金型づくりの世界では、自動化やAM、脱炭素向けなどの最新技術が数多く登場し続けている。その進化は止まることがなく、4年ぶりに開催されたJIMTOF2022でも多数の最新技術が披露され、注目を集めた。今年最後となる本特集で…
【特集】感動ワーク
魅了するワークの加工プロセスをひもとく
品質の優れたワークはそれを加工した機械や工具などの性能や、技術者の技能の高さを物語る。人を魅了する「感動ワーク」はどのような機械や工具、ソフトを使い完成したのか。多彩な感動ワークとその完成までのプロセスとノウハウをひも解く。
PART1:イワタツール「焼入れ鋼などに深穴加工を実現」
PART2:オーエスジー「バリのない良好な加工面」
PART3:岡本工作機械製作所「切込み量20㎛で加工」
PART4:セイロジャパン「自由曲面のヘール加工を実現」
PART5:日進工具「ナノレベルを切削で」
PART6:三井精機工業「先端径φ0.02㎜のピンを連続加工」
PART7:三菱マテリアル「65HRC以上の高硬度鋼加工」
PART1
イワタツール「焼入れ鋼などに深穴加工を実現」
高硬度材の深穴加工
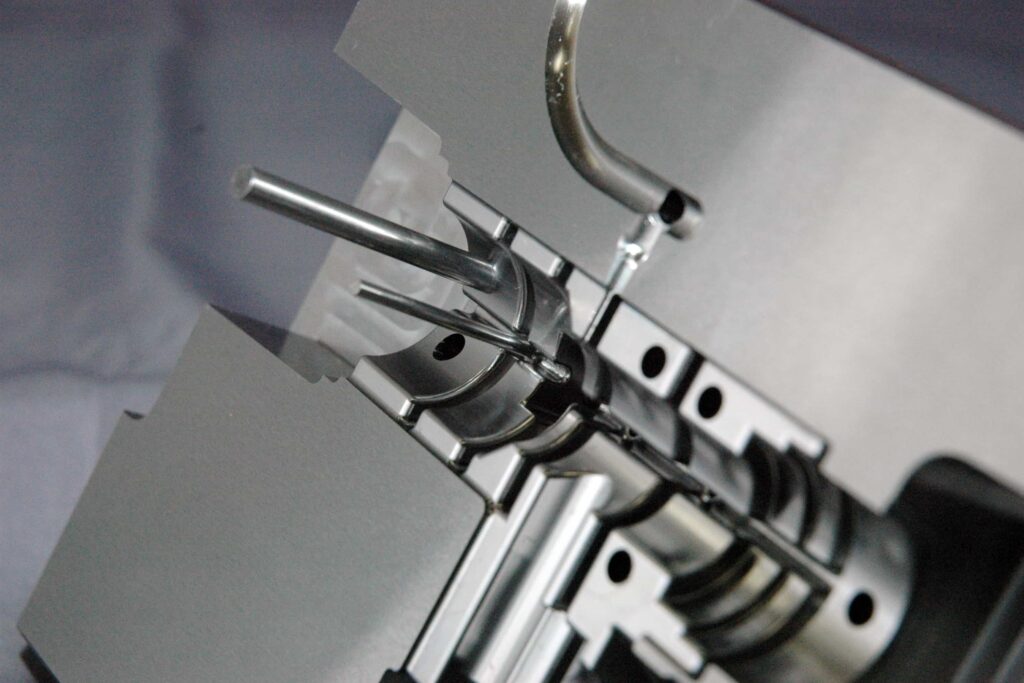
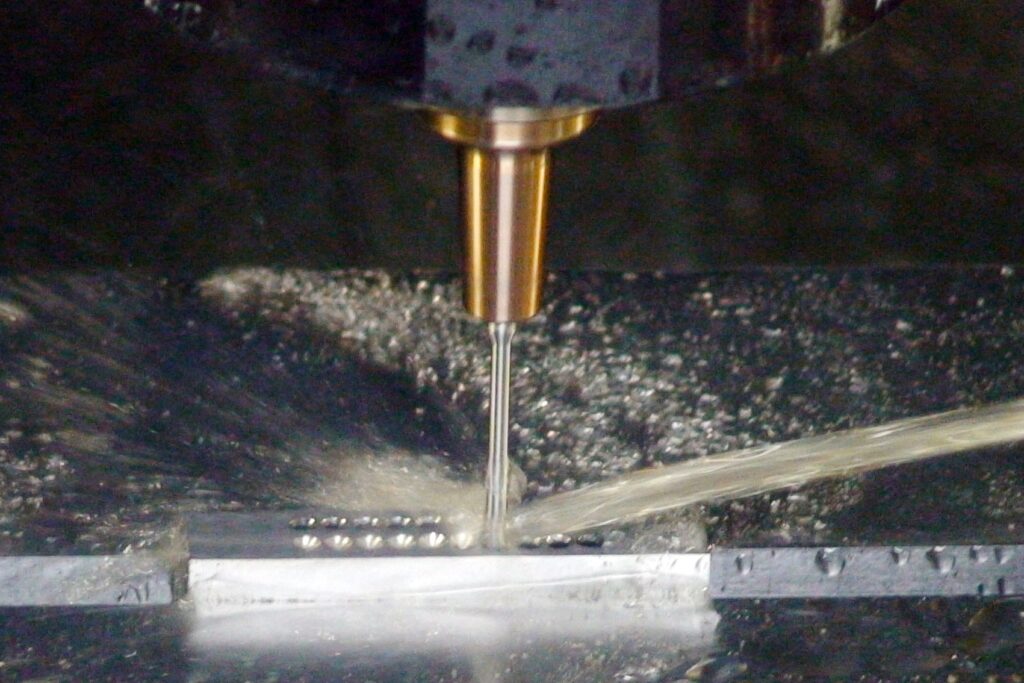
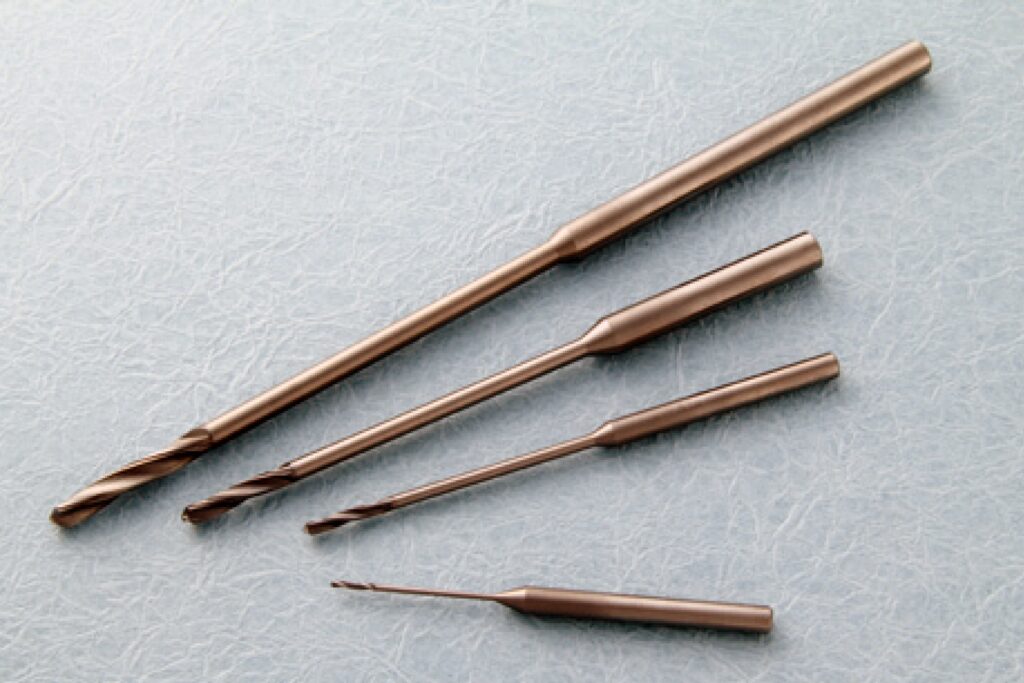
従来、焼入れ前に穴加工するのが常識だった。その常識を覆し、焼入れ鋼など高硬度材向けに深穴加工を実現したのが「トグロンハードロングドリル」だ。
この加工を可能にしたのが特長である『とぐろ』をイメージした独特な切れ刃ねじれを持つ刃先形状。金型分野ではH7以上の穴精度を出せるため、エジェクタピンなど深穴加工に最適。これまで熱処理後に細穴放電やワイヤーカットなど複数機械を使用していた加工をマシニングセンタに集約し、金型製作日数も3日から1日へ短縮した事例があり、金型メーカーの採用が飛躍的に増加した。
製作したワークサンプルはテスト加工時のもの。プラスチック金型の三洋技研からドリルで深穴加工がしたいと依頼があり、被削材STAVAX(HRC52±2)をトグロンハードロングドリル20D(TGHDL2CBALT20D)で貫通穴あけ加工を実施。加工条件(例)は加工径φ2㎜、加工深さ40㎜、切削速度25m/分、回転数4000回転/分、送り量0.04㎜/回転、送り速度160㎜/分、ステップ量0.5㎜で、リーマ無しで寸法通りに加工を実現(1穴加工時間は80秒以下)。
これをきっかけに、深穴加工向けの「トグロンハードロングドリル」が完成。「穴が曲がらないように精度の高い位置決めとドリルの折れを防ぐためにステップ加工を取り入れ、切粉の排出や冷却を行うこと、有効長の短いドリルから使用するなどのポイントを押さえるのがコツ」と岩田昌尚社長。現在も高硬度材(HRC40~72)と高精度をキーワードに展開中。
PART2
オーエスジー「バリのない良好な加工面」
銅電極を高精度・高能率加工
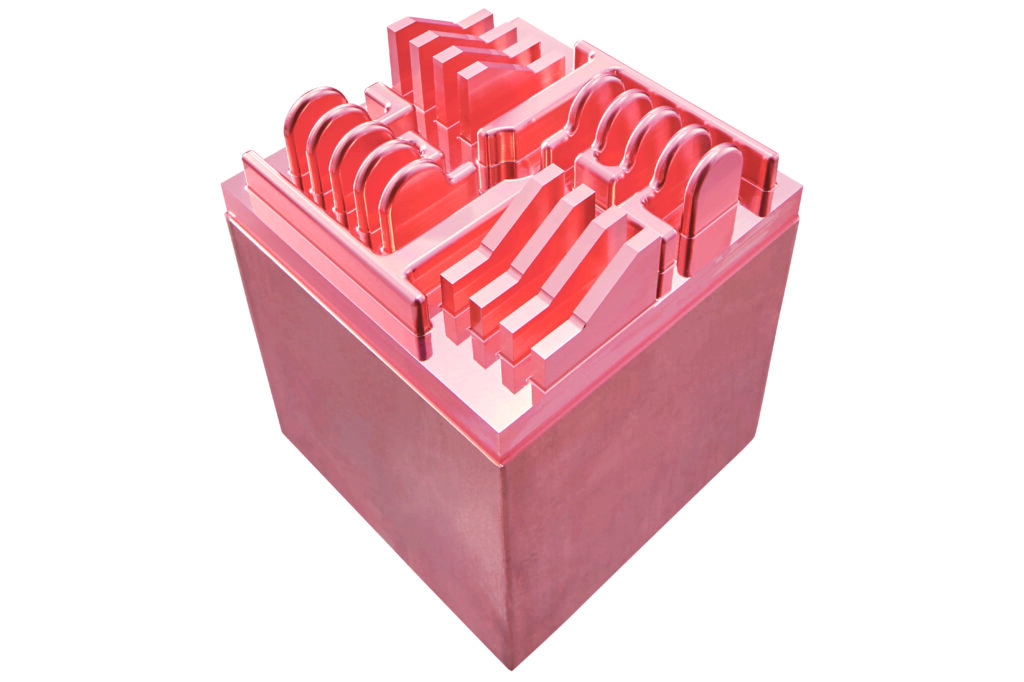
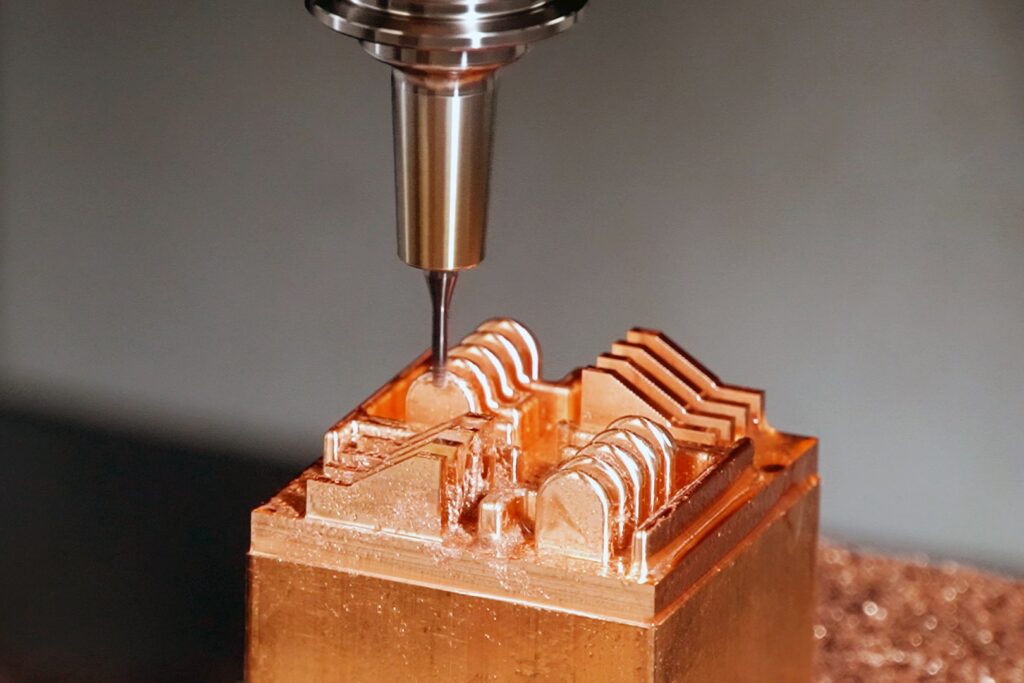
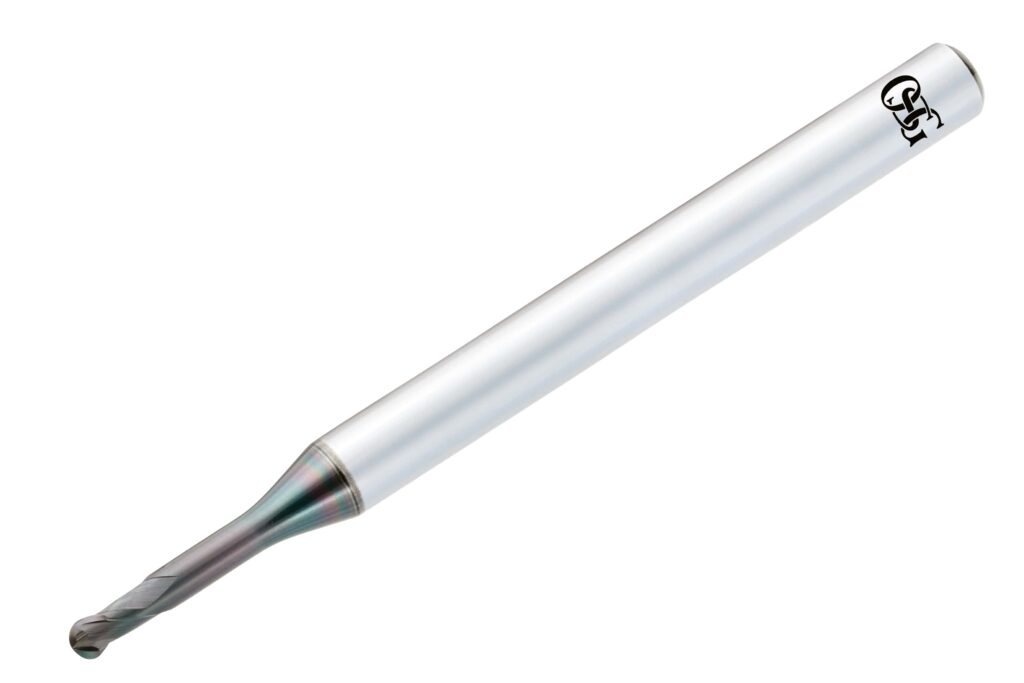
形彫り放電加工用の銅電極加工で、バリのない良好な精度を実現した。
銅合金の場合、比較的柔らかい特性から反りや バリが出やすいため加工寸法の変化が起きやすい。 そこで、銅電極用DLC超硬エンドミル「AE-LNBD-N」を用いた。
加工ワークには、銅電極で用いられるタフピッチ銅(C1100)を、工具は「AE-LNBD-N」のほか、非鉄用DLC超硬エンドミル スクエアタイプ「AE-TL-N」を用いた。荒加工は「AE-TL-N 3X15」で、切削速度50m/分、送り速度600㎜/分、切込み量 ap=11㎜ ae=0.3㎜とする高能率加工を実施した。
仕上げは「AE-LNBD-N R1×10×4」で切削速度127m/分、送り速度750㎜/分の等高線加工を行い、バリのない良好な加工面を高能率に加工した。
「AE-LNBD-N」は「DLC-IGUSS(アイグス)コーティング」を採用。表面の平滑さと極めて低い摩擦係数による耐溶着性や潤滑性に加え、刃先の高い耐摩耗性により長時間安定した加工精度が得られ、銅合金などの非鉄金属に抜群の威力を発揮する。また、鋭い切れ刃、優れたボールR精度とh4公差のシャンク精度により、バリのない良好な加工精度を実現する。さらに、R2未満の小径サイズには「外周部ティアドロップ形状」を採用。強バックテーパにより、点切削となりびびりを抑制することで、欠け防止、加工精度の向上を実現する。
「銅電極加工の最大の課題はバリの抑制。加工精度向上だけでなく、高能率加工も重要」としている。
PART3
岡本工作機械製作所「切込み量20㎛で加工」
セラミックス材の砥粒加工
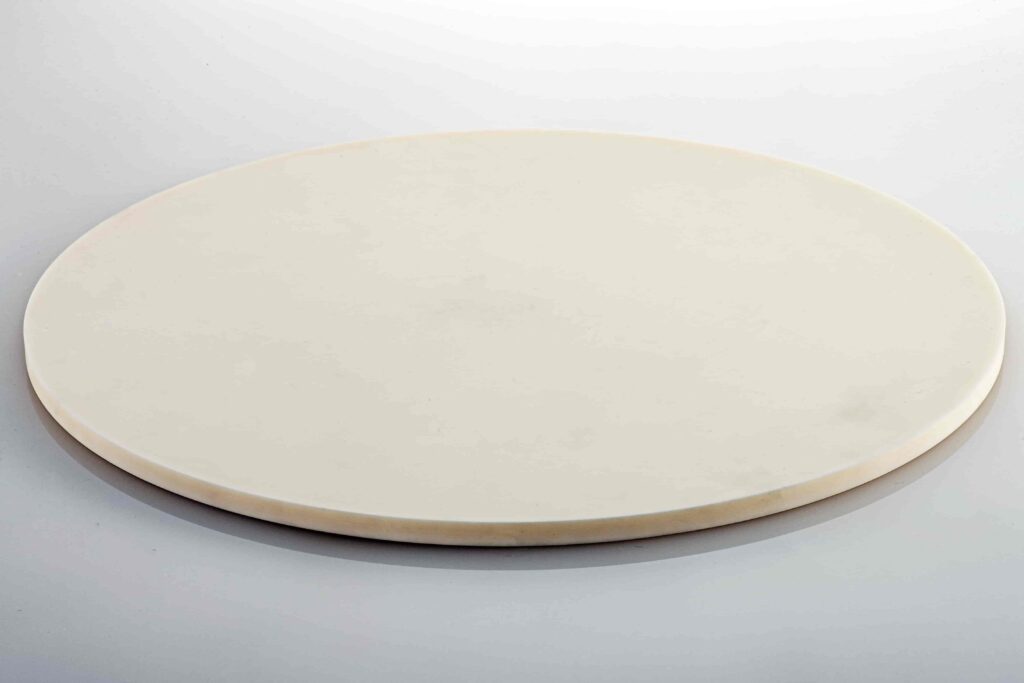
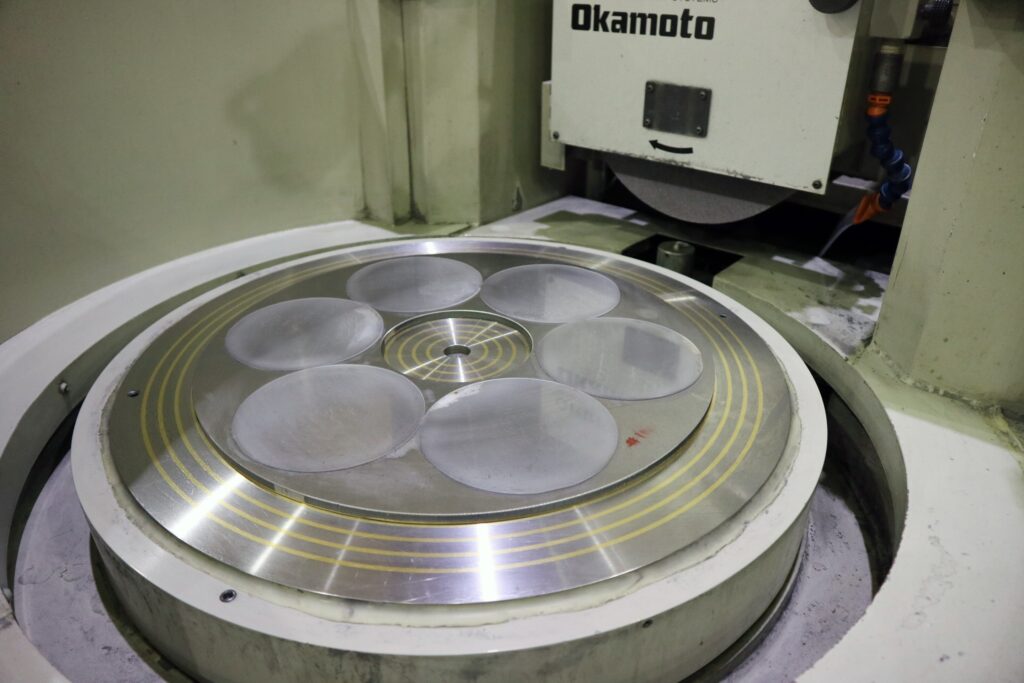
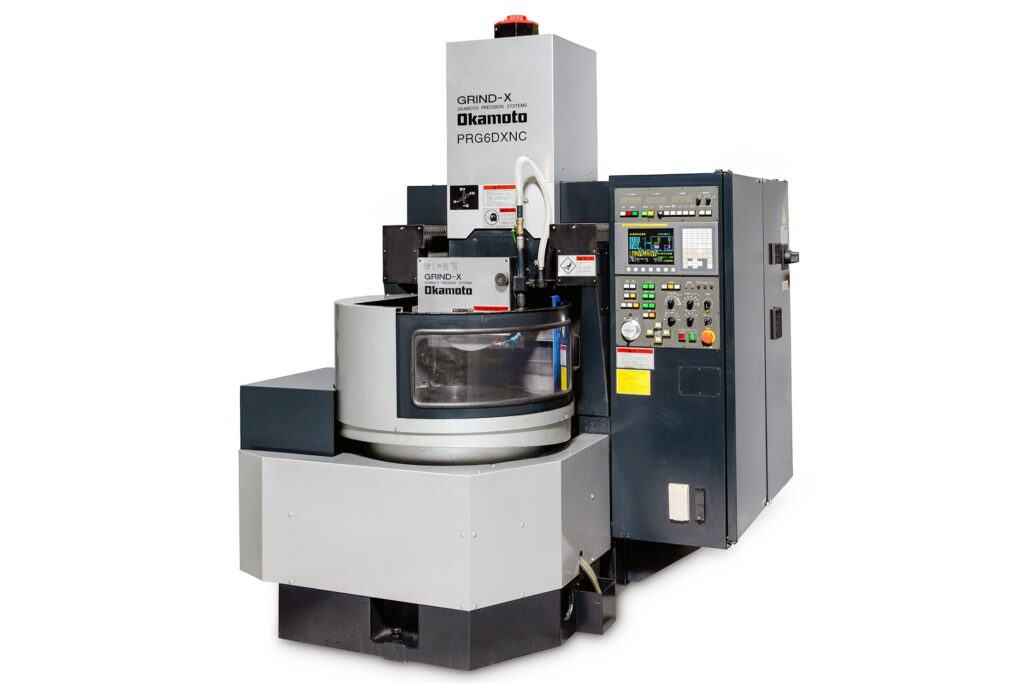
脆性材と呼ばれるセラミックス材は近年、医療部品や、半導体製造装置、次世代軽量化素材など、鉄系材料に変わる材質として大きく注目されている。その加工には保持方法・ろ過・砥石選定・加工ノウハウが必要とされており、砥粒加工も多く採用されている。
このセラミックス材は前加工での凹凸傾向が大きく、総取り代が多いため、生産性を向上させるには1回の切込量を多くする必要がある。こうした市場ニーズは高く、多くの加工現場で課題となっている。
岡本工作機械製作所が開発したCNC精密ロータリー研削盤「PRG6DXNCシリーズ」では、1回の切込み量20μm以上を実現した実績もあり、サイクルタイムの短縮に貢献することができる。また、加工精度も平面度3μm以内の要求に対応することが可能。加工条件次第では様々なニーズに対応することができる。
「PRG6DXNCシリーズ」は、回転方式のロータリーテーブルにφ600㎜の丸形電磁チャックを搭載している。平面加工だけでなく、階段加工や凸傾向加工なども分かりやすい図形対話ソフトによって、簡単に操作を行うことができる。サイズラインアップは、φ800、φ1000、φ1200、φ1800㎜を揃える。
同社は「近年、セラミックス材は鉄系材料に変わる新しい材質として注目されている。新素材のため、市場では加工ノウハウが確立されていないこともあるが、困りごとがあれば是非一度当社に相談してほしい」としている。
PART4
セイロジャパン「自由曲面のヘール加工を実現」
ドアミラーカバーモデル
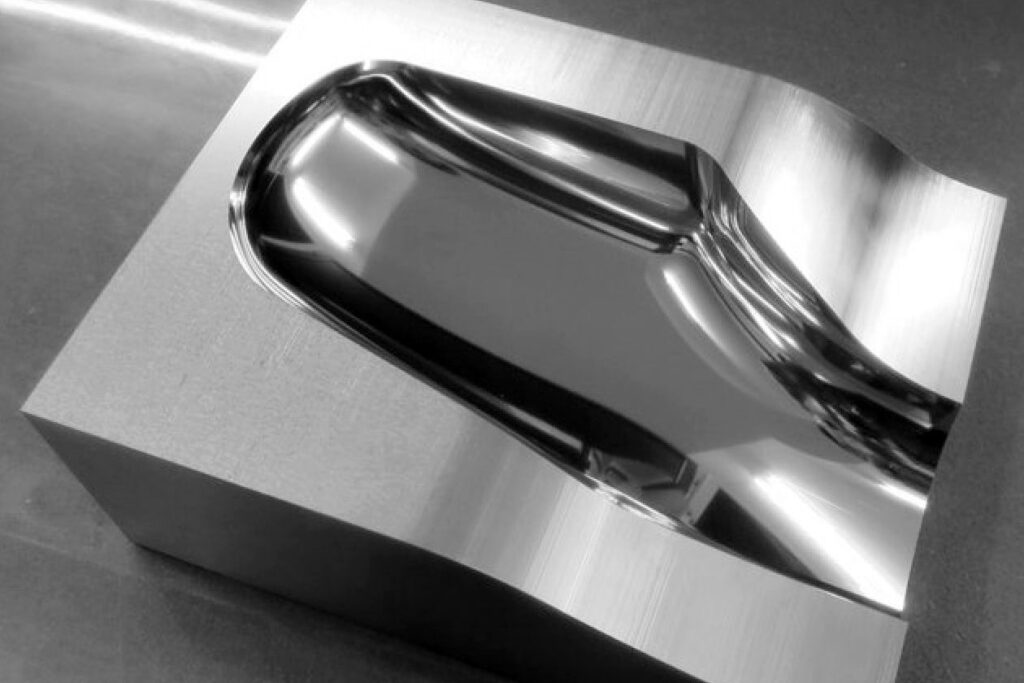
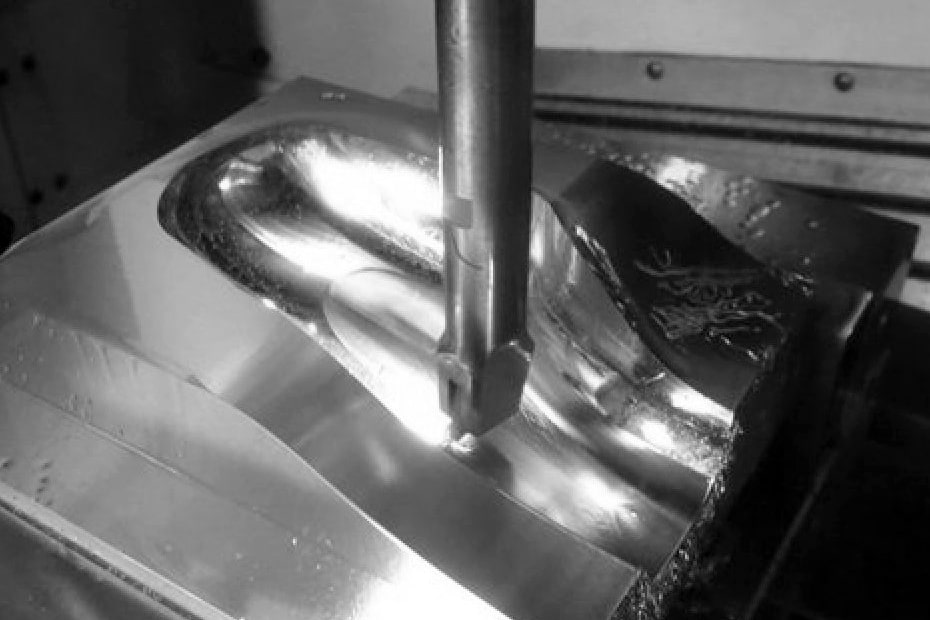
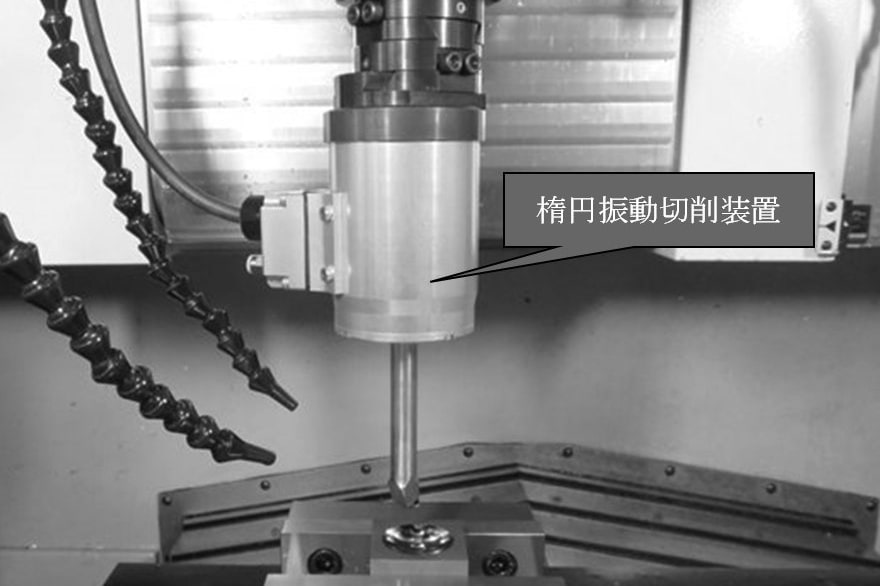
マシニングセンタでのヘール加工はこれまで、バイト形状に制約があるため、凸形状や干渉が起きないなだらかな形状など加工できる形状が限られていた。
セイロジャパンが製作したドアミラーカバーモデルのワークサンプルは、ヘール加工で深い凸型の自由曲面全体への加工を実現。これまで制約が多かったマシニングセンタでのヘール加工の可能性を広げた。
可能にしたのは、その加工方法。中仕上げに超硬エンドミルで加工するなど、ヘール加工だけでなく、複数の加工方法を組み合わせ、干渉などの問題を回避することによって、深い凹型の自由曲面全体へのヘール加工を実現した。
超硬ボールエンドミル(R3.0)を使用し、切込み0.1㎜、回転数毎分9500回転、送り速度毎秒2250㎜で中仕上げを行った後、ヘール加工で仕上げた。ヘール加工では単結晶ダイヤモンド(R1.0)と楕円振動切削装置(多賀電気製)を使用し、切込み20μm、ピックフィード20μm、送り速度毎分1000㎜という条件で加工した。
また、これらの加工パス作成に使用したのが、同社が提供する統合3次元CAD/CAMシステム「Cimatron Ver15」。サーフェス、ソリッド、メッシュ混在のデータでも全工程において作業が可能。金型製作の設計、加工軌跡作成、機上測定など全工程をサポートする専用モジュールを備え、一気通貫の統合システムとして使用できるだけでなく、個々の工程の部分最適化も図ることができる。
PART5
日進工具「ナノレベルを切削で」
円筒内面5軸加工レンズアレイ
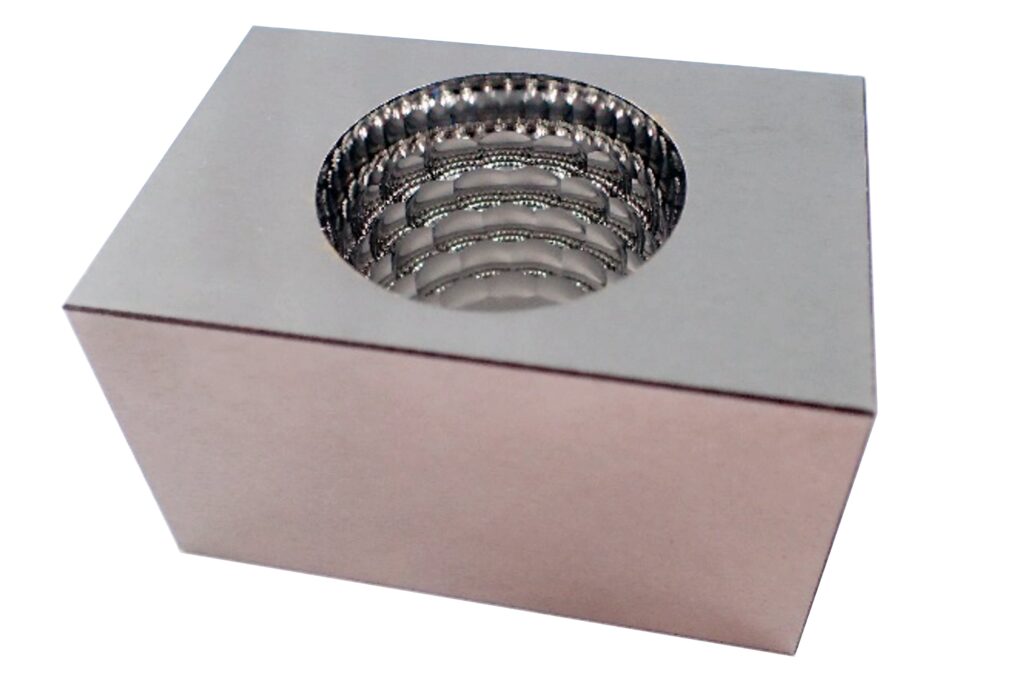
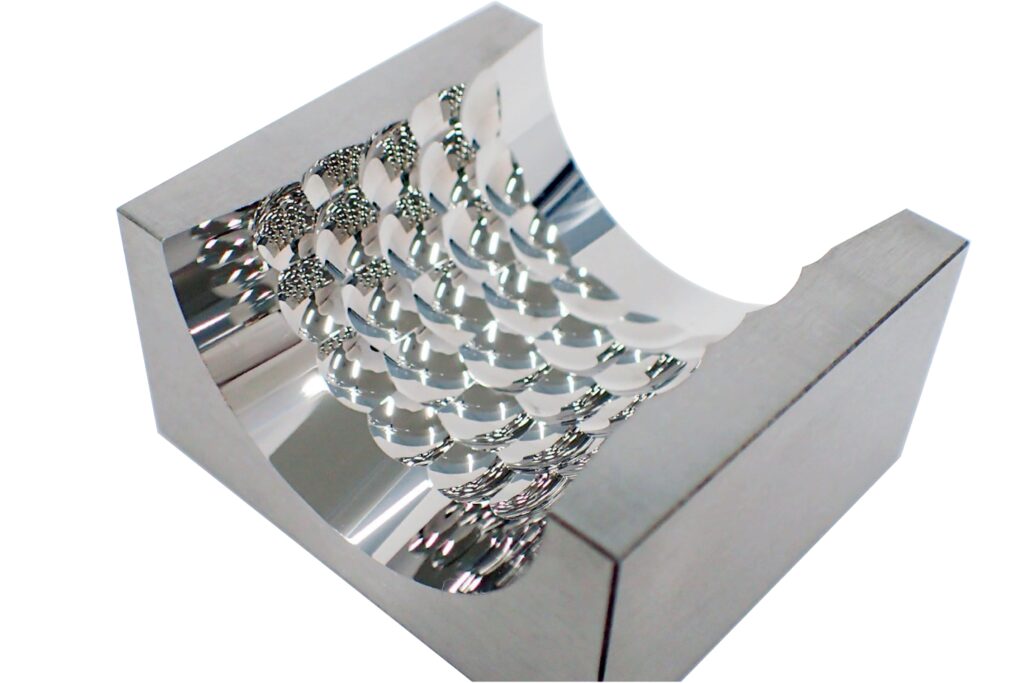
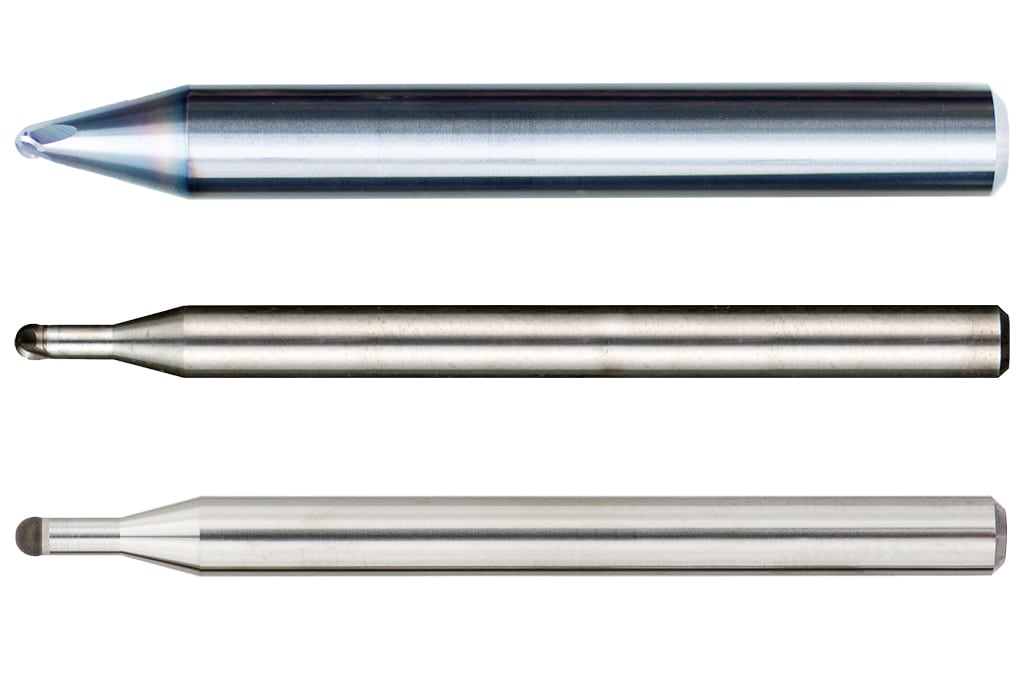
日進工具が加工したのは、5軸加工だからこそできた円筒内面レンズアレイのワーク。レンズアレイ形状で磨きが困難となることから、エンドミルによる切削のみで鏡面性を追求した。得られえた面粗度は内面テーパ部とレンズ部がそれぞれRa0.008μm、Ra0.012μmとナノレベルを達成した。
被削材はSTAVAX(52HRC)で、加工工程は計4工程。使用工具は同社の超硬、CBN、PCDの3種類を駆使した。
荒取りと中仕上げ①で使ったのは、超硬5軸MC加工用3枚刃ボールエンドミル「MSBSH330-5X R1」(写真①)。5軸の特長を活かす3枚刃・高剛性なボール形状で、高精度で高能率な加工によりトータルコストを削減する工具。今回も高剛性な刃形状で、後工程へ均一な残し代を残すことに成功した。
中仕上げ②には2枚刃のCBNスパイラルボールエンドミル「SSPB220 R1×4」(写真②)を採用。光沢のある仕上げ加工面と、刃先の切削性を向上させるスパイラルボール形状とした。
最終の仕上げ加工で活用したのは、安定した加工面を得るためにユニークな工具デザインのPCDボールエンドミル「PCDRB R1×5」(写真③)。面粗さはナノレベルに対応し、鏡面を実現した。
今回のワークについて同社では「5軸対応工具を開発したので、あえて3軸では難しい内面レンズアレイに挑戦した。5軸加工でも高精度な金型加工ができることを伝えたかった」という。また、クーラントの有無や、加工負荷の抑えるための切削条件などの「詳しいデータは問い合わせして欲しい」としている。
PART6
三井精機工業「先端径φ0.02㎜のピンを連続加工」
微細精密なマイクロニードル
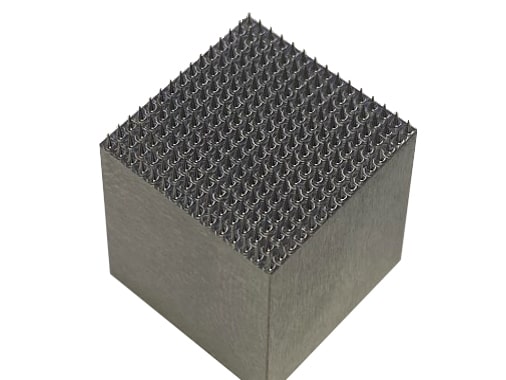
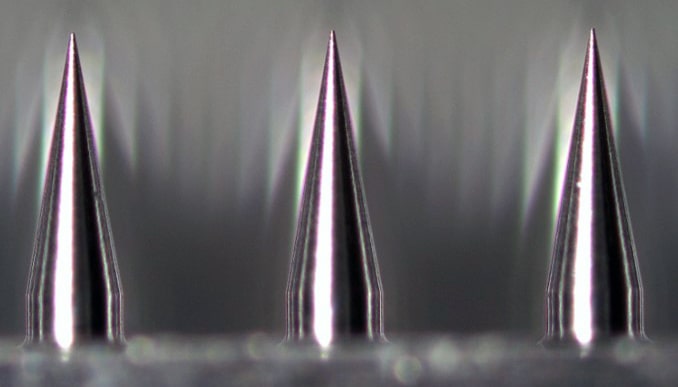
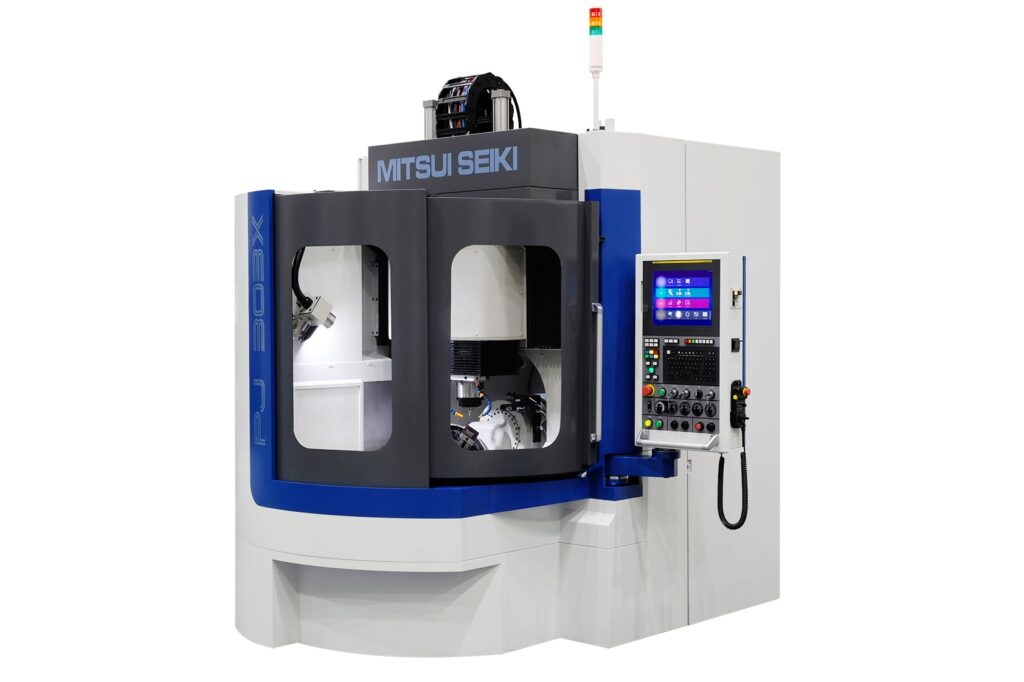
15㎜角に無数のピンが1㎜ピッチで立ち並ぶ。その数は225本。ピン1本のサイズは先端径φ0.02㎜、根本直径0.38㎜、高さ1.2㎜。三井精機工業が製作した微細精密なマイクロニードルのワークサンプルだ。
ワーク材質は「STAVAX」。CBNラジアスエンドミル(φ0.5×R0.05×1.5)を使用した。荒加工、中仕上げ、仕上げで総加工時間は12時間。加工機の主軸は毎分4万回転で、送り速度は荒加工が毎分1000㎜、中仕上げは毎分500㎜、仕上げは毎分50~500㎜で加工した。
この一連の加工で使用したのが、同社が開発したプレシジョンセンタ「PJ303
X」だ。最新の主軸熱変位補正機能や特殊熱変位キャンセル機構を搭載し、主軸・ヘッドの熱変位を大幅に抑制する他、熱変形を考慮した左右対称門型コラム構造も採用し、安定した精度での微細精密加工を実現する。
今回製作したマイクロニードルのワークサンプルでも隣接16本のピンの最大ピッチ誤差は0.9μmと安定した加工精度を実現した。マイクロニードルの他にも、レンズ金型や医療機器、電極、燃料電池などの高精度加工に適している。
また、直線軸には高速リニアモータ、回転軸DDモータを採用。回転軸2枚扉で正面操作扉の開口幅を広げたことによって、作業性を向上させた。
同社は「先端径φ0.02㎜、225本を連続で削るため、周囲温度、振動、熱変位、ミストの掛け方など基本的なことに気を抜かず加工を進めた」としている。
PART7
三菱マテリアル「65HRC以上の高硬度鋼加工」
ベベルギア向け金型を切削で
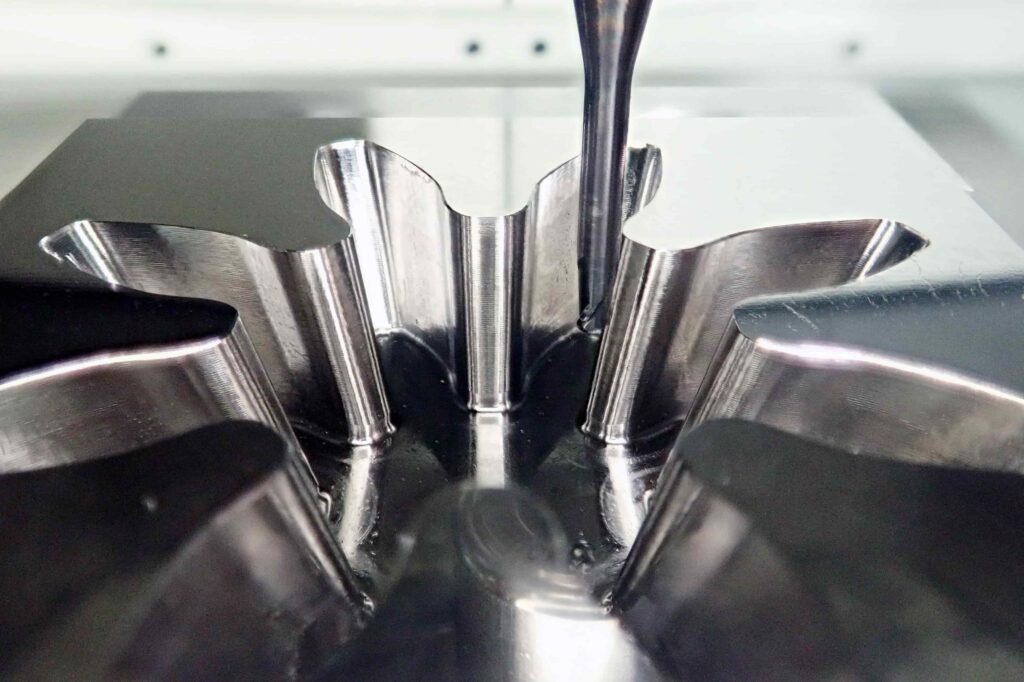
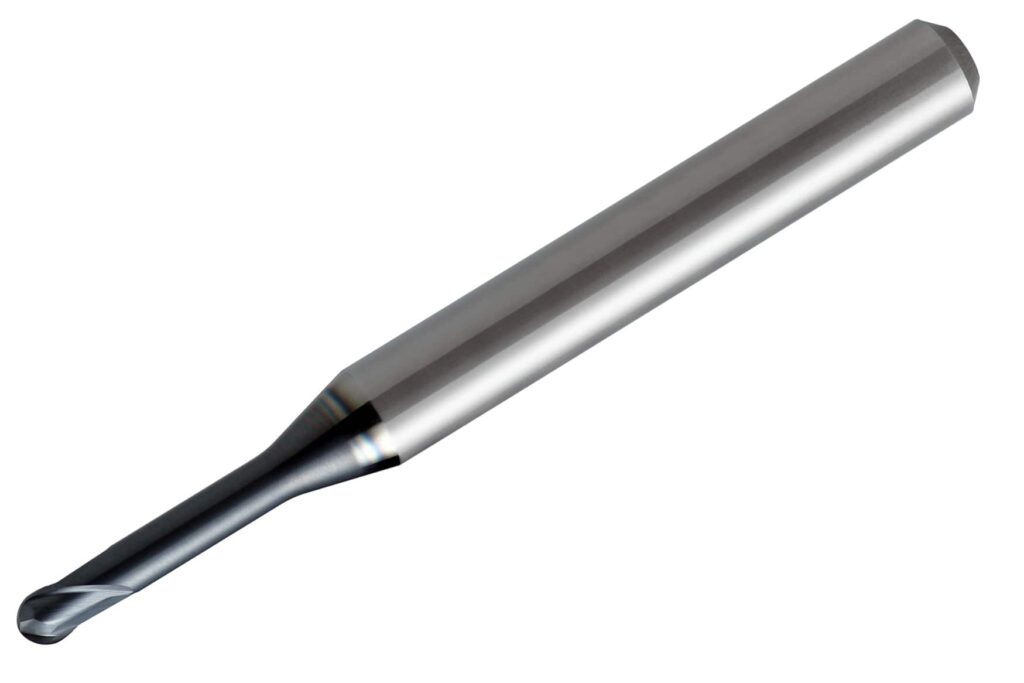
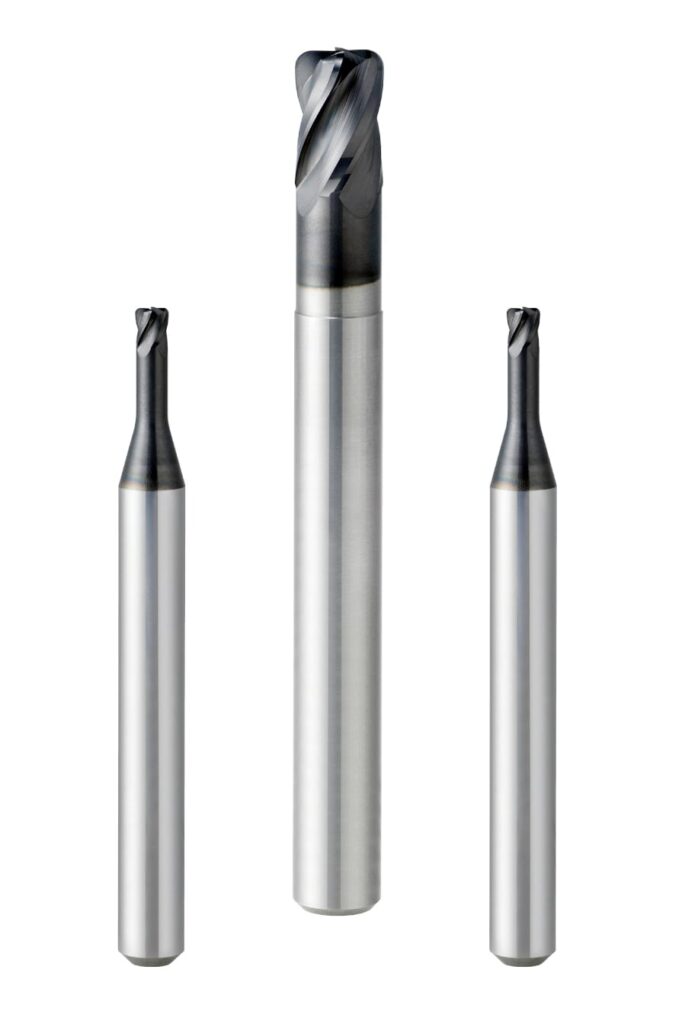
高硬度精密冷間鍛造型は高い耐久性が求められるため、使用される素材の硬度が高く、切削工具で加工するのは困難とされてきた。従来は放電加工や切削加工後に熱処理を施し、硬度を高めるなどで対応してきた。
三菱マテリアルが製作したサンプルワークは、この高硬度精密冷間鍛造型(ベベルギア向け金型)を切削工具で加工したもの。被削材は「SKH51」、ワークサイズは50×50×25㎜、使用機械は立形マシニングセンタ(HSK-E32)。
この加工を可能にしたのが、同社が開発した高硬度鋼加工用エンドミル「インパクトミラクルレボリューション」。耐酸化性・潤滑性に優れるコーティングと耐摩耗性・高密着性に優れるコーティングとの組み合わせで、優れた耐摩耗性を発揮し、65HRC以上の高硬度鋼加工を実現する。
サンプルワークの加工工程は荒から仕上げ、面取りまで8工程に分けた。面取り加工を除いた7工程で「インパクトミラクルレボリューション」シリーズを使用した。
荒加工と輪郭荒加工(1回目)では新刃形を採用し切れ刃強度を高めた2枚刃ボールエンドミルを使用。輪郭荒加工(2回目)、中仕上げ加工、壁面仕上げ加工ではボール部と外周部のシームレス化(つなぎ目なし)と強バックテーパ採用したロングネックボールエンドミルを使った。
底面仕上げ加工と上面ならし加工では、シームレス形状とワイパー刃・強バックテーパを採用し、チッピングの抑制と高精度加工が可能な4枚刃ラジアスエンドミルを使用した。
記者の目
ワークサンプルから見えてくるのは、時代の加工トレンドやニーズ。将来拡大する市場があったり、課題があったり、革新的だったりするから、それを分かりやすく伝えるためにメーカーはサンプルを作るからだ。
今回もヘール加工や5軸加工、難削材や高硬度材、微細加工などのワークを紹介した。いずれも金型メーカーが課題だったり、今後の成長を見込めたりする分野だろう。
重要なのは、それらから何を感じるかだ。特殊な金型を開発したある技術者は「興味と関係ないワークから発想を得ることが多い」という。頭にある技術同士がつながり、新たなアイデアが沸くからだろう。多くのワークを見ることは、こうした技術の抽斗(ひきだし)を増やすことにつながるはずだ。
金型新聞 2021年12月10日
関連記事
7月6~9日 ポートメッセなごや 294社が競演 金型加工技術に関する専門展「インターモールド名古屋」(主催:日本金型工業会、運営:インターモールド振興会)が7月6日~9日まで、ポートメッセなごや(名古屋市港区)で開催さ…
今なおリーマン・ショック前の7割の生産額―。プラスチック金型は、リーマン前の水準に戻った鍛造型や8割のプレス金型などと比べると回復していない。技術力、そして生産力でも圧倒的に世界をリードした「日本のお家芸」の復活のカギ…
金型メーカーアンケート 次世代の匠に必要な技は? 熟練の金型職人が持つ「匠の技」を機械に行わせたり数値化したりする取り組みは広がり続けている。新技術が登場する中、「匠」に求められる能力に変化はあるのか。それを…
金型業界含め国内製造業は慢性的な人手不足を抱え、加工や測定工程で自動化を図ることが大きな課題となっている。そのため、これまで複数の機械で加工していた加工工程を1台の機械に集約し、段取り工程の削減や短縮、さらに、工程間の搬…