令和元年に新社長に就任したオークマ・家城淳社長。市場が不透明化している中、「機電情知一体」「日本で作って世界で勝つ」を掲げるオークマの今後について家城社長の思いを聞いた。 家城淳社長愛知県出身。85年大隈鉄工所(現オ…
【対談】日本金型工業会 小出 悟 会長 ×ロボコム・アンド・エフエイコム 天野 眞也 社長
デジタル技術を活用してビジネスモデルや業務プロセスを変革するデジタルトランスフォーメーション(DX)。金型でもその重要性は誰もが認めるところ。しかし、金型づくりでは、人が介在する部分が多かったり、デジタル化を進めづらかったり簡単ではない。では、金型業界において、DXはどのように考え、取り組むべきなのか。製造業のDXをサポートするロボコム・アンド・エフエイコム(以下R&F)の天野眞也社長に、金型業界を代表し、日本金型工業会の小出悟会長が取材した。
※ロボコム・アンド・エフエイコム
DXやスマートファクトリーをサポートする「チームクロスFA」の幹事会社の1社。チームクロスFAは工程設計、ロボット、エンジニアリングなどに強みを持つ7社とパートナー企業で構成。R&Fでは、6月にDX実現のためのデジタルファクトリーを開設した。
DXでカンコツ強みに
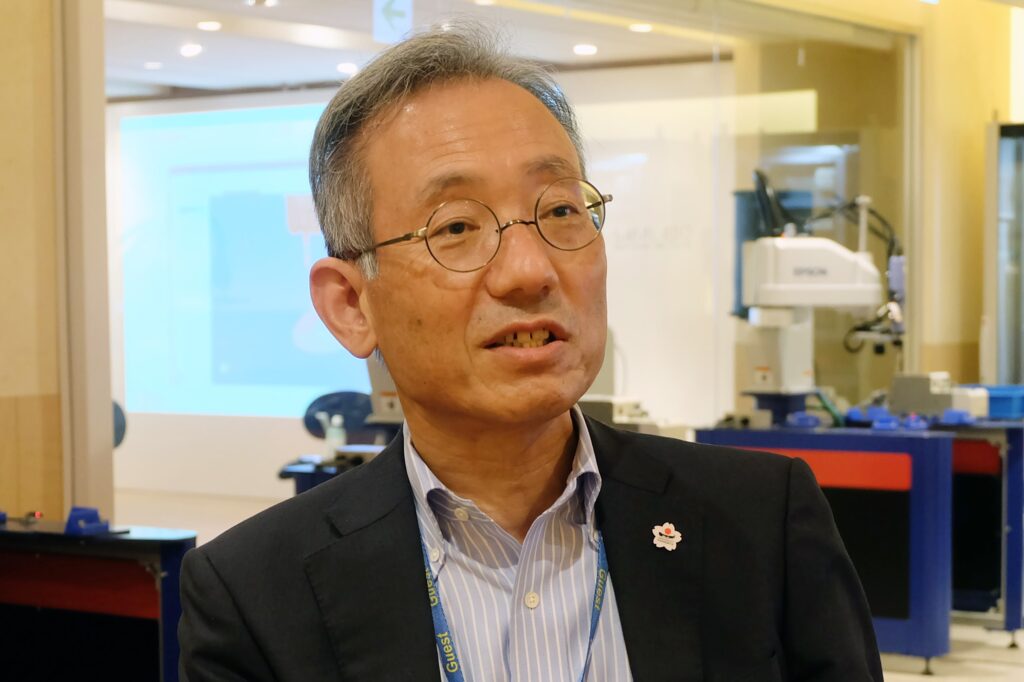
小出 本題に入る前にまず貴社の概要や取り組みを教えてください。
天野 当社が運営の主体となっている「チームクロスFA」から説明するほうが分かりやすいと思います。スマートファクトリーを実現するには、建物、IT、人、設備全てのノウハウが必要です。しかし残念ながら1社で全て提供するのは難しい。そこで工程設計、ロボット、エンジニアリングなどに強みを持つ7社とパートナー企業が集まり、スマートファクトリーやDXを支援するのがチームクロスFAです。その幹事企業の1社がロボコム・アンド・エフエイコムになります。
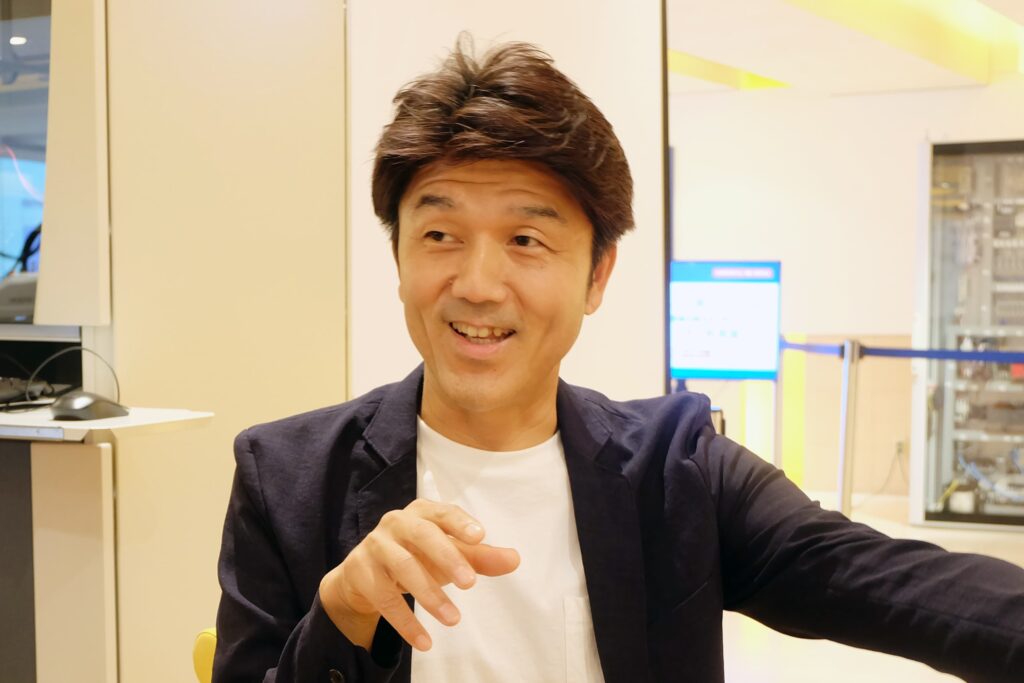
小出 スマートファクトリーやDXを実現する集団というわけですね。まず、スマートファクトリーすなわちデジタルを活用した工場が必要だと思った理由は何でしょう。
天野 日本の製造業のカンコツは世界最強です。今後も、それだけでものづくりができるなら世界一でしょう。しかし、デジタルが登場してくると、カンコツだけでは戦えない。強みのある今のうちに、カンコツやすり合わせ能力をデジタル化すべきだと思います。
例えば原作が面白くない脚本を映画化してもつまらない。それと同じでカンコツがないものづくりをデジタル化しても意味がない。逆に世界最強のカンコツをデジタル化できれば強みに変わります。ただ時間があまりないので急ぐべきです。
小出 全く同感ですね。あと5年もすれば、カンコツを持つ技能者は減っていきます。それまでに強みをデジタルで補完させていくことは急務です。しかし、金型業界はデジタルに精通した人が豊富ではない。デジタル化をどう進めていくべきなのか分からない企業も多い。何ができて、何ができないのかを見極める必要があります。
天野 私もその通りだと思います。まずは自社のデジタル化を進める上で「課題は何か」、「何から取り組むべきか」などを理解する必要があります。ただ、皆さんは金型づくりのプロですが、デジタルのプロではなく、そうした診断が得意というわけではない。診断をして最適な提案をするのが我々の役目だと思っています。
小出 どういうことでしょう。
天野 DXを進めるには、頭が痛い時に単に頭痛薬を処方するような対処療法ではダメだと思います。頭痛の本当の理由は何かを探る必要がある。運動不足かもしれないし、食事に問題があるかもしれない。皆さんと議論しながら、会社ごとの本当の課題を見極め、解決策を提示するのが我々の役割だと思っています。
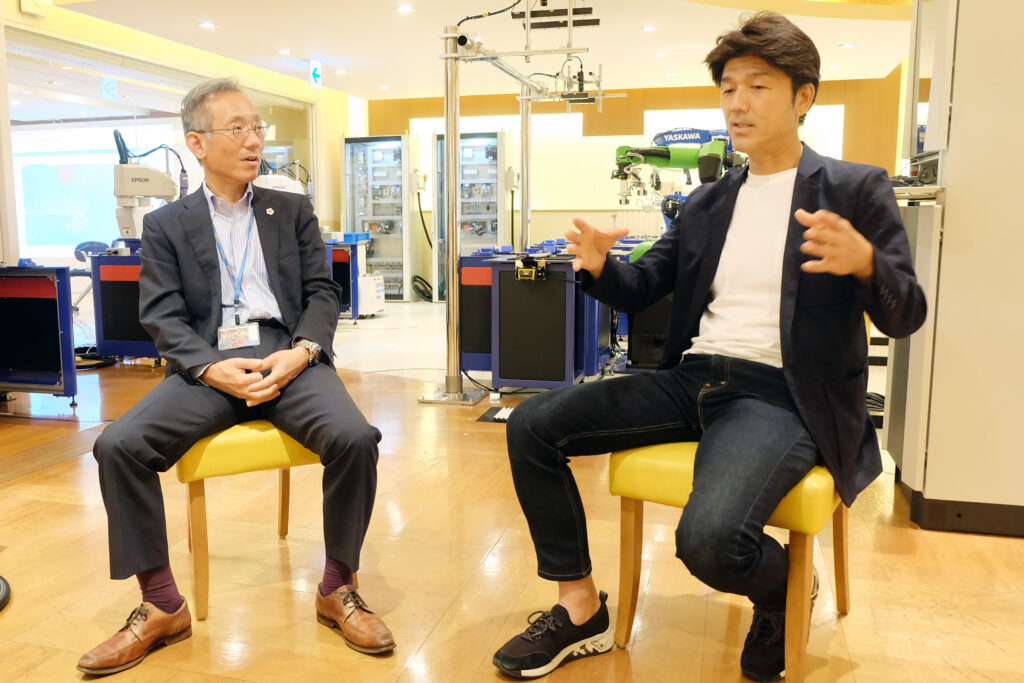
デジタルツインは未来予測
小出 DXと言っても様々な進め方があると思います。最近は仮想空間で現実を再現するデジタルツインが注目を集めています。デジタルツインで可能になることにどのようなものがありますか。
天野 まずはリアルな工場をデジタルな工場に変えていく必要があると思います。それは、ものづくりを言語化(データ化)するということでもあります。その中核となる技術の一つが、デジタルツインです。
そして、デジタルツインが可能にするのは言うなれば、未来予測でしょう。よく例に出すのが「グーグルマップ」です。昔のカーナビは目的地に到着はできても、時間まで正確ではありませんでした。しかし、グーグルマップは到着時間もかなり正確です。
同じことが工場でも可能です。工場の設備ラインをデジタル化して、シミュレーションをする。これまでは設備の条件など固定のパラメータしかシミュレートできませんでした。しかし、デジタルツインでは、人の動きや工場の外も含めた条件も加味できるので、かなり正確なアウトプットが把握できます。予測と現実が一致すれば、設計と製造現場の対立などもなくなると思います。
小出 工場をデジタルコピーするわけですよね。しかし、物理的な作業がある工場でも人の動きの把握や動作分析ができていません。設計者の頭の中はなおさらです。この部分をどうお考えですか。
天野 おっしゃる通りで、図面や工場ラインなどをデジタル化するのは比較的簡単ですが、技能者の頭の中や、ベテランの判断のデジタル化は難しい。
R&Fでは現在、過去に加工した類似ワークを基にAIで自動見積りしたり、チーム企業からCAMデータを集めて、パスが最適かどうかなどを記録したりしています。ワークに関して言えば過去に9割は似た加工をしていますし、CAMオペレータの頭の中も何とか言語化できると考えています。
小出 意識を持ってデータを集める必要がありますね。
天野 そうですね、グランドデザインが必要だと思います。AI見積りはオープンにできれば皆さんのお役に立てるのではないかと考えています。
ルーティーン領域をデジタル化すべき
小出 デジタル化の重要性は分かりましたが、金型は部品加工とは異なり、人が関わる部分が少なくありません。どこをどうデジタル化していくべきでしょうか。
天野 ものづくりにはクリエイティブ領域とルーティーン領域があると思います。微細な金型加工や金型の組付けなど人が不可欠なのがクリエイティブ領域で、金型は他の製造業に比べ、その領域が広い。一方で、簡単なパーツの設計業務や、金型保管などはデジタルを活用すれば楽になる。
こうしたルーティーン領域をDXで効率化し、クリエイティブ領域に必要な人材の育成に注力すべきではないでしょうか。
小出 私もそう思います。ルーティーン部分のDX化を議論しながら、一緒に進めていければいいですね。
天野 是非お願いします。また、どんな業界でも協調領域と競争領域があると思いますが、協調領域の部分にルーティーンな作業が多いように思います。例えば、お弁当の製造ラインでは、どの工場でもほぼ作業は同じです。金型づくりでも類似作業をしている部分も多いと思うので、そうした部分のDX化をサポートさせて頂きたいですね。
意思決定の速度アップを
小出 デジタル化は不可欠ですが、当工業会の会員企業は、小規模から大規模まで幅が広く、全社が取り組めるわけではありません。
天野 そうですね。資本と技術は必要だと思います。しかし、デジタル化への意思決定のスピードアップは規模や技術に関係なくできるのではないでしょうか。我々がそうだったからです。
小出 どういうことでしょうか。
天野 当社も資本は潤沢ではなく、技術も突出しているわけではありませんでした。しかし、SIerでデジタルマーケティングに注力する企業は少なく、10年間真面目にデジタルプロモーションと技術力アップに注力してきました。するとそれなりのところまで来ることができました。
言い方が厳しくなりますが、右肩下がりにもかかわらず、現状で食べていけるから意思決定が遅れるのだと思います。
小出 そうですね。昨年、当工業会で打ち出した「令和時代の金型ビジョン」でも“ゆでカエル”にならないように変化しましょうと訴えました。今が変化する最後の機会だと思っています。
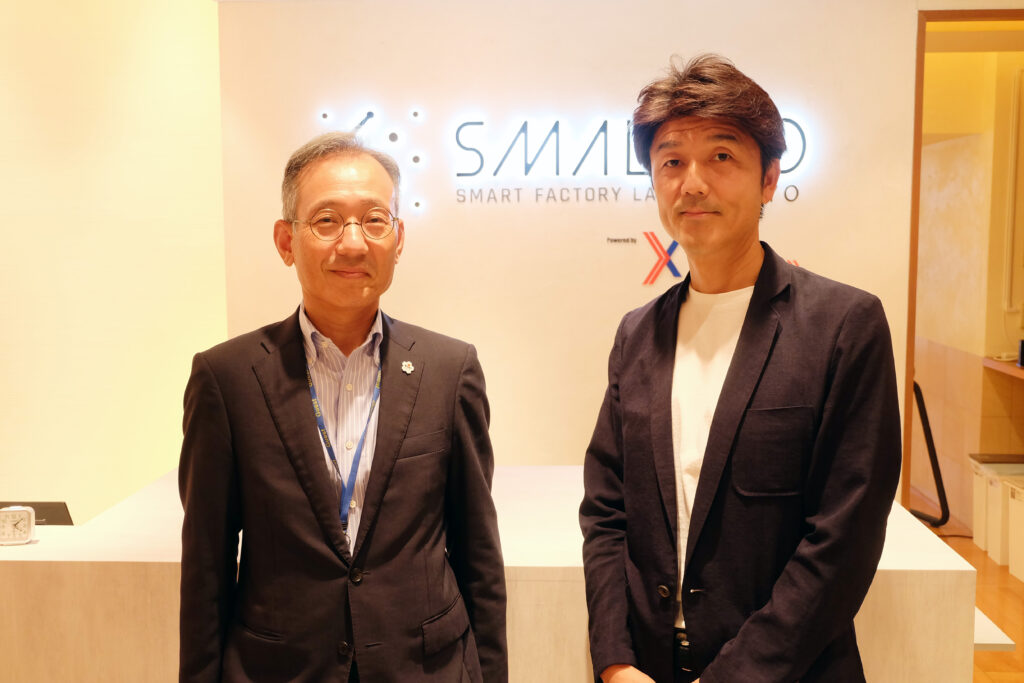
デジタル化は今日から出来ることから始めよ
小出 ちなみに、デジタル化はどうすれば急げますか。データがないとダメでしょうか。
天野 やるならば準備は今日からでもすべきです。どの企業でも完璧なデータをそろえるのは無理です。「準備ができてから」ではいつまでたっても始められません。紙の帳票をなくすとか、FAXをやめるなど小さなことからでいいと思います。
自動運転を例によく話すのですが、ステージ2でも運転は楽になります。それと同じでいきなり完璧を目指すことは難しい。今、人が100判断していることをデータが20でも判断できれば楽になります。
小出 当社でも、長年「紙図面を減らせないか」と言っているのですが、減りません。図面の本質は情報の集合体です。図面は改廃が多いので、デジタルのほうが楽だと思うのですが、こうした課題はありますか。
天野 同じような悩みはあります。現場は変わろうとしないこともありますので、その場合はルールを変えるか、デジタル化を進めるためのツールを導入し、システム化するようにしています。
小出 他に留意することはありますか。
天野 やはりDXを進めるには、トップの理解がないとダメですね。大手企業では事業部長以上でしょうか。現場だけの判断だと部分最適になってしまうことが多いからです。例えば、製造1課から5課まである企業があるとします。ボトルネックは2課なのに、先進的な取り組みをしている1課と3課だけがデジタル化を進める。こうなると、全体での最適化は難しくなります。
小出 最後に貴社が目指すところを教えてください。
天野 我々の狙いの一つは産業をシステム化し、輸出することです。例えばベトナムで弁当の製造ラインが必要な場合、その製造ラインを売って終わりではなく、構築の仕組みを売る。しかもハードだけでなくモジュール化してシステムで売る。いずれはサブスクリプション(従量課金型)で提供できればと思います。
もう一つはエンジニアの地位向上です。若いエンジニアに話を聞くと、頭で考えたことがきちんとカタチになることが楽しいと言います。そのために必要なスキルをキチンとスコア化して、そのスコアがきちんと報酬につながるような仕組みを作りたいですね。
小出 本日はありがとうございました。
金型新聞 2021年9月10日
関連記事
選ばれる企業になるために経営者の美意識によって顧客の感性に訴求する 当社は1986年に創業したカーボン素材などの高精度加工を得意とする従業員13人の会社です。主に半導体の製造工程で使用されるカーボン製治具などを手掛けてお…
「設計の効率化は業務フロー全体を見直さないと意味がない」。そう話すのは、日本デザインエンジニアリングの岩壁清行社長。同氏は長年自身も金型づくりに携わり、近年ではフィリピンで設計支援を手掛ける。また、20年以上前から、日…
今年3月、岩手大学と自動車部品メーカーのトヨタ紡織は生産技術開発を中心とした連携で包括協定を結んだ。両者は今後6年に渡り、生産技術のほか、幅広い分野で共同研究を進めていく。「大学全体で連携し、技術開発だけでなく、学生の…
コストダウン、納期短縮図る 自動車用アルミダイカスト部品メーカーの美濃工業(岐阜県中津川市、0573-66-1025)は2021年3月、埼玉県熊谷市に「熊谷金型センター」を設立し、金型製造を開始した。20年10月には静岡…