自動車のフィックスドウインドウやクォーターウィンドウ。その成形コストや歩留まりを改善し、環境に配慮した金型も設計した。顧客製品設計の最終確認会にも出席しアドバイスする。それらが評価され、令和2年度「現代の名工」に選ばれた…
オギハラ 長谷川 和夫 社長
〜新素材の金型に挑む〜
いかにトライ数を減らすか
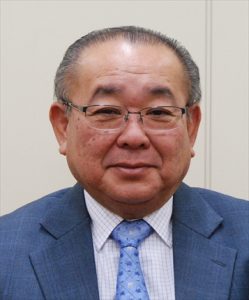
1954年生まれ、静岡県出身。77年日本大学卒業後、オギハラ入社、86年オギハラ・アメリカ・コーポレーション(現タイサミット・アメリカ・コーポレーション)、2013年同副社長、16年1月オギハラ社長に就任。
「1988年にホンダのNSXに関わったのがきっかけ。オールアルミボディを採用した自動車で、当社では一部の金型を手掛け、量産はほぼ全てのアルミ部品の生産に携わった。当時は材料の開発が進んでおらず、プレスや溶接など加工に苦労した記憶がある」
―当時に比べて、何が変わりましたか。
「材料と接合技術の進化が大きいのではないか。アルミ材の開発が進み、絞るときに割れ難くなるなど、当時に比べて格段にプレスしやすくなった。また、接合技術も進歩した。抵抗溶接だけでなく、トグルロック、リベット留め、接着剤など様々な工法が開発され、アルミ材で自動車を組めるようになっている」
―一般のプレス用金型との違いは。
「最大の難点はスプリングバックだろう。高張力鋼坂(ハイテン材)と同じくらい大きいので、設計どおりの形状を出すのが難しい。当社では、10年ほど前から導入した3Dスキャナを使って工程ごとに全てスキャンし、データを蓄積して成形シミュレーションの精度を上げている。ただ、トライアウトの回数は減っているが、まだまだ課題は多い」
「また、せん断ピアス加工などの加工くずの処理も課題だ。アルミは加工くずが出やすく、これが加工面につくと面品位の悪化に繋がるなどトラブルの原因になる。金型にディンプル(くぼみ)を付けて加工くずを逃がす処理や、ブローを取り付けて吸い込むほか、鏡面にしてバリを抑制するなど様々な工夫を加えている」
技能に頼らない作り方
―今後のアルミ材活用の動きをどう見ますか。
「30年以上前からフォード社(米)のリンカーンでは、フードパネルにアルミ材を使っていた。アメリカでは当時から『フタ物はアルミ材』という考えが主流だった。今後は日本の自動車メーカーでも採用が進むだろう。また、アルミと高張力鋼坂(ハイテン材)、アルミと炭素繊維強化プラスチック(CFRP)など複合化の流れも拡大していくと見ている」
アルミ材活用という点ではダイカストという選択肢もあります。―
「プレスの強みは量産性。生産数やコストによって使い分けていくことが重要だろう」
―今後の展開は。
「シミュレーションの精度を上げ、戻り作業のない生産体制を構築する。さらに、アメリカや、中国工場の量産で得た情報をフィードバックして金型に織り込み、規格化することで、人の技量に頼らない金型づくりに取り組んでいく」
―金型メーカーができることは。
「今後もアルミに限らず様々な技術開発が進むだろう。コストやデザインなどあらゆる側面から最適な車づくりを追求するのが完成車メーカー。我々金型メーカーは、常にそうした動きに対応できるように準備しておくことが重要だ」
金型新聞 平成29年(2017年)5月12日号
関連記事
微細加工の大型化に対応 工作機械の「マザーマシン」として世界で高い評価を得ている安田工業。近年、金型業界でもニーズが高まる微細加工向けとしてJIMTOF2016で「YMC650」を発表し微細加工分野の開拓に努めている。…
ウッデホルムやボーラーブランドで知られる特殊鋼メーカーのアッサブジャパン。昨年には、日本進出70周年を迎え、金属3Dプリンタ(AM)事業の強化や、真空炉を設備投資するなど積極的に事業展開を進めている。世界中で販売するグロ…
CAEを活用しているのは企業だけではない。岩手大学では、樹脂流動解析ソフト「3DTimon」(東レエンジニアリングDソリューションズ)を学生の教育で利用している。樹脂を流す際、最適なゲート位置などを自らの勘や経験から教え…
「設計の効率化は業務フロー全体を見直さないと意味がない」。そう話すのは、日本デザインエンジニアリングの岩壁清行社長。同氏は長年自身も金型づくりに携わり、近年ではフィリピンで設計支援を手掛ける。また、20年以上前から、日…