測定できる。設計、加工軌跡、機上測定など全工程を一気通貫で統合も部分最適化も可能なシステムとして利用できる。
PART5
記者の目
これから日本の金型企業を取り巻く事業環境は人手不足の深刻化や自動車の変革などによって大きく変化することが予測される。
こうした未来に金型企業がいかに立ち向かっていくか。その大きな武器になるのが「DX」だろう。IoTやAIといったデジタル技術を活用することで、これまでの常識や慣習にとらわれることなく、より良い形での金型づくり、経営が可能になるはずだ。
金型新聞 2021年9月10日
関連記事
金型はこれまで、金型職人の頭の中で製品形状や金型設計を描き、経験やノウハウで調整し、製造してきた。そして金型の「匠」の技は「背中」を見て学ぶもので、習熟への時間はとても長かった。しかし近年では、工作機械やCAD/CAMと…
ギガキャストで需要広がる 大型ダイカストマシンで自動車の構造部品を一体鋳造する「ギガキャスト」が注目を集めている。国内のダイカストマシンメーカーは型締力9000tのマシンを開発。海外では1万3000tで試作が行われるなど…
ササヤマが今期スタートした新中期経営計画「SAIMS247」。その中核事業となるのが金型製作期間の半減だ。デジタル技術や経験を駆使し金型づくりの大改革が進む。 全ての部品をQRで管理 材料に書かれたシリアルナンバー。入力…
デジタル技術の進化で、相次いで登場する新技術。次世代の匠はそれらの技術を金型づくりにどのように活かしているのか。また、それら能力を習得するには、どのようなスキルや育成が必要なのか。本特集では、様々ある新技術の中でも、次世…