新中期経営計画「SAIMS247」。その狙い、そして目的は。笹山勝社長に聞いた。 「短納期」を強みに、海外での競争に打ち勝つ SAIMS247の3カ年の目標は金型の製作期間半減。その真の狙いは金型の競争力の再強化です。当…
【特集】新時代の金型自動化
現場の生産性向上、人手不足の解消に向けて、多くの金型企業が関心を寄せる自動化。近年の自動化技術は目覚ましい進化を遂げており、ロボットやIoT、AIなどの次世代技術によって、これまで以上に高度な自動化が可能になっている。こうした技術革新が進む一方で、自動化にどう取り組むべきか悩む金型企業も多いのではないか。本特集では先進企業の取り組みや機械メーカーの自動化提案などを通じ、新時代の金型自動化を紹介していく。
目次
PART1:オオイテック 全自動金型加工システム
PART2:牧野フライス製作所 金型自動化の要諦
PART3:金型メーカーアンケート Q何を自動化したいですか?
PART4:BESTOWS 加工プログラムを自動作成
PART1
オオイテック / 全自動金型加工システム
少子高齢化による人手不足が進み、顧客からの納期短縮の要求が年々強まる中、これまで以上に生産効率を向上させようと、金型企業でも自動化の動きが加速している。群馬県太田市に本社を構え、自動車部品向けプレス用金型を手掛けるオオイテックも徹底した金型づくりの自動化に取り組む金型企業の1社だ。工作機械メーカーなどと共同で構築した全自動加工システムを導入し、外注部品の内製化や工程改革に挑み、工期半減を目指している。
外注部品の内製化 / 工期半減を目指す
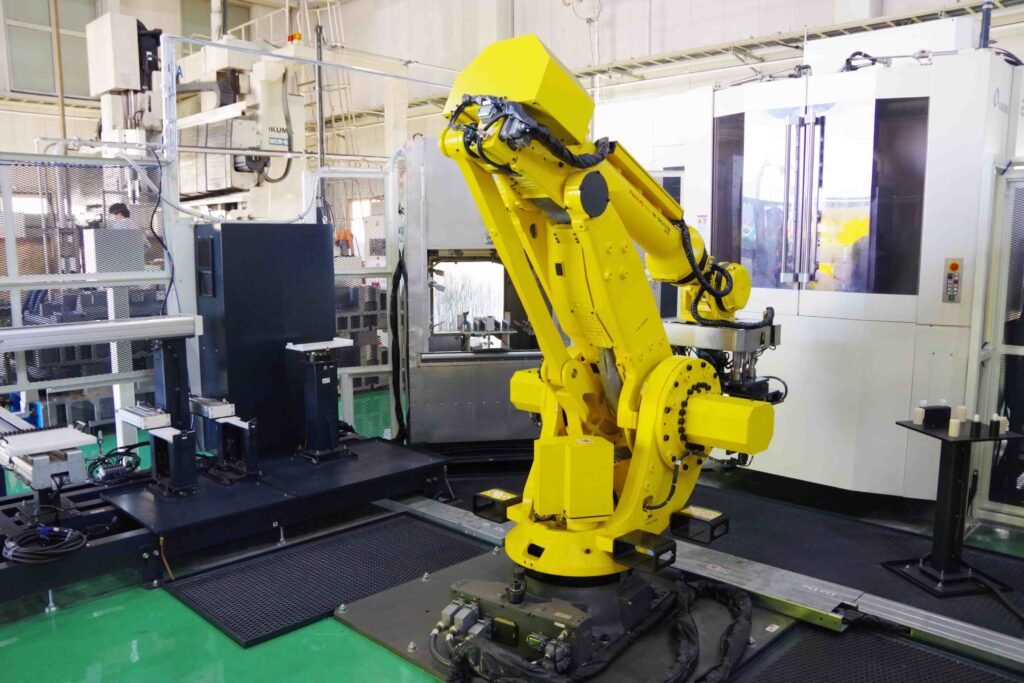
オオイテックは自動車の骨格部品向けプレス用金型の設計、製作に特化した金型企業。特に1480MPa級までの超高張力鋼板(超ハイテン材)に実績があり、自動車メーカー各社の多くの車種に採用されている。
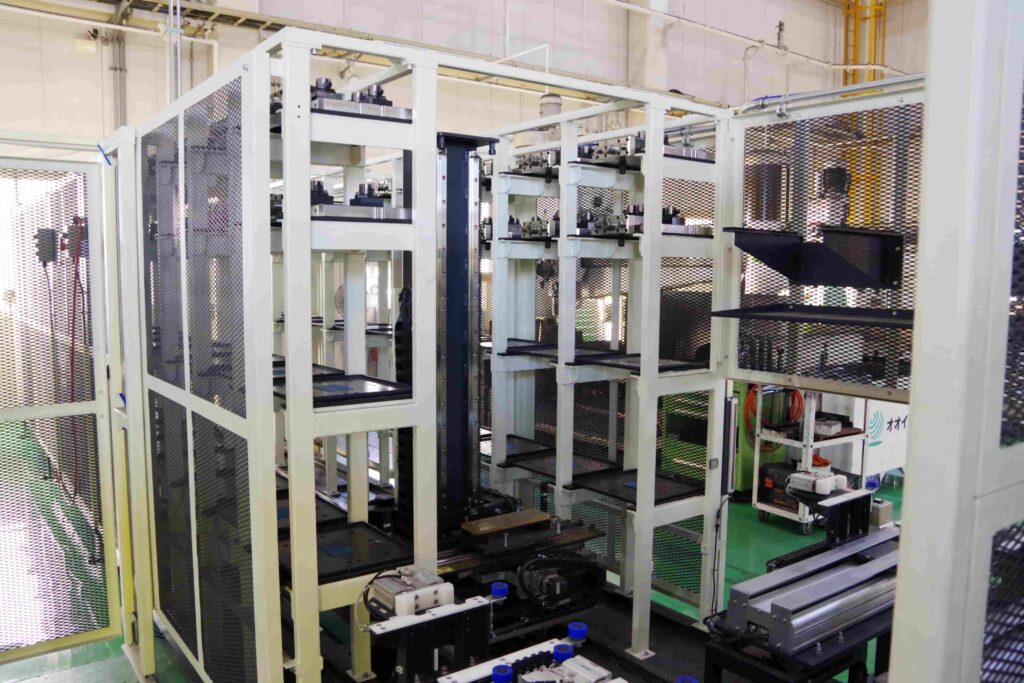
「昔は鋳物を加工すれば金型が成立していたが、今は鋳物に鋼材を付けないと成立しなくなっている。従来に比べ、鋼材を加工する量が増え、外注費もかさんでいた」(板橋紀幸常務)。そこで、これまで外注していた鋼材加工を全て社内に取り込むために、約2億円をかけて全自動加工システムを導入。今年1月から本格的に稼働を開始させた。
同社が自動化に取り組む目的の一つが外注部品の内製化だ。毎月約30型を生産している同社だが、その内の半分は協力工場が製作している。また、鋼材の穴加工やキー溝加工といった構造部の加工は全て外注化していた。
同システムは横形マシニングセンタ(MC)と多関節ロボット、ストッカ、洗浄機、段取り替え装置を組み合わせ、素材投入から取り出しまでの完全自動化を実現した。どんなサイズ・形状にも対応し70×45㎜から320×200㎜まで加工することができる。
システムの仕組みは、パレットに鋼材(最大4つ)とQRコードを並べ、ロボットに搭載されたカメラでQRコードを読み込むことで鋼材を認識し、NCデータとの紐付けを行い、自動加工を可能にする。ワークの搬送はロボットが行い、ストッカには最大60個のワークを搭載することができる。
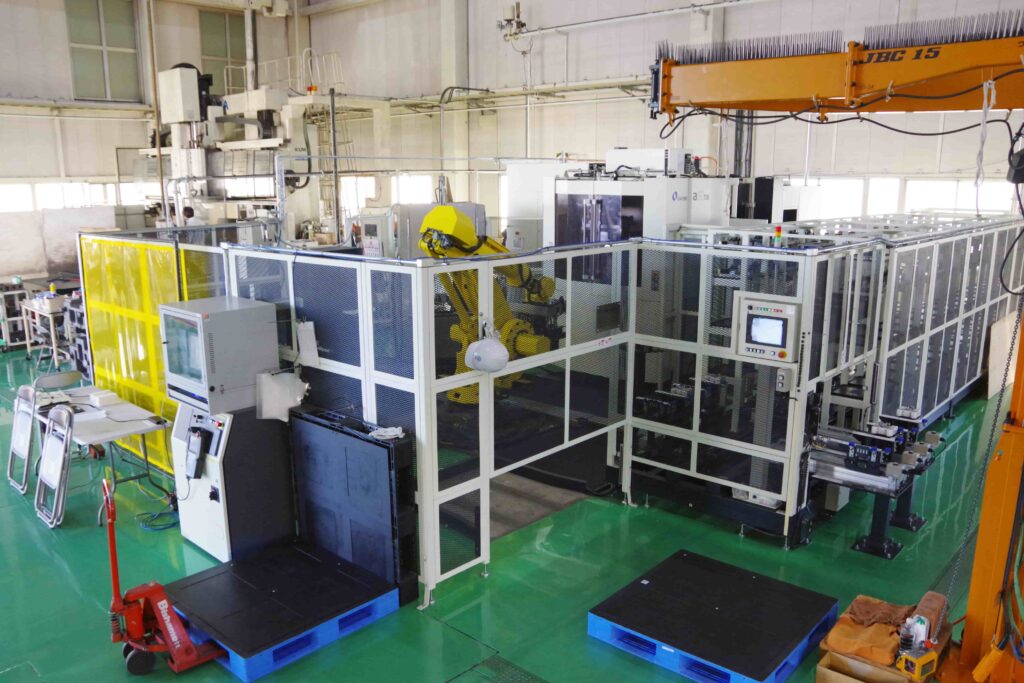
ストッカから取り出した鋼材は加工前に洗浄を行い、MCに投入される。治具は加工の種類によってパターン化され、構造部に関わる加工ではバイスを使用。一方、形状加工ではプルボルトを使った治具を7パターン揃え、鋼材のサイズによって使い分ける仕組みになっている。NCデータの中には治具の情報も含まれており、自動的に治具が選定される。
また、形状加工で必要となる段取りも段取り替え装置によって自動化。鋼材を治具プレートに固定するためのボルトの取り付け、締め付け作業も自動で行うことができるようになっている。
さらに、使用する全ての工具ホルダにはICチップを搭載。ツールプリセッタで測定した工具の情報をICチップに書き込み、ATC(オートツールチェンジャー)内のスキャナでその情報を読み取ることで最適な工具の選定を可能にしている。
鋼材の投入と工具管理の一部以外は人手を必要としないこのシステム。これを動かすカギとなるのが加工プログラムだ。プログラムの供給が滞ると、システム全体の稼働が停止してしまうため、同社では簡単かつ早くプログラムが作成できる仕組みを構築した。使用工具の標準化や工具毎の加工条件をデータベース化することで工具選定を容易にした他、加工方法の設定も蓄積されたデータをもとにテンプレート化。加工形状を選択すれば、工具レイアウトと加工動作が割り当てられるようになっている。
現状は構造部の加工のみに対応しており、すでに9割ほどを内製化した。今後は5軸MCを導入し、形状加工まで可能なシステムに改良していく考え。「形状加工が可能になれば、さらなる短
納期化を図ることができる」(深掘元広製造部長)。
この短納期化こそが同システムを導入したもう一つの目的。現在の金型製作工程は鋼材加工、鋳物加工、組付け、ならい加工と直列で流れている。それを自動化システムによって、鋳物加工と並行して鋼材加工も進められるようになる。「通常4週間かかっていた工期を2週間に半減させることができ、大幅な納期短縮が図れる」(深掘部長)。
今後は大型加工の高精度化にも取り組み、仕上げや組立工程の工数削減を目指す。高精度対応の大型加工機を導入する他、工場内の温度管理にも注力する。「究極の未来像は人が必要最低限しか介在しない“オートファクトリー”。その理想に向かって取り組みを進めていく」(板橋常務)。
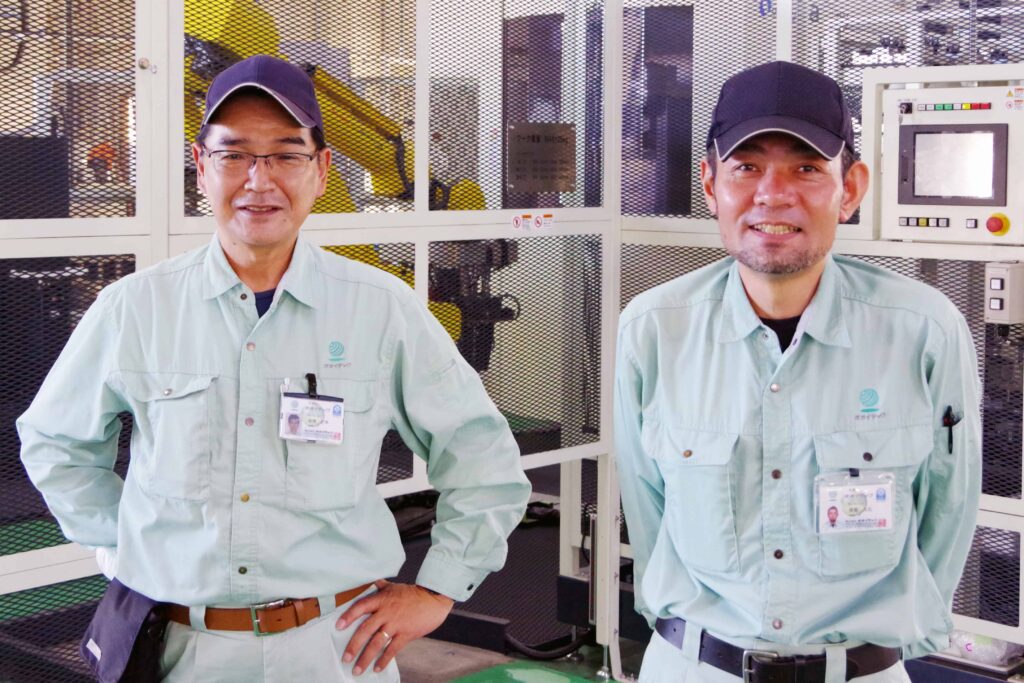
会社概要
- 本社 :群馬県太田市西矢島町84-1
- 電話 :0276-38-2200
- 代表者 :早川みちる社長
- 創業 :1963年
- 従業員 :70人
- 事業内容:プレス用金型設計・製作
PART2
牧野フライス製作所 加工技術本部 / 金型自動化の要諦
目標設定や全社的対応 / 工程の見える化も
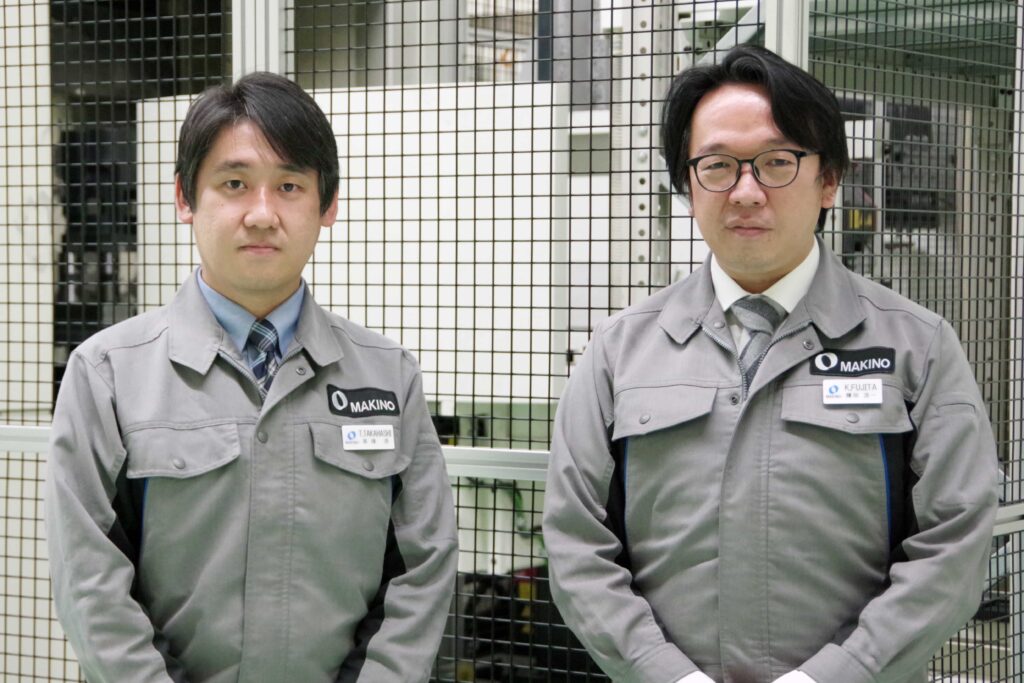
二人とも金型の自動化は難しいと指摘する。藤田氏は理由の一つに「金型は無限品種一品生産なため」とワークの多様性を挙げる。「部品の種類が多く、10社あれば10通りの自動化や利益の出し方があるため、パッケージでの提案が難しい」。
高橋氏は「治具の選択や製造プロセスなど『文化』の違いも大きい」と話す。「同じ部品でも企業によって作り方は異なる」ため、パッケージに当てはめると「手間が増える」こともよくあるという。
では、どこから取り組むべきなのか。藤田氏は「いつまで、どこを自動化し、何で利益を生むのかという目標設定が必要」という。「今はお金をかければ大半の自動化は実現できる」が、そんな企業は滅多にないからだ。また「全社的に取り組むこと」も重要という。「加工の自動化のために設計プロセスを変更するなど、結果的に全社的な課題となることが多い」。
高橋氏は「工程の見える化」も必要という。「作業や工程を明確にし、標準化しないと目標設定も難しい」からだ。代表的なのがプログラム供給の自動化。「自動化には安定した品質のプログラム供給は欠かせない。『なぜプログラマーがそのパスや工具を選択したのか』を分析し、標準化しないと安定供給はできない」。
このように難しい金型づくりの自動化だが、藤田氏は「作り方自体は変わっていないし、これまでも個別の工程での自動化はしてきた。全ての工程をつなぐ意識が芽生えてきたのは大きな変化だが、できることから始めればいい」と話す。
では、今後自動化を進める上での課題は何か。高橋氏は「アウトプットの部分」と指摘する。オオイテックのように、プログラムや治工具など機械にワークを投入するまで「インプット」の自動化は進んでいる。今後は「測定や組付けなど加工後のアウトプットの自動化が求められる」という。
そのために、高橋氏は「当社の技術だけでなく色々な企業と手をつなぐことも必要になる」と話す。その上で「お客様と一緒になって最適な自動化を創り上げていきたい」(藤田氏)。
PART3
金型メーカーアンケート Q:何を自動化したいですか?
A:ボトルネックの設計と測定を
設計と測定—。特集に合わせて実施した自動化に関するアンケートで、金型メーカーは自動化を進める上で、入口と出口となる2つの工程に課題や興味を持っていることが分かった。
アンケートでは、まず「自動化に興味があるか」について尋ねたところ、全社が「興味ある」と回答。しかも、全ての企業で、最重要課題もしくは重要課題の一つと答えた。
自動化を経営課題と認識していることから「自動化に取りくんでいる」(21社)という回答が最も多かったが、一方で「どこから取り組んでいいかわからない」(15社)が2番目に多い回答に。課題とは理解していても、どこから着手すべきか悩む企業が多い。
次いで、どのような工程の自動化に取り組む(取り組もうとしているか)、興味があるかを聞いたところ(複数回答可)、「設計やCAMの自動化」(30社)が最も多い。中には「AI技術を使って設計業務完全自動化できないか」とする意見もあった。
次いで多いのが「測定工程」(23社)。「磨き工程の自動化」(14社)という声も多く、金型の製造プロセスの入口と出口の自動化が課題として浮かび上った。
切削加工では、設計や測定に比べて、回答は少なかった。すでにATCやAWCによる自動化はすでに進んでいることもあるのだろう。ただ、切削加工では「搬送の自動化(14社)」よりも、「脱着に関する自働化(20社)」の要求が多く、段取りでの作業効率化を望む企業が多い。
自由回答では、「見積利の自動化」や、「日程工程の自動化」といった加工に関するものの自動化を進める意見もあった。
200人中49人から回答
金型メーカーら200人にメールでアンケートを送付し、49人から回答をもらった、複数回答可。ウェブサイトに後日自由回答を掲載します。
PART4
BESTOWS 加工プログラムを自動作成
西田勇社長インタビュー
神戸大学発のソフト会社BESTOWSが開発した「BESTOWSシリーズ」は、製品の3Dモデルをインプットして簡単な操作をするだけでNCプログラムを自動作成する。時間と手間をかけていたプログラム作成の時間を短縮でき、熟練技能者が持つ長年の経験やノウハウも必要ない。製品の特徴や開発の目的、そして今後の目標は。開発者の西田勇社長に聞いた。
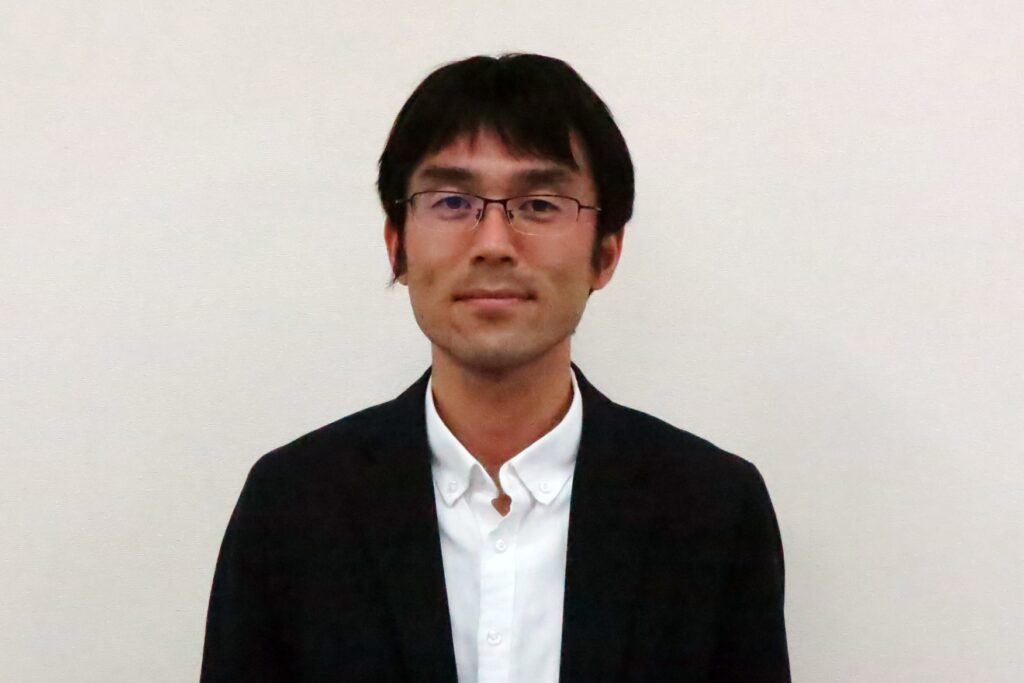
にしだ・いさむ
1985年生まれ、大阪府出身。2012年神戸大学大学院工学研究科博士課程修了、同年シスメックス入社。ソフトウェア開発に従事後、2016年神戸大学大学院工学研究科助教に就任。2018年BESTOWS設立。
熟練者と変わらぬ加工
どんなことができるソフトか。
3DCADデータとワークの材質を入力するだけで、NCプログラムを自動で作成できるソフト。①3DCADデータを輪切りにして解析②解析データを基に12の選択肢から加工割付を選択③加工割付から工具を選定④ワークの材質と工具データを基に加工条件を設定⑤必要な領域を切削するための経路の割り出しの5つの工程を自動で行い、プログラムを作成する。
従来の自動化ソフトは、4つ目の加工条件は手動での入力が必要だった。このソフトは過去の何万という加工データを関数化しており、最適な加工条件の設定も含めた一気通貫の自動化ができる。
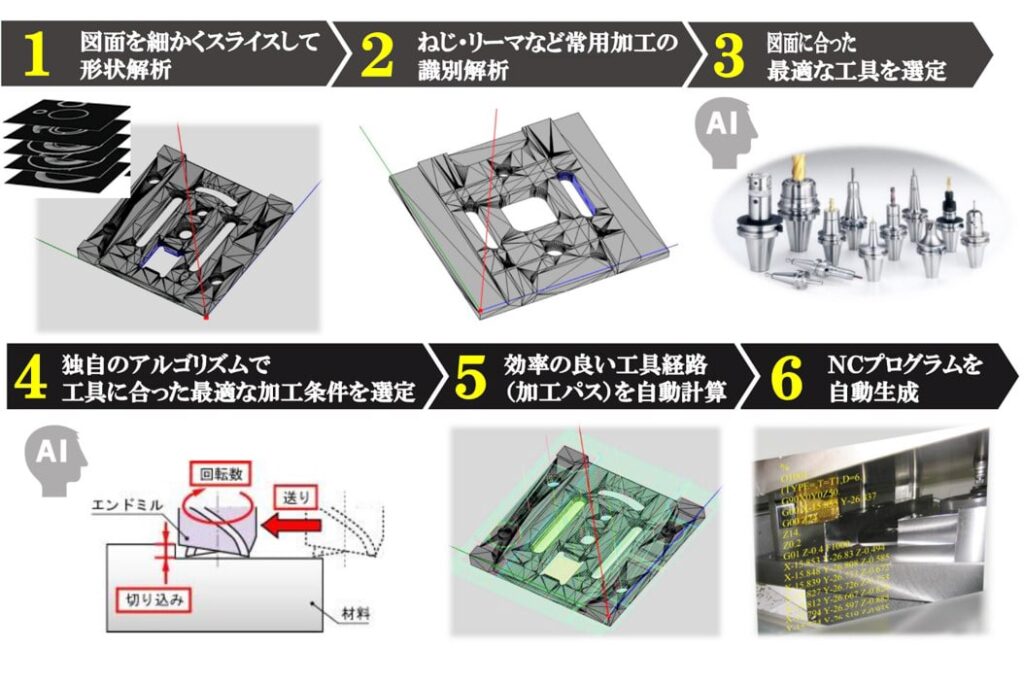
どんなことを改善できるか。
熟練の技能者が1時間以上かかっていたNCプログラムの作成を、数分に短縮できる。加工の経験がなくとも扱えるため、新人や経験の浅いパートタイマーでも熟練者と変わらないワークができる。特に、大量のプログラムを作成する必要がある少量多品種の部品加工や金型ほど、相性が良いはず。
現場では高度なものから簡単なものまで全てのプログラム作成を熟練者が行っていることも多く、簡単なものは自動化し、高度な加工に注力するための活用が進んでいる。
開発の背景は?
研究者は、加工現場の実態をよく知らない。私自身、ソフトを現場に持って行くも、現場の実態と合わず使われないことが多かった。そんな中、アルムの平山京幸社長と知り合い、アルム子会社の金属加工現場とタッグを組んで研究ができた。トライ&エラーを繰り返せる環境で開発に臨めたので、現場に即したソフトウェアが開発できた。
今後の展開は。
現状では、どんな形状のワークでも作れるわけではない。ポケットや穴、凸形状などの簡単なワークや、簡単な斜面や1側面についている曲面の加工プログラムは作成できるが、曲面の多い複雑な加工プログラムの作成までには至っていない。
今後は金型向けや同時5軸など、より高度な加工を行えるように都度アップデートを行っていく。また医療機器メーカーと共同で、差し歯や人工骨プレートを削るための専用機の開発も進めている。
金型新聞 2021年11月5日
関連記事
デジタル技術を活用してビジネスモデルや業務プロセスを変革するデジタルトランスフォーメーション(DX)。しかし、人が介在する金型づくりでDXを進めるのは簡単ではない。金型企業はDXをどのように考え、取り組むべきなのか。先進…
協力企業との連携推進 時期によって業務の量に差が生じることは少なくない。特に金型業界では、製品のモデルチェンジや更新のタイミングなどに受注が集中するため、繁忙期と閑散期で現場の稼働状況は大きく異なる。繁忙期には残業や休日…
設計・解析ノウハウ中国で蓄積 ギガキャストで先行する中国でギガ向け金型を製作し、そのノウハウをベースに国内でのギガ関連の需要開拓を狙うのが共立精機だ。構想段階からの設計相談や解析などの技術サポートを提供する一方、国内では…
受託などサービス拡充 AMに必要なデザイン設計や材料、各種3Dプリンタ積層造形装置メーカーなどで構成される「日本AM協会」は近畿経済産業局施策「kansai‐3D実用化プロジェクト」で具体的なAM活用検証を行い、成果を発…