新中期経営計画「SAIMS247」。その狙い、そして目的は。笹山勝社長に聞いた。 「短納期」を強みに、海外での競争に打ち勝つ SAIMS247の3カ年の目標は金型の製作期間半減。その真の狙いは金型の競争力の再強化です。当…
進化する超硬加工ー特集ー
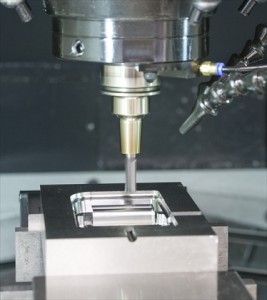
超硬合金を金型材料として使う動きが広がりつつある。これまでは長寿命化などのメリットはあるが、加工しづらいことがボトルネックとなり、一部の金型でしか利用されていなかった。しかし近年、切削加工ができたり、放電や研削加工技術が進化したりしたことも超硬合金活用の後押しとなっている。今まで使われていた冷間鍛造型に加え、プレスやレンズ金型などへの応用も期待できる。現状では超硬加工は多くないが、次代の加工として注目されつつある。
超硬合金を金型材として活用するメリットのひとつは長寿命化だ。高度HRA90以上という硬さがあるのだから当然だ。さらに、HRA80超程度ながら、耐蝕や耐衝撃性に優れる汎用的な素材もあり、選択肢が広がっている。また、長い間安定した成形できるので、高精度でピン角が求められるような金型などでも超硬合金は有効だ。
しかし、課題は加工のしにくさだ。切削することは難しく、放電では時間もかかり、研削加工では形状に制約があるなど、加工しづらいことが何よりネックになっていた。
だが、近年は加工技術が進化し、以前に比べ加工しやすくなってきた。その筆頭に挙げられるのが切削加工だ。ダイヤモンドコーティング工具やPCD(多結晶焼結ダイヤモンド)工具などが登場したことで、これまで出来なかったミーリングやドリル加工までできるようになった。合わせてマシニングセンタも剛性の高い機種や高精度加工を可能にする機種などが登場。
放電加工では制御技術の進展などにより、銅タングステンより安いグラファイトを活用し、スピードを上げた加工も可能。研削ではクーラントの進化などにより、深い切込みでの研削できるようになった。治工具は超硬専用のマグネットチャックなどもある。
超硬合金の金型を長年手がける、東京鋲螺工機の高味寿光社長は「それぞれの特性を見極めて最適な加工を選択すべき」と指摘する。
だが、こうした加工技術の課題が解決できれば、今も多く超硬合金が使われる冷間鍛造型以外にも広がる可能性もある。ロット数が多くピン角が求められるような精密プレス型や、電気接点用金型、高温で過酷な成形条件のガラスレンズ型などでの応用が期待されている。
現時点では、超硬合金を金型に活用することはまだ多くないが、増える可能性も秘めている。それに応じて超硬合金を加工する技術は今後も進化も続きそうだ。

鋳造金型メーカーの日型工業が取り組んでいるのは耐衝撃性に優れる汎用的な超硬合金の切削加工だ。鋳造の砂型などでは砂が金型を削るなど金型の摩耗が激しく、硬い材料が求められている。これまではSKD11の焼入れ鋼なども削っていたが、「もっと硬い材料はないか」(技術開発チームの笠松士郎リーダー)と考えたのが超硬加工へのきっかけだった。
一昨年には超硬合金「G2」(硬さHRA91)という硬い材料を切削加工にも成功。今回は「ベベルギア金型などでの実用性が高い」(笠松氏)と言われる、耐衝撃性に優れる超硬合金「RT53」(同HRA85・5)を切削加工した(写真)。
ワークサイズは65㎜角、深さは25㎜。使った加工機は牧野フライス製作所の「V56ⅰ」。仕上げ加工だけで、R0・5~3㎜までのユニオンツールのダイヤモンドコーティング工具を「10本ほど使って加工した」(笠松氏)。出来上がったワークの寸法精度は約±10μm。仕上げの切削加工のみだが、加工時間は約24時間だったという。
何よりの加工の難しさは「柔らかくて粘いため、工具摩耗が大きかった」ことだ。このため「加工条件などをメーカー推奨ではなく、自ら模索しながら設定した」という。
笠松リーダーは「今回は削ることに主眼を置いたが、電着工具なども含め工具の使い方を工夫できる余地は大きく、コスト、時間はもっと改善できる」としている。今後の超硬合金の加工について「深いものは放電などで、浅いものは切削など棲み分けが進むのではないか」とみている。
日型工業
▽住所=埼玉県川口市南鳩ケ谷3―20―15▽電話048・283・6111▽代表者=渡辺隆範社長▽従業員数=35人▽営業品目=重力鋳造、低圧鋳造、砂型鋳造金型など。
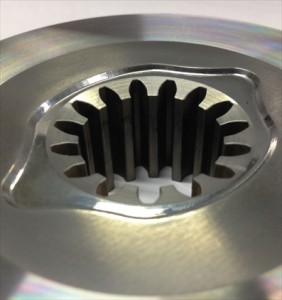
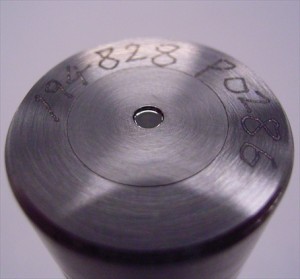
冷間鍛造金型メーカーの東京鋲螺工機では4つの方法で、超硬合金を加工している。熟練工による手彫り、ダイヤモンドバイトや砥石を使った研削・旋削加工、放電加工、そしてマシニングセンタでの直彫りだ。高味寿光社長は「それぞれの加工特性を理解し、最適な方法で加工することが重要」とコストや精度などで最もメリットのある加工法を選択し、付加価値の高い金型づくりに取り組む。
ネジやリベットなど冷間圧延用金型は1分間に100から1000個も成形するため、金型には高い耐久性が求められる。そのため、同社では1980年代から、耐衝撃性・摩耗性に優れた超硬合金が金型材として使ってきた。当初は鉄製の棒に粉末ダイヤを付け、熟練工が手彫りで加工していた。現在でも、大物の穴加工や丸物加工など単純形状は手彫りの方が早いという。
その後、放電加工機を導入し、より複雑な3次元の自由形状が再現できるようになった。同社では、電極加工と磨きに高い技術力を持つ。除去体積が大きく、深穴のワークでは放電加工が適する。ただ、電極加工や磨きの工程があるため、生産性が悪く、コストもかかるという欠点があった。
そこで、2011年から高精度マシニングセンタ「IQ300」(牧野フライス製作所)による直彫り加工「Tokyo‐ACE」に着手した。とくに浅物加工でメリットが大きく、深さ0・5㎜、直径2㎜の電気接点用の金型では、放電加工で50分だった加工時間が10分にまで短縮し、コストも大幅に削減。また圧縮の残留応力により硬度が向上し、型寿命は1・5倍に伸びた。
高味社長は、「それぞれの加工法に一長一短がある」とし、「手彫りは技能伝承、放電では生産性の向上、直彫りは加工範囲の拡大」と課題を挙げる。「機械や工具は日夜進歩しているので、常に最新の情報を仕入れ、今後も4つの加工技術を深めていく」。
東京鋲螺工機
▽埼玉県新座市野火止7‐13‐3▽電話048・478・5081▽代表者・高味寿光社長▽従業員・30人▽営業品目・ネジ、リベット、ピン、接点などの成形用ヘッダー金型、超硬パンチ・ピン、超硬合金製部品加工など。
金型新聞 平成27年(2015年)7月2日号
関連記事
▶︎▶︎採用目指す動き広がる ▶︎▶︎金沢大学古本達明教授に聞く 金属3Dプリンタの未来「将来不可欠なツールに」 ▶︎▶︎事例①日産自動車 ダイカスト部品で活用探る ▶︎▶︎事例②J・3D ハイブリッド構造でコスト抑制 …
52人が考える、リーダーが持つべきもの 自動車の電動化や市場のグローバリズムが加速する混沌とした時代。金型メーカーの経営者は、この新時代にどのような能力が必要と感じているのか。進むべき方向を示す「決断力」か、恐れず挑戦…
工作機械や工具、ソフトウェアなど金型づくりを支えるツールの進歩はすさまじい。こうしたツールの進化によって、加工精度は飛躍的に向上した。加工速度や微細化、自動化、計測技術なども数年前とは比較にならないほど性能や機能が進化し…
目次金型メーカーアンケート型取引に関する政府の動向金型メーカーの実例紹介型取引適正化推進協議会座長 細田孝一氏に聞く記者の目 取引環境改善も道半ば 金型メーカーアンケート 政府が2016年の世耕プランで、取引環境の改善を…